Simulation and experimental research on residual stress of honed gear based on scratch test
The International Journal of Advanced Manufacturing Technology(2022)
摘要
The residual compressive stress on the surface of the gear after the power honing process could significantly improve the service performance and life of the gear. In order to study the formation mechanism and special distribution of the residual stress, a spiral scratching experiment is designed for the gear steel samples. Meanwhile, the influence of preload force and groove spacing on the residual stress is studied. The result shows that the residual stress increases from − 252 MPa to − 344 MPa in the parallel feed direction and from − 317 MPa to − 541 MPa in the vertical direction as the spacing decreases. With the increase of preload force, the residual stress value decreases when the spacing is small and increases when the spacing is large. Then, the three-dimensional finite element model of double abrasive grains is established with ABAQUS. The residual stress value of the whole surface is distilled and compared with the experimental one. According to the experimental and simulation results, the residual compressive stress of power honing is mainly caused by plastic deformation and the reason for its special distribution is that a smaller scratch spacing is generated in the area of the pitch line of tooth surface.
更多查看译文
关键词
Power honing,FEM,Residual stress,Scratching
AI 理解论文
溯源树
样例
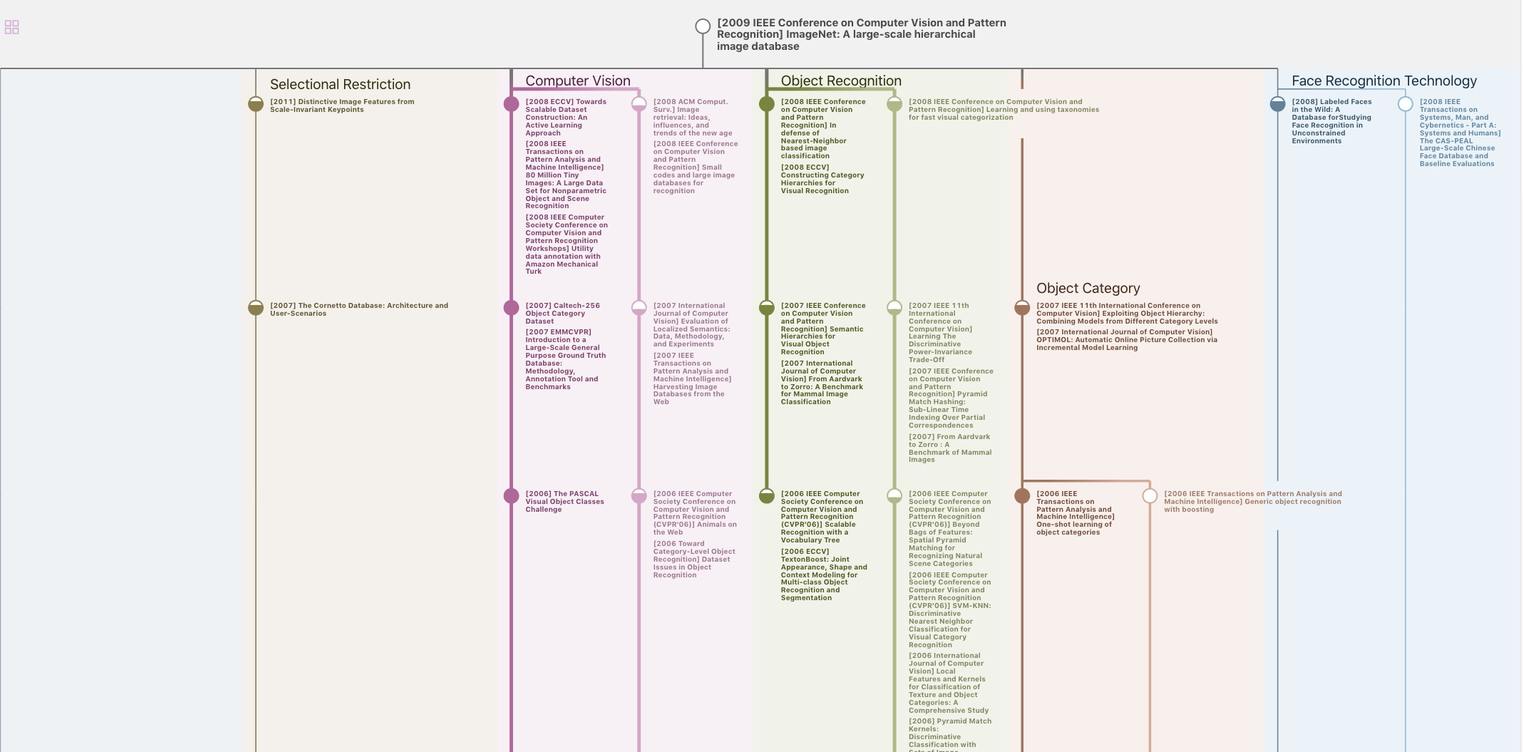
生成溯源树,研究论文发展脉络
Chat Paper
正在生成论文摘要