Improving the machining performance in single-point diamond turning of curved Zerodur optics by using straight-nosed cutting tools
Journal of Materials Processing Technology(2022)
摘要
The machining performance and mechanisms of straight-nosed cutting tools in the single-point diamond turning (SPDT) of curved Zerodur optics are analysed and experimentally investigated. Analyses into the SPDT processes of convex spherical Zerodur samples have shown that using straight-nosed cutting tools can significantly reduce the cut thickness for facilitating the ductile-mode material removal while increasing the width of cut compared with the conventional round-nosed cutting tools. Calculations have also shown that lower cutting force intensities would be acting on the straight cutting edges than the round ones, which can in turn contribute to decreasing the heat flux density into the cutting tool, and is thus expected to reduce the thermal-induced cutting tool wear. To verify these, SPDT tests of spherical Zerodur samples were carried out, where a reduction of the machined surface roughness from Ra 173 nm to 15 nm was achieved by using the straight-nosed cutting tools, and a 96% area ratio of ductile-mode cutting was obtainable with very slight damage marks left on the machined surface. It has been further found that the straight-nosed cutting tools suffered less flank wear, as well as less bluntness and recession of the cutting edge. The mean cutting and thrust forces acting on per unit length of the cutting edge were found to be reduced, which agrees well with the prior analytical results, and is believed as evidence for the reduction of cutting power required for each unit cutting edge area for enhancing the resistance to cutting tool wear.
更多查看译文
关键词
Ultra-precision machining,Single-point diamond turning,Straight-nosed cutting tools,Ductile-mode cutting,Machining performance,Cutting tool wear
AI 理解论文
溯源树
样例
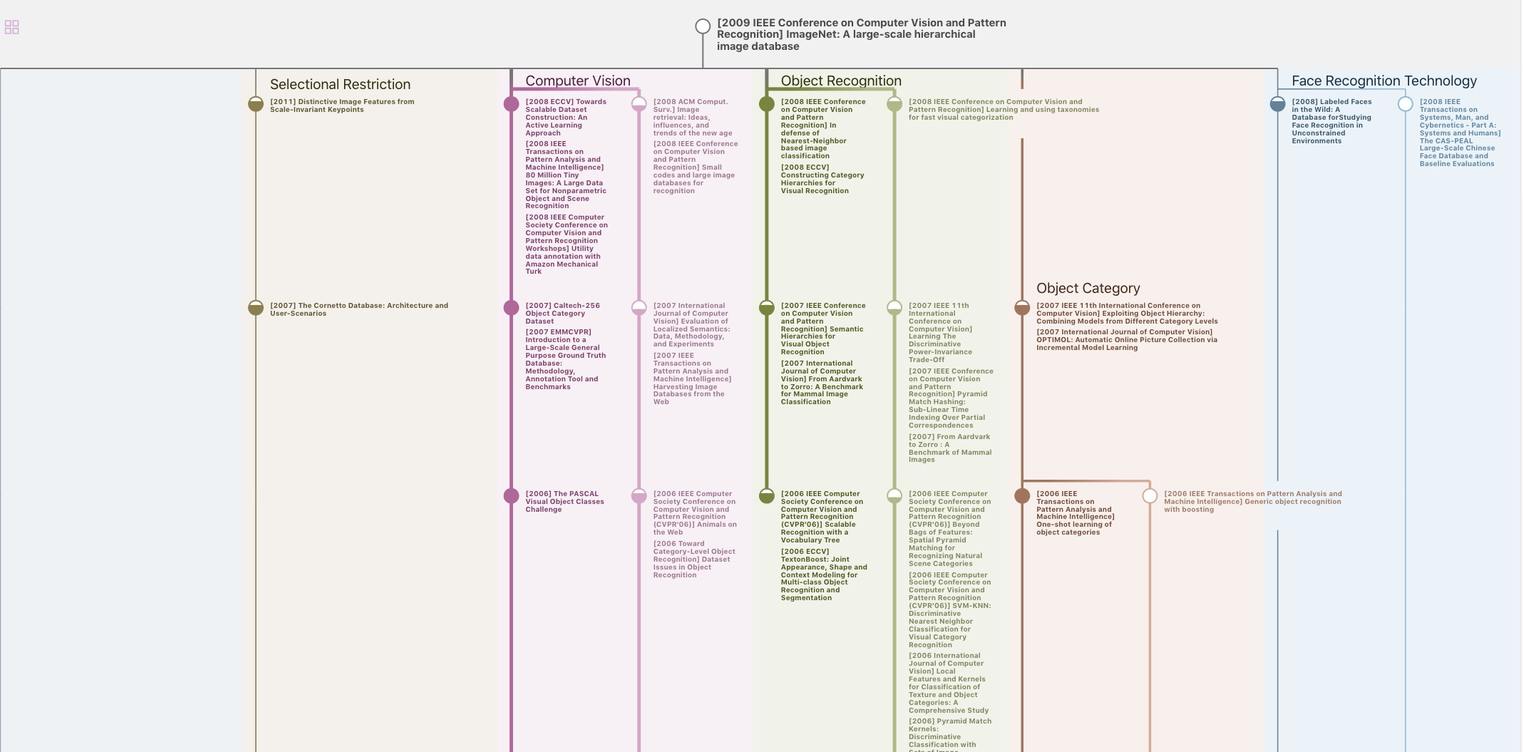
生成溯源树,研究论文发展脉络
Chat Paper
正在生成论文摘要