Optimizing the axial distance of the nozzle to the engine shell to cool the maximum fluid flow
INTERNATIONAL JOURNAL OF NONLINEAR ANALYSIS AND APPLICATIONS(2022)
摘要
The purpose of this paper is to obtain the optimal axial distance from the nozzle to the motor shell for suction of the maximum flow rate of the cooling fluid. Given that there is no laboratory data to evaluate numerical analysis, an attempt was made to validate the numerical coefficient of the NACA0012 blade lift by numerical method to validate the numerical method and compare it with its existing laboratory results. As you can see from the results, the distance between the nozzle and the motor has a very small effect on the cooling flow. In fact, this shows that with the changes in axial distance in the mentioned range (between 0 and 2.5 cm), the amount of suction caused by the hot jet of the hot nozzle output of the nozzle has a very small effect on the cooling flow. To check the suction rate of the nozzle output jet on the cooling flow rate, the problem for different discharge nozzles is numerically analyzed to see how much the effect of the nozzle output fluid on the cooling fluid discharge flow is. The coolant flow of the Flow rate engine nozzle does not change much. This factor indicates that the flow rate of the engine coolant flow is mostly due to the pressure of the coolant itself and does not depend on the suction jet of the nozzle output. In this section, the effect of increasing the length of the engine shell on the cooling rate of the engine cooling is discussed. In this analysis, the shell length was increased by 6.5 cm. The increase in shell length is done with a constant diameter. As the shell length increased, the cooling flow rate increased significantly. As the shell length increases, the cooling flow rate increases by about 52% at the relative inlet pressure of 15,000 Pascals.
更多查看译文
关键词
nozzle, engine shell, Flow rate suction, cooling
AI 理解论文
溯源树
样例
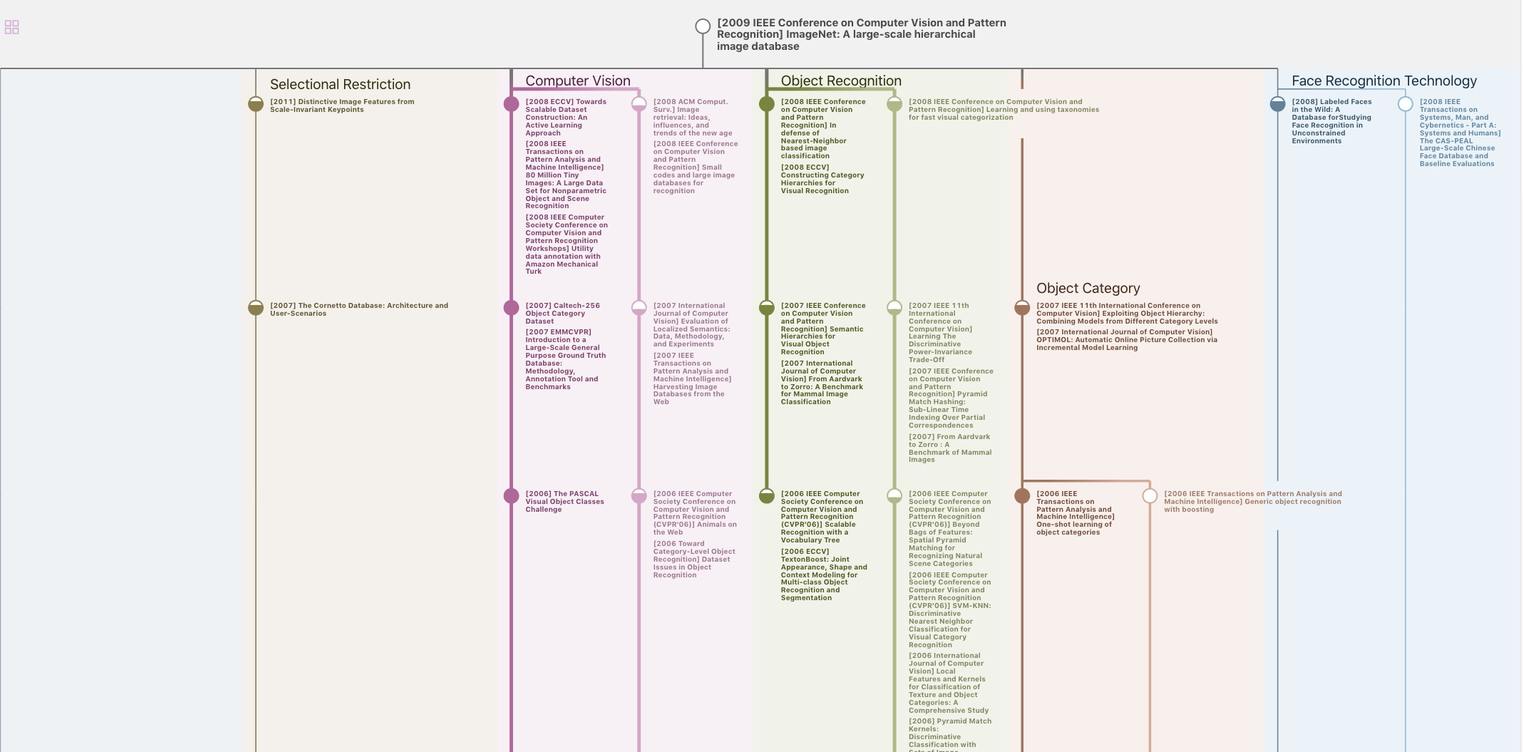
生成溯源树,研究论文发展脉络
Chat Paper
正在生成论文摘要