Numerical Investigation of Various Coaxial Nozzle Designs for Direct Laser Deposition
Volume 2: Manufacturing Processes; Manufacturing Systems; Nano/Micro/Meso Manufacturing; Quality and Reliability(2020)
摘要
Abstract Direct Laser Deposition (DLD) is a form of metal-based additive manufacturing. The DLD process involves ejecting powder out of a nozzle by means of an compressed gas and irradiating a laser beam to heat up the powder and the substrate. During the powder spray ejection, tight focusing of the powder stream has the potential to improve the DLD process by reducing powder wastage. Thus, nozzle design and computational fluid dynamics (CFD) analysis of the design parameters become important. This study focuses on the numerical simulation of the gas-solid flow inside a coaxial DLD nozzle and how design features of the nozzle affect powder focusing. The two-phase gas/powder flow was analyzed using a Eulerian-Lagrangian scheme. A total of twelve designs were simulated and analyzed through CFD simulation, with features such as inlet angle, inlet offset, and the presence and shape of flow-straightening grooves considered. It was determined that geometry reducing particle tangential velocity such as flow-straightening grooves produce the best focusing effects, whereas offset inlets without the presence of grooves reduces focusing by maximizing particle swirling. Finally, the simulations show that the distribution of powders within the nozzle is also affected by nozzle inlet angle, with horizontal inlets providing more even distribution over inlets angled towards the nozzle tip.
更多查看译文
AI 理解论文
溯源树
样例
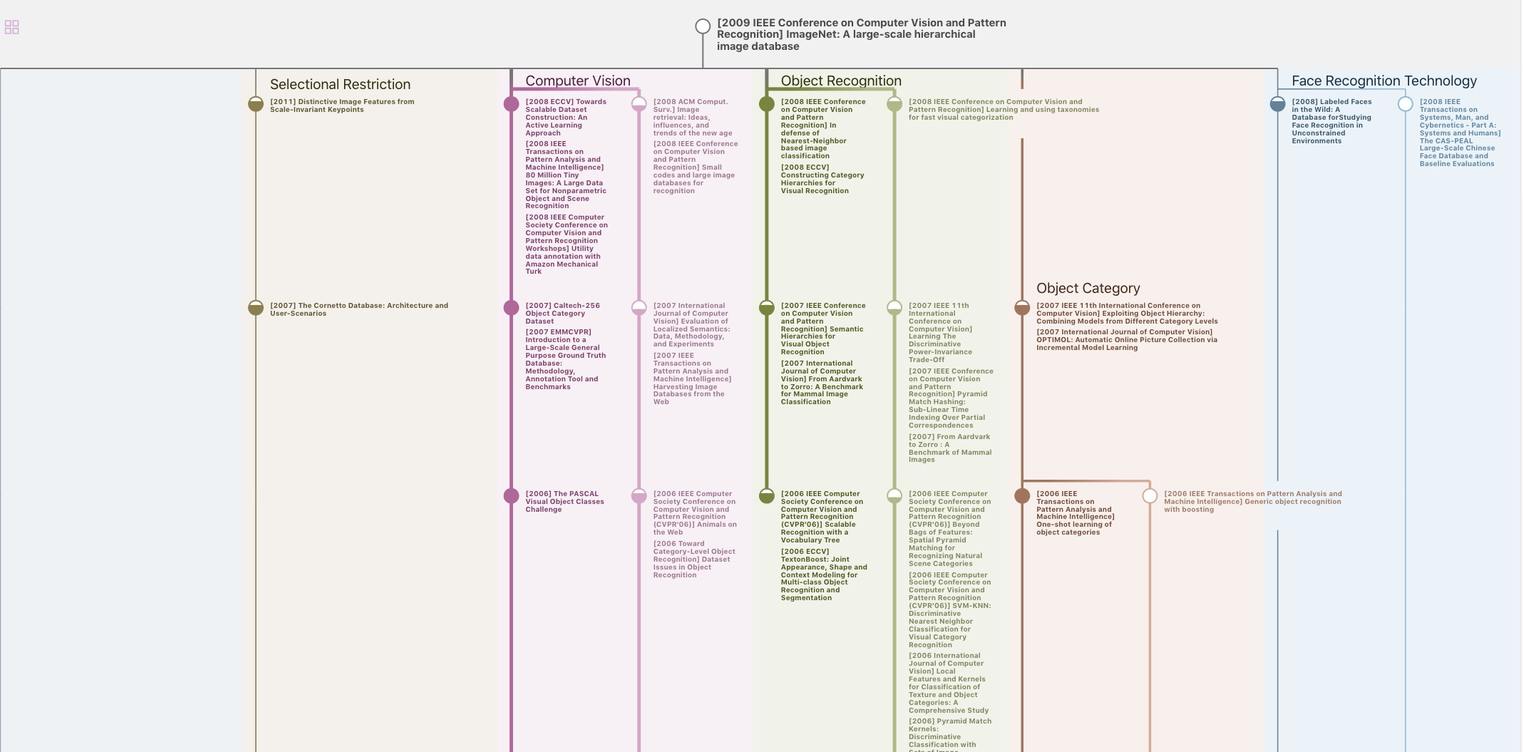
生成溯源树,研究论文发展脉络
Chat Paper
正在生成论文摘要