Realizing quality inspection in magnetic pulse crimping manufacturing: Using Steger algorithm and self-attention
Journal of Materials Processing Technology(2023)
摘要
Magnetic pulse crimping (MPC) is a high-speed forming using magnetic force to derive metal deformation, which has advantages of controllability and excellent formability. However, due to similar joint appearance and unobservable connection area, evaluating joint quality nondestructively is difficult. This paper presents a quality inspection using the similarity between typical joints (templates) and tests to solve the difficulty. Templates corresponded to joints with deformations ranging from insufficient to excessive (categories 0–4), and the intermediate was qualified. Deformed shapes of the joints on coaxial sections were analytical features to make the most of the correlation between shape and quality. Detailed analysis on quality-related shape avoids unobservable areas and explores subtle differences. Shapes were extracted from the structure light image using the Steger-based algorithm. Self-attention network, a machine learning algorithm, learned the shapes of typical joints to form a comparator. The comparator was used to determine which template shape (types 0–4) the different shapes of the test joint were similar to. The test joint category depended on which type has the maximum ratio in shape prediction. Steger extracts shapes without the discrete spots effect, abnormal and missing values. The comparator accuracy is 0.9701, 0.9841 and 0.9881 for training, validation, and testing. The F1 of the qualified category is 0.98. The untrained joints were used as validation. The maximum ratios are 0.878, 0.842, 0.764, 0.469, and 0.997, whose predicted categories coincide with the real ones. This proves that it is feasible to design inspection based on process characteristics.
更多查看译文
关键词
Magnetic pulse crimping,Quality inspection,Feature similarity,Steger-based algorithm,Self-attention,Machine learning
AI 理解论文
溯源树
样例
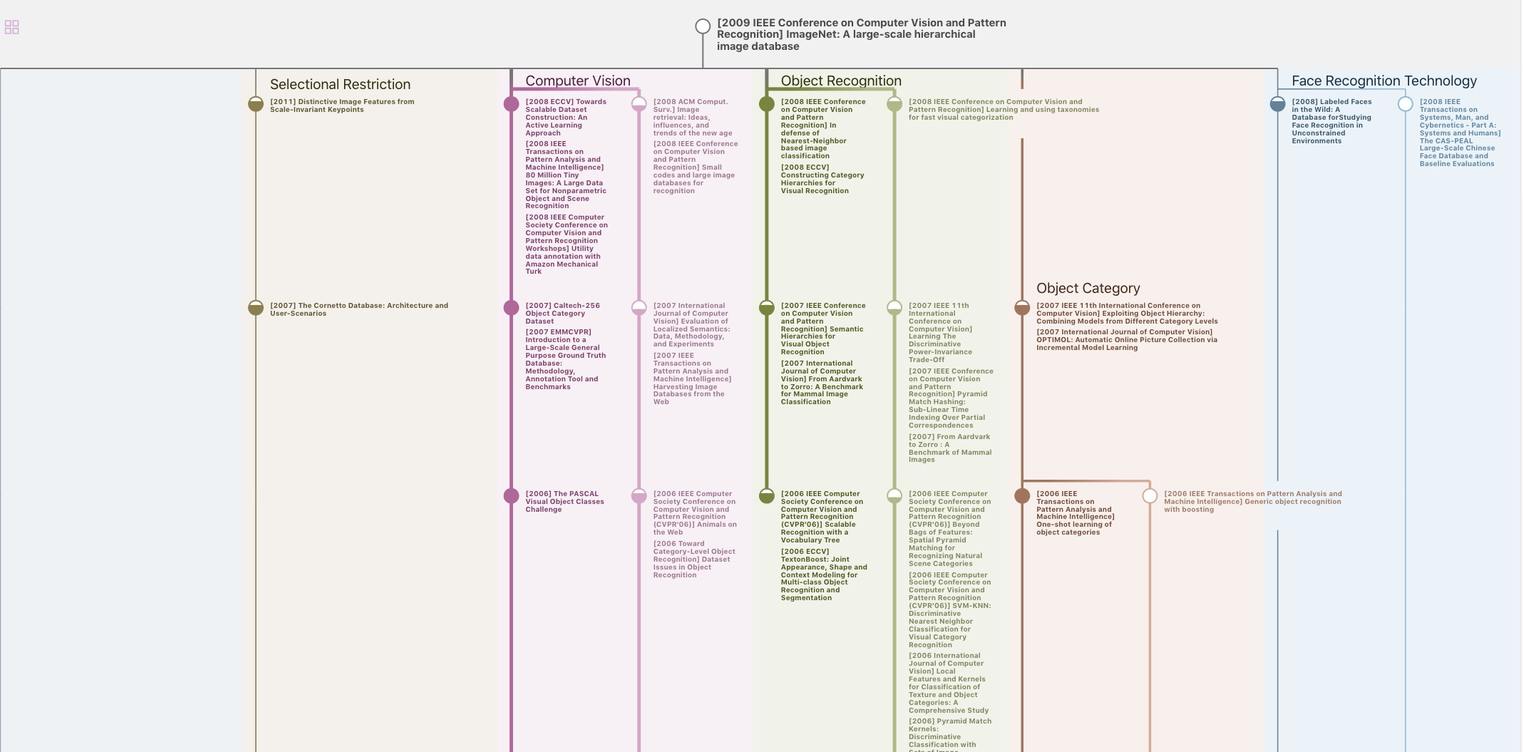
生成溯源树,研究论文发展脉络
Chat Paper
正在生成论文摘要