Process Optimization and Interfacial Microstructure and Properties Analysis of Laser Cladded IN718 Alloy
CHINESE JOURNAL OF LASERS-ZHONGGUO JIGUANG(2022)
摘要
Objective The IN718 alloy is a kind of nickel-based superalloy with excellent corrosion resistance and mechanical properties, which has been widely used in aerospace, chemical and petroleum fields. However, due to its harsh service environment, IN718 alloy parts usually fail due to wear, corrosion and fatigue cracking, resulting in serious economic losses. The emergence of laser cladding technology can not only efficiently restore the size of failed parts, but also obtain controllable microstructure and properties on its surface, which greatly reduces the economic loss of enterprises. The interfacial area between the cladded layer and substrate usually is the weakest area of remanufactured parts. This is because the interface of cladded layer experiences multiple reciprocating processes of rapid heating and rapid cooling which is easy to cause complex metallurgical reaction and phase transformation. It can not only promote the metallurgical combination between the cladded layer and substrate, but also produce a heat affected zone, resulting in performance degradation. At the same time, the poor component matching between powder and substrate and the insufficient laser energy input are easy to lead to a series of defects such as inclusions and pores near the repaired interface. The microstructure and properties of this area are very important to the service life of repaired IN718 alloy parts, but there is few research on the repaired interfacial characteristics and properties of laser cladded IN718 alloy. Therefore, it is of great significance to study the microstructure evolution and properties of the interface of IN718 laser cladded layer. Methods The aged-IN718 alloy plate and IN718 spherical powder are used in this study. First, the laser cladding process of IN718 alloy is optimized based on the orthogonal experimental design and the effect of process parameters on the forming size of cladded layer is studied. Then, the interfacial microstructure characteristics are observed by an optical microscope (OM) and scanning electron microscope (SEM ), and the elemental content of precipitates is detected by an energy disperse spectroscopy (EDS ). The micro-hardness near the interface between cladded layer and substrate is tested by a hardness tester. The bonding strength of cladded layer/substrate interface is quantitatively analyzed by the shear test, and the fracture behavior of cladded layer interface is also analyzed. Results and Discussions The width (W ), height (H) and W/H of the cladded layer increase with the increase of the laser power, while the dilution ratio of the cladded layer increases first and then decreases with the increase of the laser power [Figs. 3(a1)--(a4 ) ]. The scanning speed has a negative effect on the width and height of the cladded layer, while it has a positive effect on the W/H and dilution ratio [Figs. 3 ( b1)--(b4 ) ]. The increase of powder feeding rate is helpful to improve the height of the cladded layer, but it is not conducive to the improvement of width, W/H and dilution ratio [ Figs. 3(c1)--(c4 ) ]. The optimized laser cladding process parameters of aged-IN718 alloy are as follows: the laser power of 900 W, the scanning speed of 6 mm/s, and the powder feeding rate of 10 g/min. From top to bottom, the interface includes cladded layer (CL ), fusion zone (FZ ), heat affected zone (HAZ) and substrate which is not affected by heat [ Fig. 4(a ) ]. The microstructure of the cladded layer is dendritic crystal with directional epitaxial growth, the fusion zone is located between the cladding zone and the substrate [Fig. 4 (b ) ]. The upper side is connected with the cladded layer and presents obvious crystallization characteristics, and the other side is connected with the substrate and presents element diffusion characteristics [Fig. 4(c ) ]. The heat affected zone is located below the fusion zone, where the grains grow unevenly and are obviously different from the grains in the original substrate [Fig. 4 (d ) ]. This is because the energy input leads to the partial dissolution of precipitates in this region and diffusion into austenite. However, due to the short action time at high temperature, only the precipitates with smaller size are completely dissolved, while the carbides with larger size are not fully dissolved and continue to remain at the grain boundary [Fig. 4(e ) ]. The element distribution from the cladded layer to the substrate is relatively uniform, and there is no macro-segregation (Fig. 5). This is because the cladding layer and substrate are similar in composition and there is no obvious chemical element transition between them. In addition, there is no plane crystal at the interface between the cladded layer and the substrate. This is because the powder composition is similar to the substrate composition and both have a face centered cubic (FCC) crystal structure ( Fig. 6 ). The micro-hardness of the IN718 cladded layer is about 280 HV. The micro-hardness of the substrate is about 475 HV. The micro-hardness of the heat affected zone gradually increases from the cladded layer to the substrate ( Fig. 7 ). The average interfacial shear strength of the laser cladded IN718 alloy is 608.87 MPa (Fig. 8 ). The shear fracture at the interface of the laser cladded IN718 alloy basically includes three parts: fiber region, radiation region and shear lip region (Fig. 9 ). Conclusions Laser cladding process parameters have a significant impact on the IN718 alloy coating. Increasing power and reducing scanning speed are helpful to improve the width and height of the cladded layer. Increasing the powder feeding rate and reducing the scanning speed are helpful to improve the height of the cladded layer, but not conducive to improving the width, dilution ratio and W/H. The interface of IN718 cladded layer is surrounded by the cladded layer zone, fusion zone, heat affected zone and substrate from top to bottom. The cladded layer presents typical dendrite morphology. The fusion zone shows metallurgical bonding with the substrate, which is different from the cladding layer and substrate in morphology, and there is no plane crystal. The heat affected zone is located below the fusion zone, and the internal grains are coarsened. The element distributions at the interface are uniform and there is no macro -segregation, but the residual Laves phase will lead to the mutation of Nb or Mo element in the cladded layer and the fusion zone. The micro-hardness of the cladded layer is lower than that of the aged substrate, while the micro-hardness of the heat affected zone increases gradually from the cladded layer to the substrate. The average shear strength of IN718 coating interface is 608.87 MPa. Subsequent heat treatment is needed to improve the micro-hardness and shear strength near the interface.
