Structural and Electrochemical Investigation of High Energy Spinel LiMn1.5Ni0.5O4 Produced at Low Temperature
ECS Meeting Abstracts(2021)
摘要
Spinel LiMn1.5Ni0.5O4 (LMNO) materials, without the environmentally toxic Co, are one of the most promising potential cathode materials for lithium ion batteries operated at high voltages. According to the distribution of Mn and Ni within the cubic crystal structure, spinel LMNO can be categorized into either ordered or disordered. Normally, disordered LMNO materials are produced at temperatures which are higher than the theoretical oxygen release temperature of spinel LMNO (715 ℃)[1, 2]. This leads to some Mn4+ atoms being reduced to Mn3+ to maintain the electroneutrality of spinel LMNO. The existence of Mn3+ causes Jahn-Teller distortion and affects the structural stability of spinel LMNO. In order to reduce the amount of Mn3+, high temperature produced LMNO materials are post-annealed at lower temperature, i.e. 700 ℃, to introduce O into spinel LMNO again[3]. Both the high calcination temperatures and the long annealing times increase the preparation cost of the spinel LMNO. In other words, low-temperature calcination without post-annealing would be a preferred way to produce spinel LMNO at lower cost. However, LMNO materials calcinated at 700 ℃ in air show ordered distribution of Mn and Ni, which is supposed to be the reason for poor cycling and rate performance[4, 5]. This indicates changing the ordered distribution of Mn and Ni in 700 ℃ produced LMNO may improve the electrochemical performance. In the present work, different co-precipitation processes are attempted to change the distribution of the Mn and Ni precursors used in the LMNO synthesis. Three different spinel LMNO materials, named as N-, CS- and SW-LMNO, are produced by three hydroxide precursors with stoichiometric Li2CO3 at 700 ℃ without post-annealing. Scanning electron microscope (SEM) images, shown in Figure 1(a) – (c), demonstrate different morphologies of N-, CS- and SW-LMNO. This indicates that different precipitation approaches result in different particle sizes and shapes of spinel LMNO. However, the use of different precipitation processes has little effect on the bulk crystal structure of spinel LMNO, reflected by similar X-ray diffraction (XRD) patterns in Figure 