Experimental validation of non‐Newtonian stratified co‐extrusion prediction models using a digital process twin
Polymer Engineering & Science(2022)
摘要
Abstract In the co‐extrusion of plastics, pressure‐throughput behavior, layer distribution, and residence time are crucial parameters, modeling of which contributes to manufacturing high‐quality products at optimized process efficiency and significantly shortens development times for die systems. In previous work, we have presented symbolic regression models to predicting the (i) pressure‐throughput behavior, (ii) position of the interface, (iii) interfacial shear stress, (iv) ratio of volume flow rates, and (v) interfacial flow velocity for isothermal two‐layer co‐extrusion flows through rectangular ducts. These regression models are mathematically simple and capable of capturing the shear‐thinning nature of polymer melts without the need for numerical methods. Here, we present an experimental study validating the proposed models against co‐extrusion process data and comparing them to existing theories. To this end, a two‐layer co‐extrusion demonstration die instrumented with an optical coherence tomography sensor for detecting the interfacial position was used. To accurately set up and evaluate the die flows, the overall co‐extrusion process was represented by means of a digital process twin. Industrially relevant combinations of materials were tested under a wide range of processing conditions. Comparisons of pressure losses and interfacial positions to the predictions showed excellent agreement and the results outperformed the concept of representative viscosity.
更多查看译文
关键词
digital process twin,experimental validation,<scp>non‐newtonian</scp>
AI 理解论文
溯源树
样例
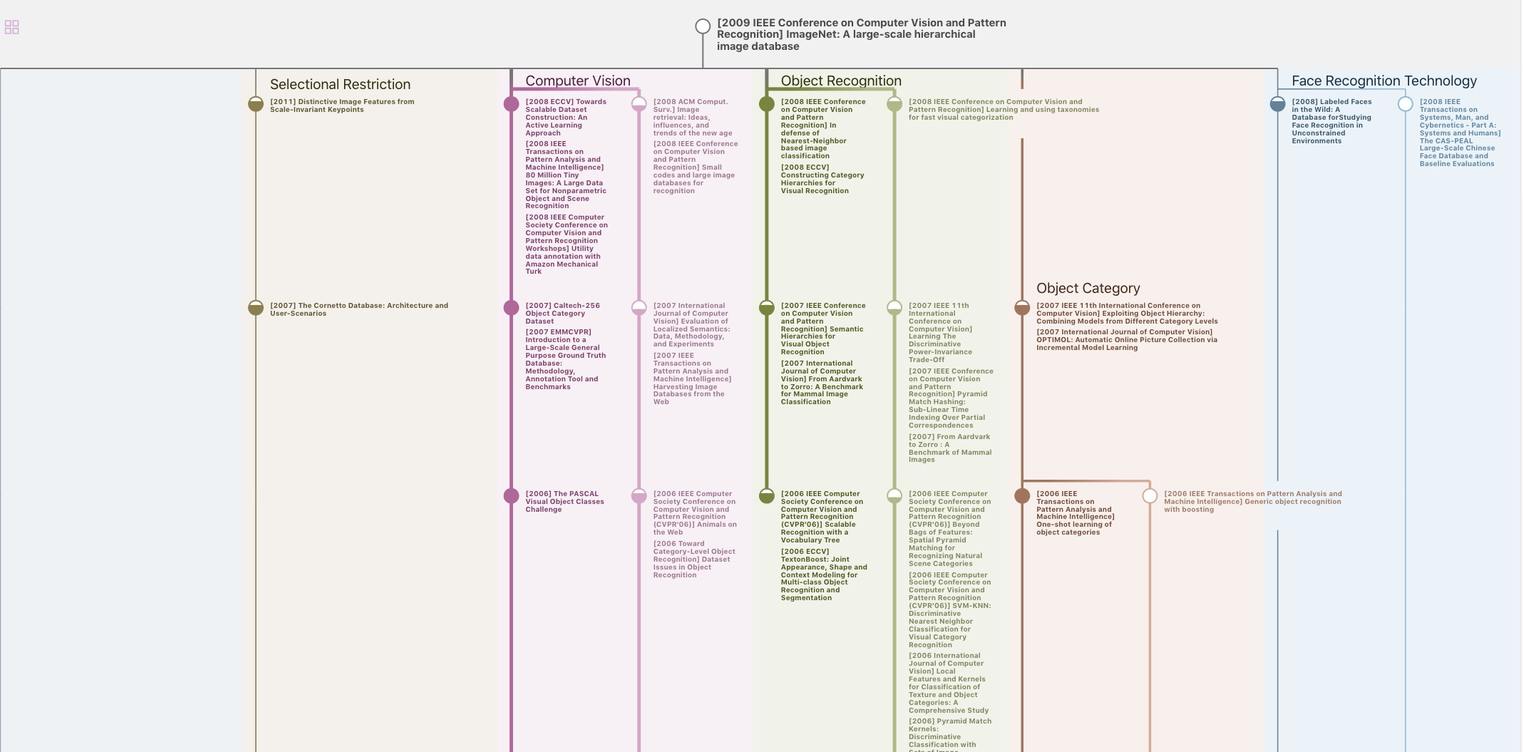
生成溯源树,研究论文发展脉络
Chat Paper
正在生成论文摘要