更多查看译文
关键词
laser technique,laser cladding,IN718,process optimization,interface microstructure,mechanical property
AI 理解论文
溯源树
样例
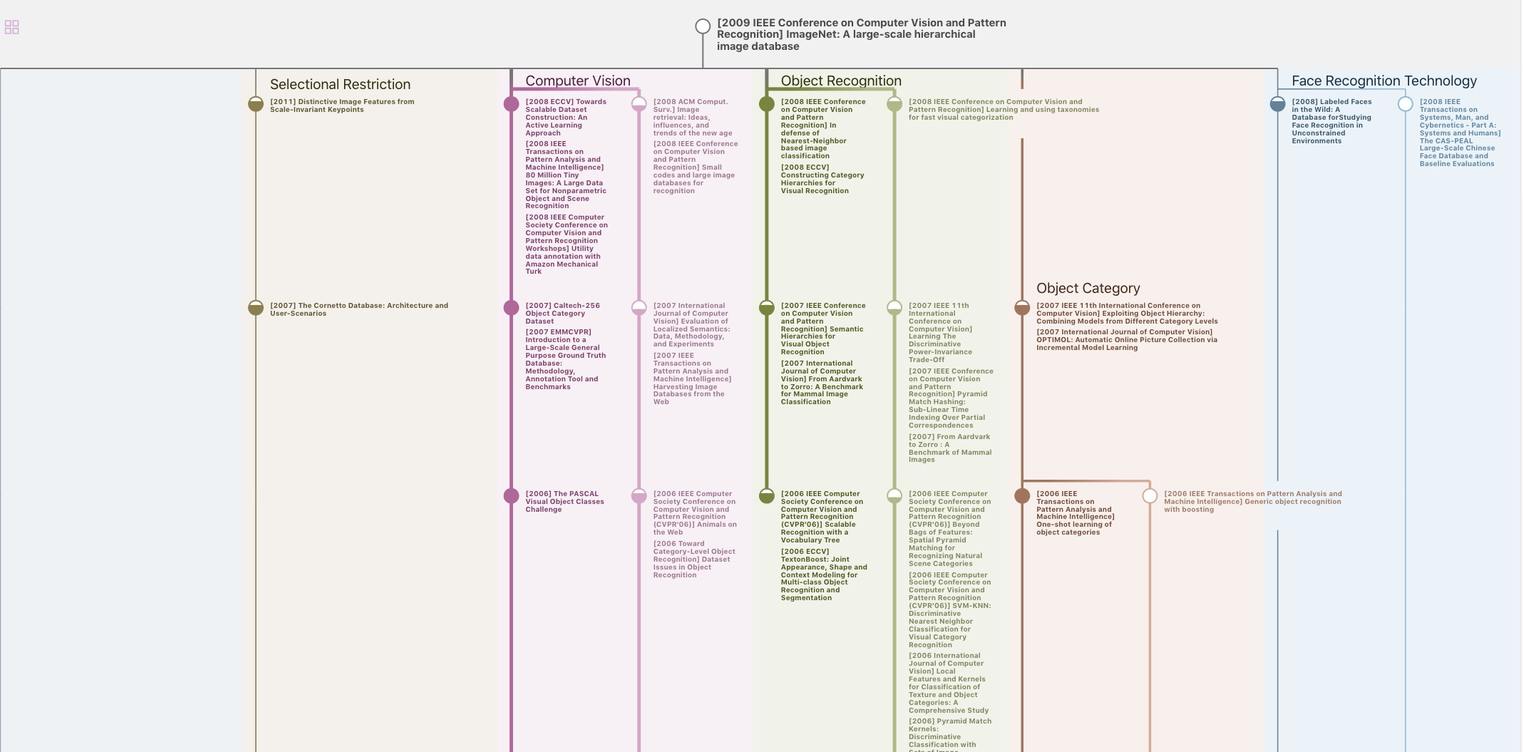
生成溯源树,研究论文发展脉络
Chat Paper
正在生成论文摘要