Physical mechanisms for delaying condensation freezing on grooved and sintered wicking surfaces
Applied Physics Letters(2022)
摘要
Heat pipes are passive heat transfer devices crucial for systems on spacecraft; however, they can freeze when exposed to extreme cold temperatures. The research on freezing mechanisms on wicked surfaces, such as those found in heat pipes, is limited. Surface characteristics, including surface topography, have been found to impact freezing. This work investigates freezing mechanisms on wicks during condensation freezing. Experiments were conducted in an environmental chamber at 22 °C and 60% relative humidity on three types of surfaces (i.e., plain copper, sintered heat pipe wicks, and grooved heat pipe wicks). The plain copper surface tended to freeze via ice bridging—consistent with other literature—before the grooved and sintered wicks at an average freezing time of 4.6 min with an average droplet diameter of 141.9 ± 58.1 μm at freezing. The grooved surface also froze via ice bridging but required, on average, almost double the length of time the plain copper surface took to freeze, 8.3 min with an average droplet diameter of 60.5 ± 27.9 μm at freezing. Bridges could not form between grooves, so initial freezing for each groove was stochastic. The sintered wick's surface could not propagate solely by ice bridging due to its topography, but also employed stochastic freezing and cascade freezing, which prompted more varied freezing times and an average of 10.9 min with an average droplet diameter of 97.4 ± 32.9 μm at freezing. The topography of the wicked surfaces influenced the location of droplet nucleation and, therefore, the ability for the droplet-to-droplet interaction during the freezing process.
更多查看译文
AI 理解论文
溯源树
样例
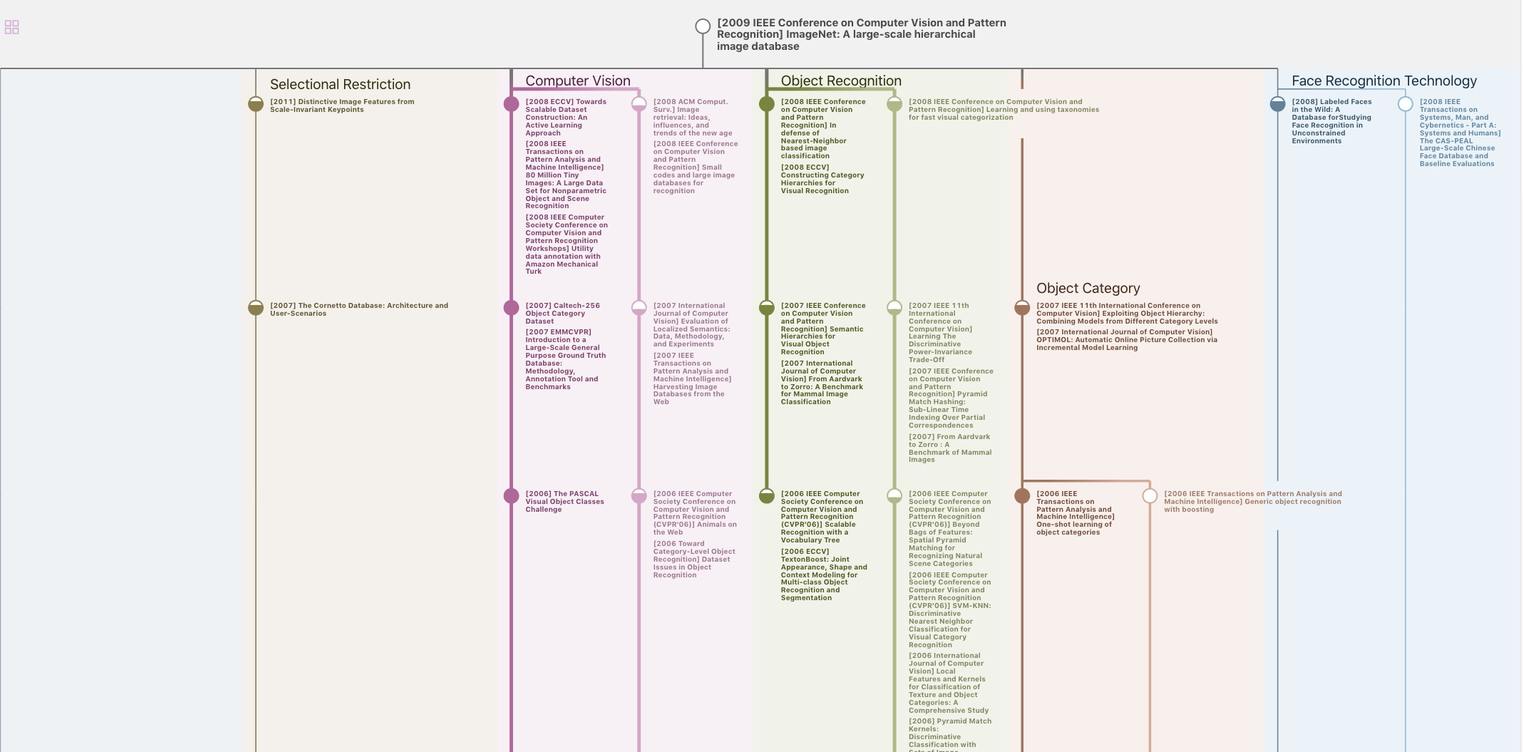
生成溯源树,研究论文发展脉络
Chat Paper
正在生成论文摘要