1(d). As shown in Figure 1(e), SW-LMNO shows high initial discharge capacity (140 mAhꞏg-1) at room temperature which is the highest amongst all reported LMNO[6]. SW-LMNO also shows good cycling performance in the first 100 cycles at 1 C (1 C = 150 mAꞏg-1), which are not only better than those of other low-temperature produced spinel LMNO but also comparable with those of most reported high-temperature produced spinel LMNO[7]. This means, this work provides a new strategy to produce high-energy spinel LMNO by controlling the microstructure but save energy consumption. Moreover, transmission electron microscope (TEM), X-ray pair distribution function (PDF) and X-ray absorption spectroscopy (XAS) are performed to explain the reason for improvement of SW-LMNO in comparison with N- and CS-LMNO. Reference [1] A. Manthiram et al. A perspective on the high-voltage LiMn1.5Ni0.5O4 spinel cathode for lithium-ion batteries. Energy & Environmental Science[J]. 2014, 7 (4): 1339-1350 [2] M. Kunduraci et al. Effect of oxygen non-stoichiometry and temperature on cation ordering in LiMn2-xNixO4 (0.50≥ x≥ 0.36) spinels. Journal of Power Sources[J]. 2007, 165 (1): 359-367 [3] D. W. Shin et al. Role of cation ordering and surface segregation in high-voltage spinel LiMn1.5Ni0.5-xMxO4 (M= Cr, Fe, and Ga) cathodes for lithium-ion batteries. Chemistry of Materials[J]. 2012, 24 (19): 3720-3731 [4] Z. Moorhead-Rosenberg et al. Electronic and electrochemical properties of Li1-xMn1.5Ni0.5O4 spinel cathodes as a function of lithium content and cation ordering. Chemistry of Materials[J]. 2015, 27 (20): 6934-6945 [5] B. Aktekin et al. Cation ordering and oxygen release in LiNi0. 5-xMn1.5+xO4-y (LNMO): In situ neutron diffraction and performance in Li ion full cells. ACS Applied Energy Materials[J]. 2019, 2 (5): 3323-3335 [6] O. Tiurin et al. Atomic layer deposition (ALD) of lithium fluoride (LiF) protective film on Li-ion battery LiMn1.5Ni0.5O4 cathode powder material. [J]. 2020, 448: 227373 [7] G. Liang et al. Developing high-voltage spinel LiNi0.5Mn1.5O4 cathodes for high-energy-density lithium-ion batteries: current achievements and future prospects. Journal of Materials Chemistry A[J]. 2020, 8, 15373-15398 Figure 1
更多查看译文
AI 理解论文
溯源树
样例
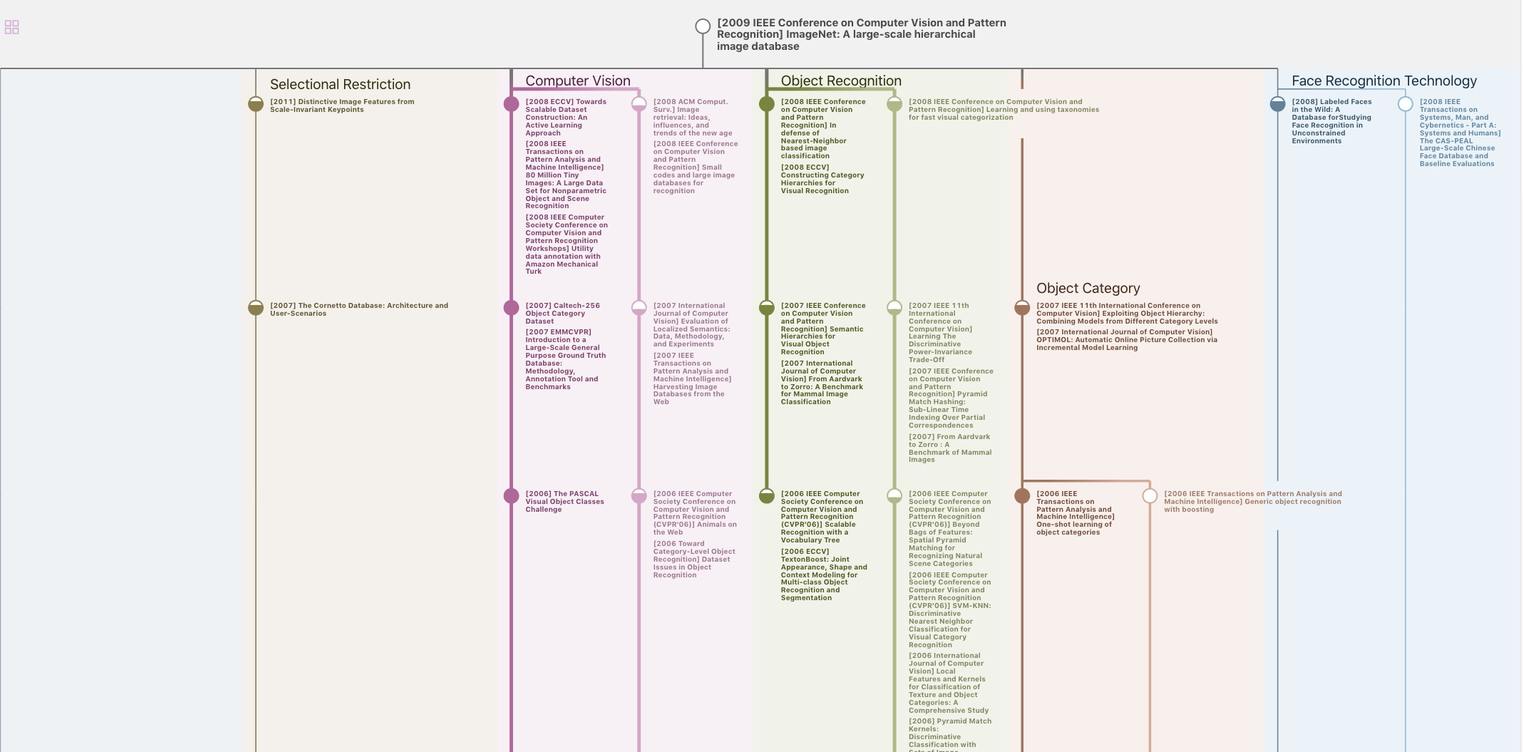
生成溯源树,研究论文发展脉络
Chat Paper
正在生成论文摘要