Study on the Spatial Distribution of Argon Bubbles in a Steel Slab Continuous Casting Strand
Steel Research International(2021)SCI 2区SCI 3区
Yanshan Univ | Shougang Grp Co Ltd
Abstract
The spatial distribution of argon bubbles in an 1800 mm × 230 mm continuous casting strand under different casting speeds and argon flow rates are studied through the numerical simulation using the Euler–Euler‐multiple‐size‐group approach. The calculated fluid flow is validated with water modeling and nail board measurements of industrial trials. Argon bubbles with diameter of 2 mm are injected into the submerged entry nozzle (SEN). The speed of the molten steel near the SEN decreased with the casting speed increasing and increased with the argon flow rate increasing. Most of argon bubbles are larger than 4.5 mm inside the mold at the casting speed of 0.6 m min−1 and the argon flow rate of 18 NL min−1. The breakup rate of bubbles inside the mold increased with the increasing of the casting speed and the coalescence rate increased with the increasing of the argon flow rate. The coalescence and breakage of argon bubbles inside the mold mainly occurred during the rising of bubbles to the top surface and the moving of bubbles with the steel jet to the narrow face. The average diameter of bubbles decreased when the casting speed increased and the diameter increased when the argon flow rate increased.
MoreTranslated text
Key words
argon bubbles,multiple-size-group model,nail board measurement,water modeling
求助PDF
上传PDF
View via Publisher
AI Read Science
AI Summary
AI Summary is the key point extracted automatically understanding the full text of the paper, including the background, methods, results, conclusions, icons and other key content, so that you can get the outline of the paper at a glance.
Example
Background
Key content
Introduction
Methods
Results
Related work
Fund
Key content
- Pretraining has recently greatly promoted the development of natural language processing (NLP)
- We show that M6 outperforms the baselines in multimodal downstream tasks, and the large M6 with 10 parameters can reach a better performance
- We propose a method called M6 that is able to process information of multiple modalities and perform both single-modal and cross-modal understanding and generation
- The model is scaled to large model with 10 billion parameters with sophisticated deployment, and the 10 -parameter M6-large is the largest pretrained model in Chinese
- Experimental results show that our proposed M6 outperforms the baseline in a number of downstream tasks concerning both single modality and multiple modalities We will continue the pretraining of extremely large models by increasing data to explore the limit of its performance
Upload PDF to Generate Summary
Must-Reading Tree
Example
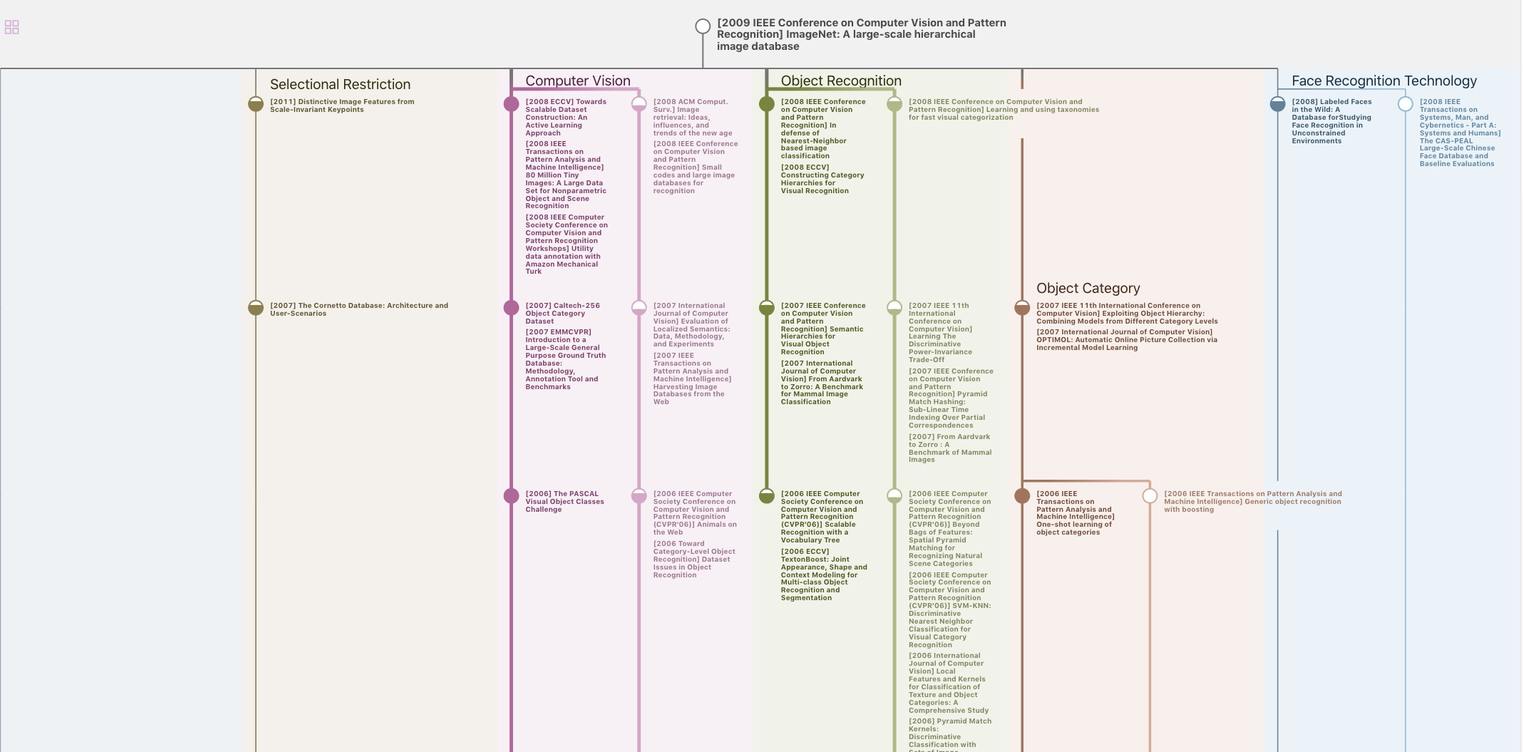
Generate MRT to find the research sequence of this paper
Related Papers
Chemical Engineering Science 2022
被引用2
Canadian Metallurgical Quarterly 2022
被引用1
INTERNATIONAL JOURNAL OF NUMERICAL METHODS FOR HEAT & FLUID FLOW 2023
被引用3
Metals 2023
被引用1
Metals 2023
被引用2
STEEL RESEARCH INTERNATIONAL 2024
被引用0
Metallurgical Research & Technology 2024
被引用0
Effect of Breakup and Coalescence Kernels on Polydispersed Bubbly Flow in Continuous Casting Mold
INTERNATIONAL JOURNAL OF MULTIPHASE FLOW 2024
被引用0
Data Disclaimer
The page data are from open Internet sources, cooperative publishers and automatic analysis results through AI technology. We do not make any commitments and guarantees for the validity, accuracy, correctness, reliability, completeness and timeliness of the page data. If you have any questions, please contact us by email: report@aminer.cn
Chat Paper