The impact of infill percentage and layer height in small-scale material extrusion on porosity and tensile properties
Additive Manufacturing(2022)
摘要
Material extrusion additive manufacturing is prone to introducing porosity within the structure due to the layer-by-layer construction using elliptical beads of material. This open porosity ultimately plays a role in determining the mechanical properties of printed parts. The shape, size, and amount of porosity within a printed part is influenced by a variety of factors, including nozzle diameter, infill percentage, layer height, raster orientation, and print speed. While several studies have investigated these and other parameters’ effects on mechanical performance and porosity, better understanding the interconnected relationships is crucial in balancing the various input parameters to achieve maximum strength. This work initially examined the influence of key print parameters (infill percentage and layer height) on the internal porosity of a printed Acrylonitrile Butadiene Styrene (ABS) part. Then, the print parameters and internal porosity were statistically correlated to final mechanical properties. Porosity was further classified as either open or closed to differentiate between connected voids in the mesostructure from isolated voids within the material itself. Mechanical performance increased with an increasing density and infill percentage, displaying a 224 % increase in elastic modulus and a 150 % increase in ultimate tensile strength. The contribution of layer height was found to be conditional upon the infill percentage.
更多查看译文
关键词
3D Printing,Extrusion,Porosity,Mechanical Properties,Fused Filament Fabrication
AI 理解论文
溯源树
样例
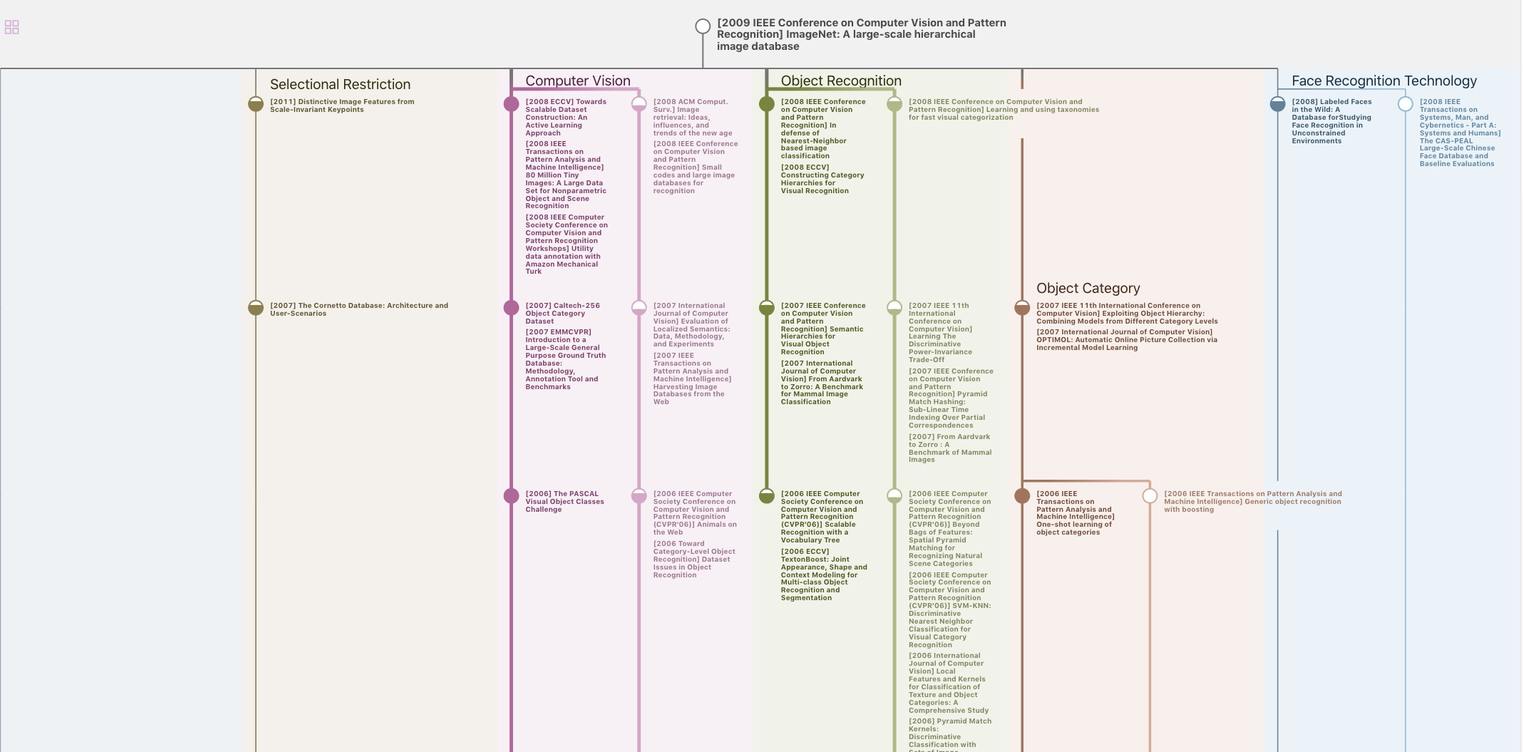
生成溯源树,研究论文发展脉络
Chat Paper
正在生成论文摘要