Ceramic Heat Pipe for Thermal Management of a High Frequency Inductor
2021 AIAA/IEEE Electric Aircraft Technologies Symposium (EATS)(2021)
摘要
As the power density of electric machines and power electronics continues to increase to meet the demands of more electric aircraft, the thermal management of these devices becomes increasingly important. Ideally, the thermal management solution of the device should have high thermal conductivity and be electrically insulating so that it can be directly integrated with the device in question. Technical ceramics are a class of materials that meet these two requirements. Direct liquid cooling by submerging electric components in a dielectric fluid is an alternate option, but adds system complexity and may incur pumping loss. In this work, the thermal management solution for a high frequency inductor is presented. A conventional wicked heat pipe is designed that is made from a solid ceramic case with a sintered ceramic wick. This heat pipe can provide structural support for the core and windings and is electrically insulating, so it does not incur any additional eddy current losses from the high frequency magnetic fields. It does not require additional pumping power, because conventional wicked heat pipes are passive devices. In this paper, the manufacturing process of the ceramic heat pipe is also presented. It is shown that the sintering of large diameter spherical ceramic particles is difficult due to their high specific surface area and low surface free energy. To overcome this difficulty, a flux material was used to initiate liquid phase sintering. The results of the sintering trials show that for the 120 μm diameter α-Al
2
O
3
powder selected for the wick, the combination of 1650°C sintering temperature and the addition of 5 wt% talc sintered the porous matrix together sufficiently for use as a heat pipe wick.
更多查看译文
AI 理解论文
溯源树
样例
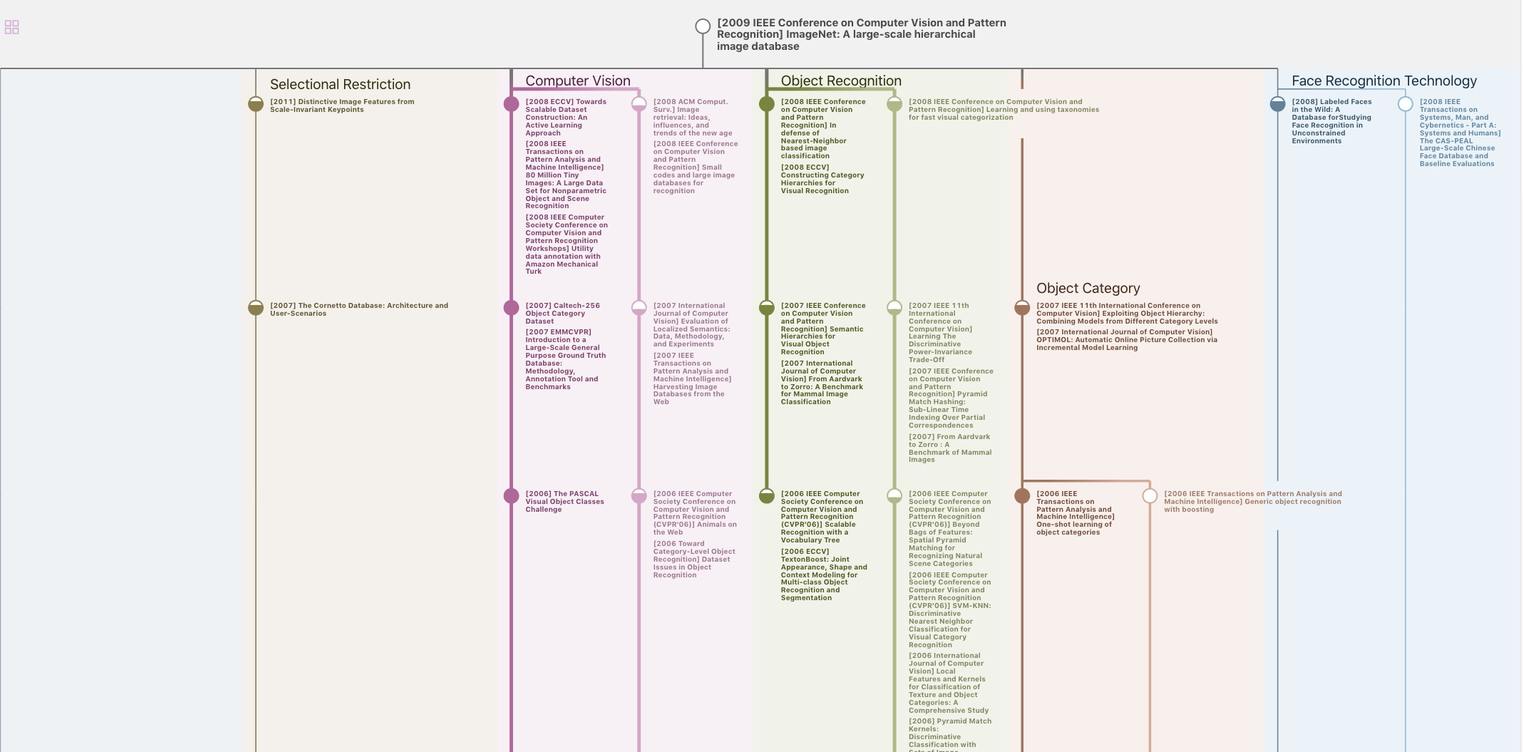
生成溯源树,研究论文发展脉络
Chat Paper
正在生成论文摘要