Structural optimization of an aeroelastic wind tunnel model for unsteady transonic testing
CEAS Aeronautical Journal(2022)
摘要
The reduction of loads, ultimately leading to a weight reduction and thus an increase in aircraft performance, plays an important role in the design of modern aircraft. To this end, two aeroelastic tailoring methodologies, independently developed at ONERA and DLR and aiming at load reduction by means of a sophisticated application of composite materials, were applied to a common model geometry. A choice was made in favor of the publicly available NASA Common Research Model (CRM) wing, featuring a comprehensive database with respect to geometry, as well as analytical and experimental research results. The span of the wing half to be investigated was set to 0.55 m, limited by the test section dimensions. While wind tunnel testing was part of ONERA’s workshare, the model building was performed by DLR. This paper at hand focuses on the structural, aeroelastic optimization of the DLR wing. It is based on an optimization framework developed and constantly being enhanced and extended at the DLR - Institute of Aeroelasticity (DLR-AE). The paper describes the consideration of different structural objective functions, structural and aeroelastic constraint combinations, design field considerations, as well as the application of an aero load correction applied in the course of the optimization. The final results consist of the selection of an appropriate fiber type, optimized fiber layers represented as stacking sequence tables for the upper and lower wing skins, and the corresponding optimized jig twist distribution, required for manufacturing the lamination molds; in summary, all data required to start the construction of the wind tunnel model.
更多查看译文
关键词
Composite optimization,Aeroelasticity,Passive load alleviation
AI 理解论文
溯源树
样例
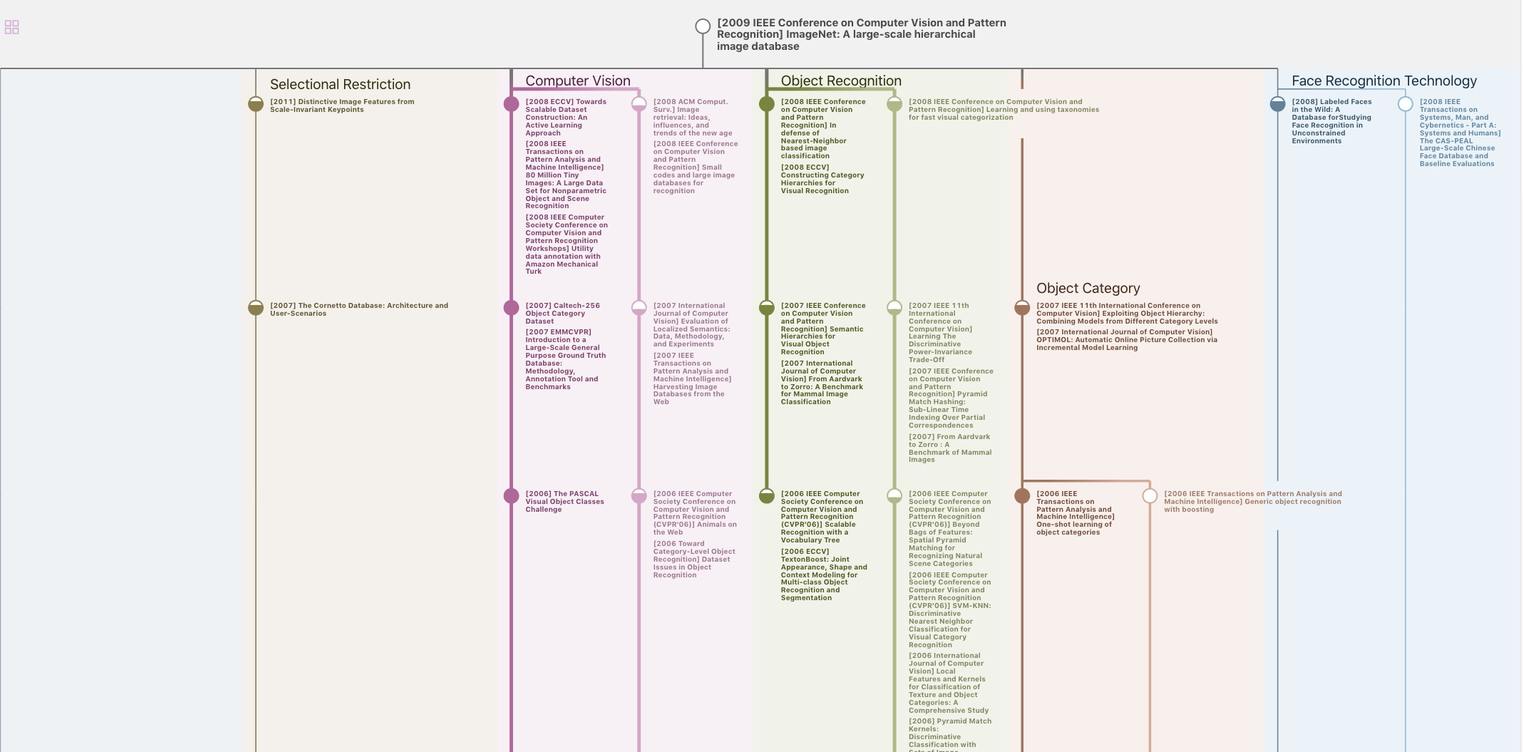
生成溯源树,研究论文发展脉络
Chat Paper
正在生成论文摘要