Active Stirling Thermocompressor: Modelling and effects of controlled displacer motion profile on work output
Applied Energy(2022)
摘要
Recent work suggests that Stirling device performance can be improved using a decoupled, actively controlled displacer piston to directly shape the device's thermodynamic behavior. In this paper, the authors validate the controlled displacer concept using a low-frequency thermocompressor platform whose displacer and power output mechanisms are not kinematically coupled. As a little-known class of Stirling devices whose work output is pneumatic rather than mechanical, the thermocompressor presents new challenges for modeling and experi-mental validation because few devices have actually been built and tested. The device presented here is currently the highest pressure experimental research platform of a Stirling thermocompressor known to the authors. A third-order dynamic model is derived using first principles and is validated against experimental results. The model contains parameters that are known and/or measurable and as such is not a "fitted" model. This first -principles model is used to explore the influence of different displacer motion profiles on the output of the thermocompressor. The model is able to incorporate an arbitrarily-specifiable displacer motion profile. Using a controlled displacer piston profile, we experimentally demonstrate 1.45X higher peak cycle power and 3.6X higher work output, compared to a traditional sinusoidal displacer motion. This model is appropriate for opti-mizing the control of the displacer motion with respect to desired thermocompressor power, efficiency, or other performance metrics for any general Stirling thermocompressor.
更多查看译文
关键词
Stirling Thermocompressor,Displacer piston control,thermocompressor,active Stirling,controlled Stirling,first -principles model,lumped -parameter model
AI 理解论文
溯源树
样例
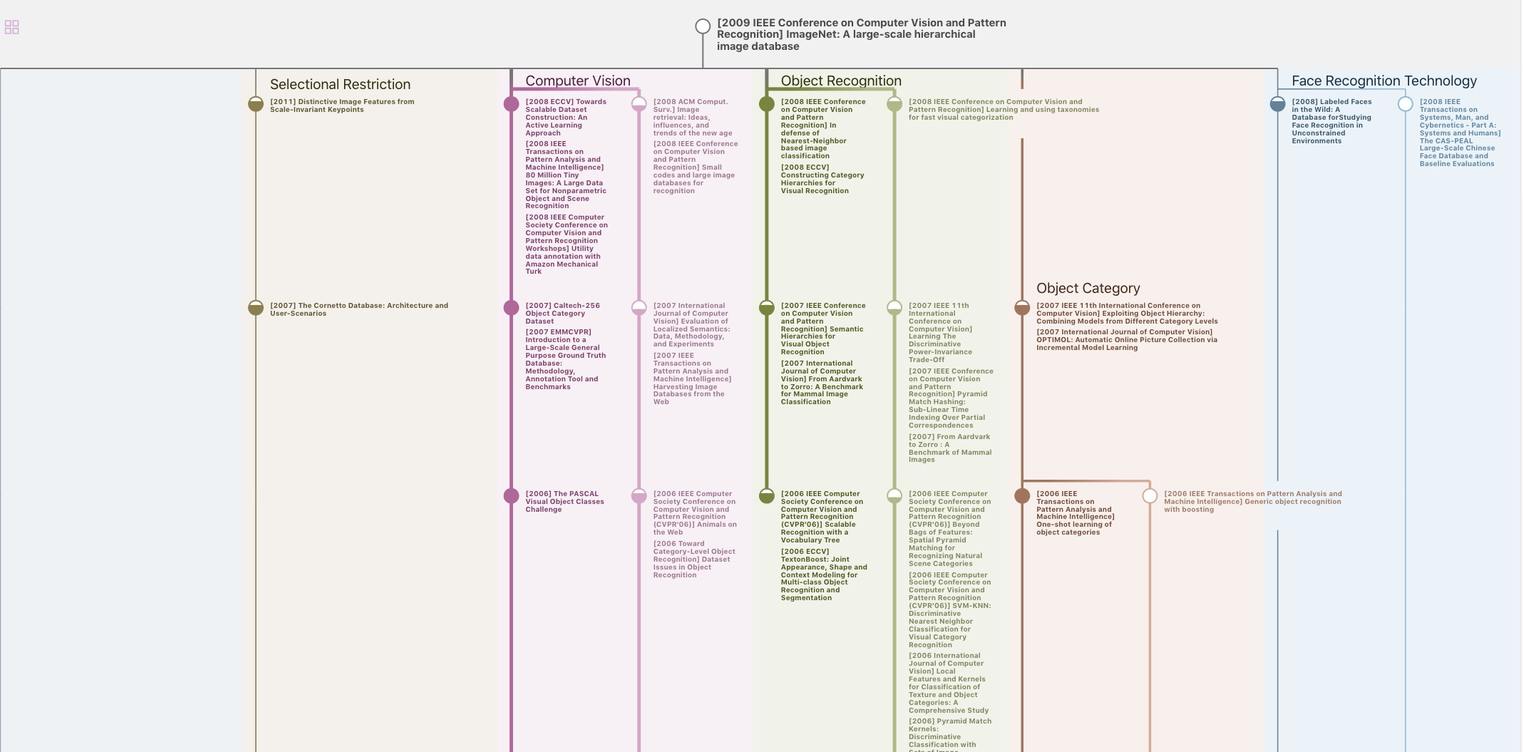
生成溯源树,研究论文发展脉络
Chat Paper
正在生成论文摘要