Designing a Cruciform Specimen Via Topology and Shape Optimisations under Equal Biaxial Tension Using Elastic Simulations.
Materials(2022)
摘要
Stress uniformity within the gauge zone of a cruciform specimen significantly affects materials' in-plane biaxial mechanical properties in material testing. The stress uniformity depends on the load transmission of the cruciform specimen from the fixtures to the gauge zone. Previous studies failed to alter the nature of the load transmission of the geometric features using parametric optimisations. To improve stress uniformity in the gauge zone, we optimised the cross-arms to design a centre-reduced cruciform specimen with topology and shape optimisations. The simulations show that the optimised specimen obtains significantly less stress variation and range in the gauge zone than the optimised specimen under different observed areas, directions, and load ratios of von Mises, S11, S22, and S12. In the quantified gauge zone, a more uniform stress distribution could be generated by optimizing specimen geometry, whose value should be estimated indirectly each time through simulations. We found that topology and shape optimisations could markedly improve stress uniformity in the gauge zone, and stress concentration at the cross-arms intersection. We first optimised the cruciform specimen structure by combining topology and shape optimisations, which provided a cost-effective way to improve stress uniformity in the gauge zone and reduce stress concentration at the cross-arms intersection, helping obtain reliable data to perform large strains in the in-plane biaxial tensile test.
更多查看译文
关键词
cruciform specimen,optimisation,topology,shape,finite element method,biaxial tensile test,material test
AI 理解论文
溯源树
样例
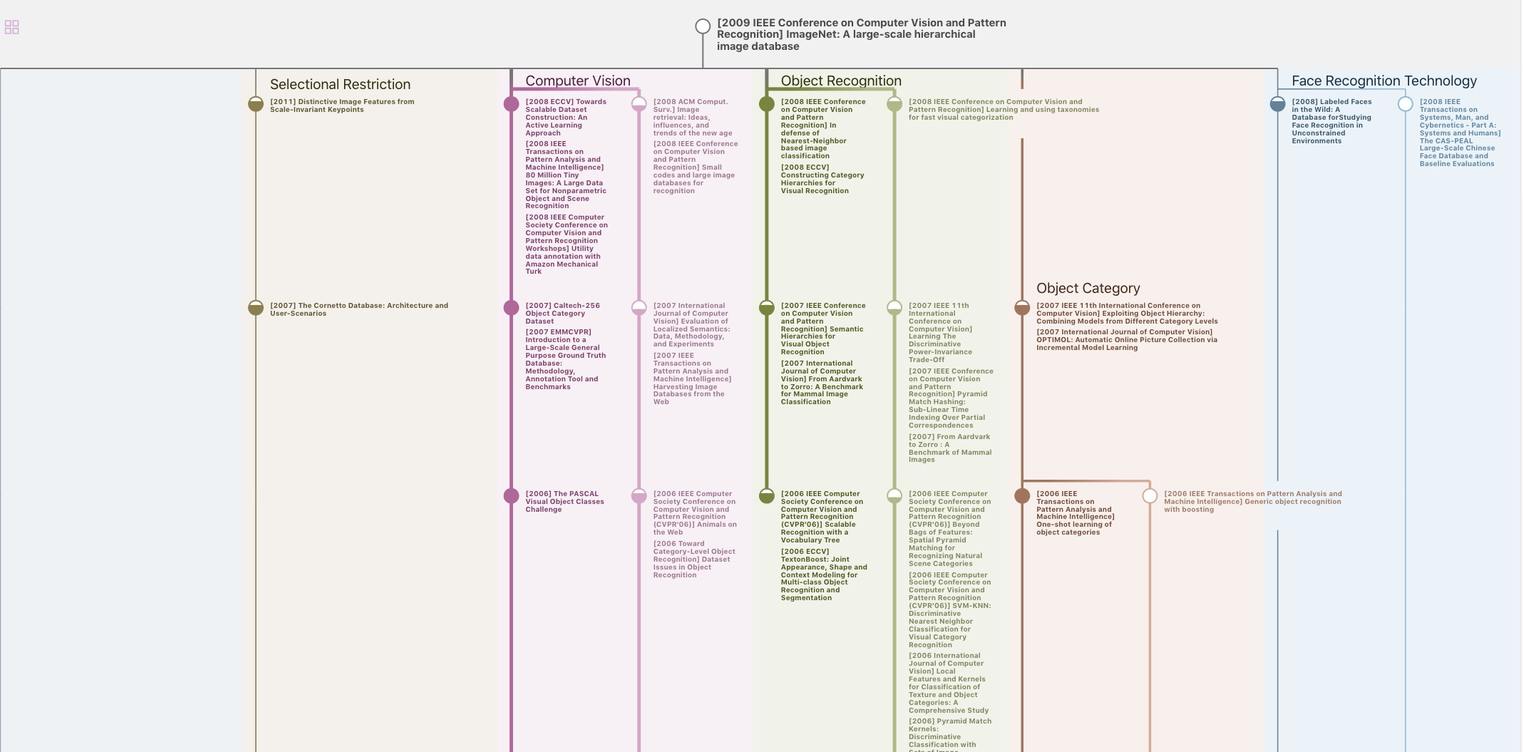
生成溯源树,研究论文发展脉络
Chat Paper
正在生成论文摘要