Comparative Multi-Modal, Multi-Scale Residual Stress Evaluation in SLM 3D-Printed Al-Si-Mg Alloy (RS-300) Parts
METALS(2021)
摘要
SLM additive manufacturing has demonstrated great potential for aerospace applications when structural elements of individual design and/or complex shape need to be promptly supplied. 3D-printable AlSi10Mg (RS-300) alloy is widely used for the fabrication of different structures in the aerospace industry. The importance of the evaluation of residual stresses that arise as a result of the 3D-printing process' complex thermal history is widely discussed in literature, but systematic assessment remains lacking for their magnitude, spatial distribution, and comparative analysis of different evaluation techniques. In this study, we report the results of a systematic study of residual stresses in 3D-printed double tower shaped samples using several approaches: the contour method, blind hole drilling laser speckle interferometry, X-ray diffraction, and Xe pFIB-DIC micro-ring-core milling analysis. We show that a high level of tensile and compressive residual stresses is inherited from SLM 3D-printing and retained for longer than 6 months. The stresses vary (from -80 to +180 MPa) over a significant proportion of the material yield stress (from -1/3 to 3/4). All residual stress evaluation techniques considered returned comparable values of residual stresses, regardless of dramatically different dimensional scales, which ranged from millimeters for the contour method, laser speckle interferometry, and XRD down to small fractions of a mm (70 mu m) for Xe pFIB-DIC ring-core drilling. The use of residual stress evaluation is discussed in the context of optimizing printing strategies to enhance mechanical performance and long-term durability.
更多查看译文
关键词
SLM, Al-Si-Mg alloy, residual stress, contour measurements, laser speckle-pattern interferometry, Xe pFIB-DIC, FEniCS
AI 理解论文
溯源树
样例
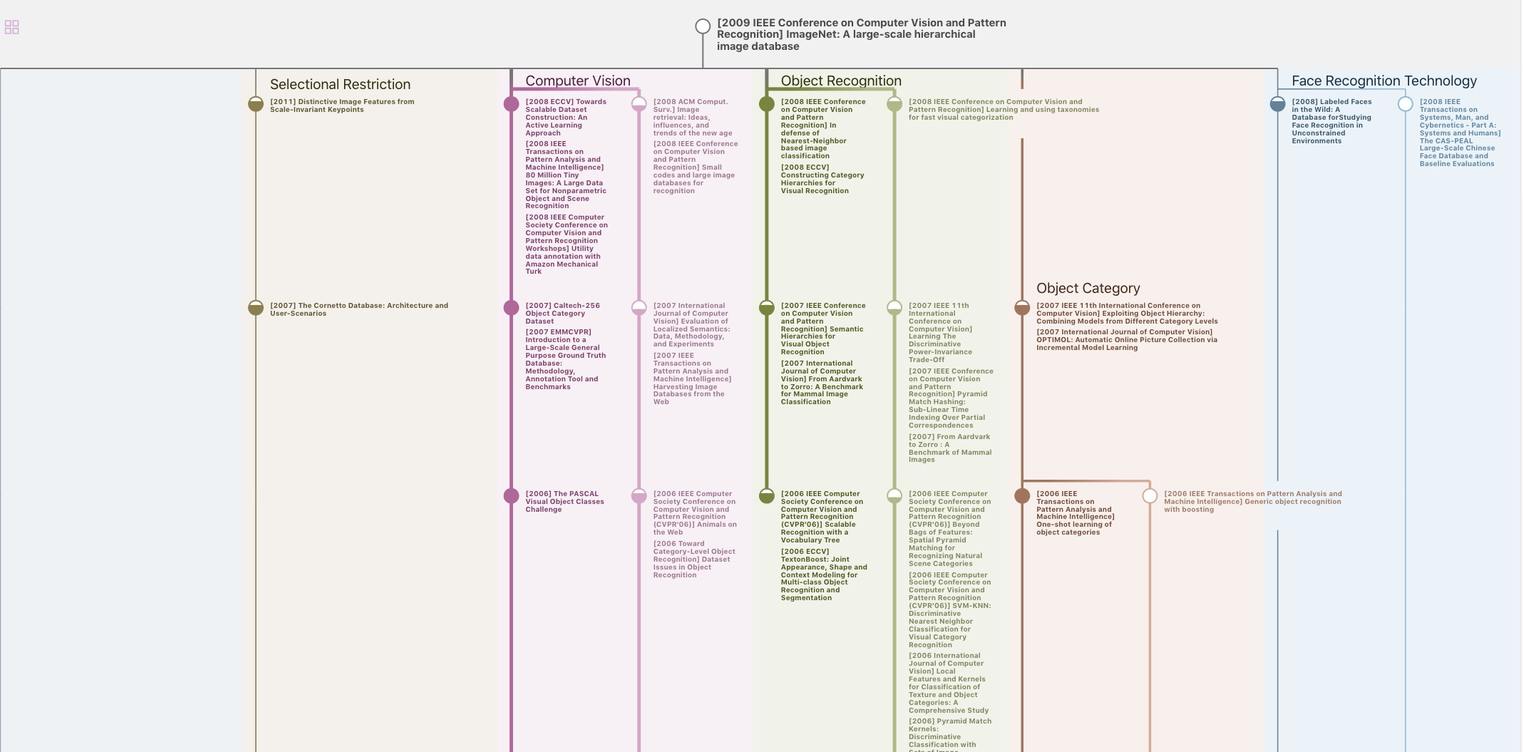
生成溯源树,研究论文发展脉络
Chat Paper
正在生成论文摘要