Simulation of Annealing Process on AISI 316 L Stainless Steel Fabricated Via Laser Powder Bed Fusion Using Finite Element Method With Creep
Additive Manufacturing(2022)
摘要
In the laser powder bed fusion (L-PBF) process, the development of residual stress in as-built components is unavoidable owing to the concentrated heat input and rapid solidification. Thus, the manufacturing of precise components using L-PBF is challenging because of the deformation of the finished products caused by residual stresses. Annealing heat treatment after L-PBF can effectively reduce the residual stress; however, it also reduces the hardness and yield strength of the products. In this study, the deformations of AISI 316 L components fabricated via L-PBF with and without annealing heat treatments were investigated in terms of residual stresses caused by the L-PBF process. In addition, a finite element model was developed for predicting the deformations as well as the evolution of the residual stresses during the annealing process. Cantilever-type residual stress experiments were designed and conducted to quantitatively analyze the evolution of the residual stresses during annealing heat treatments under different conditions. The annealing behavior of 316 L was modeled using the creep material properties. The developed simulation model was further validated using two specially designed components, an auxetic cantilever and a propeller made of 316 L using L-PBF. The developed model could accurately represent the deformations of 316 L components fabricated via L-PBF. In comparison to the de-formations measured in the experiments, those estimated by the model showed average error values of only 0.21 and 0.19 mm for the auxetic cantilever and propeller, respectively.
更多查看译文
关键词
Laser powder bed fusion,Annealing,Finite element analysis,Residual stresses
AI 理解论文
溯源树
样例
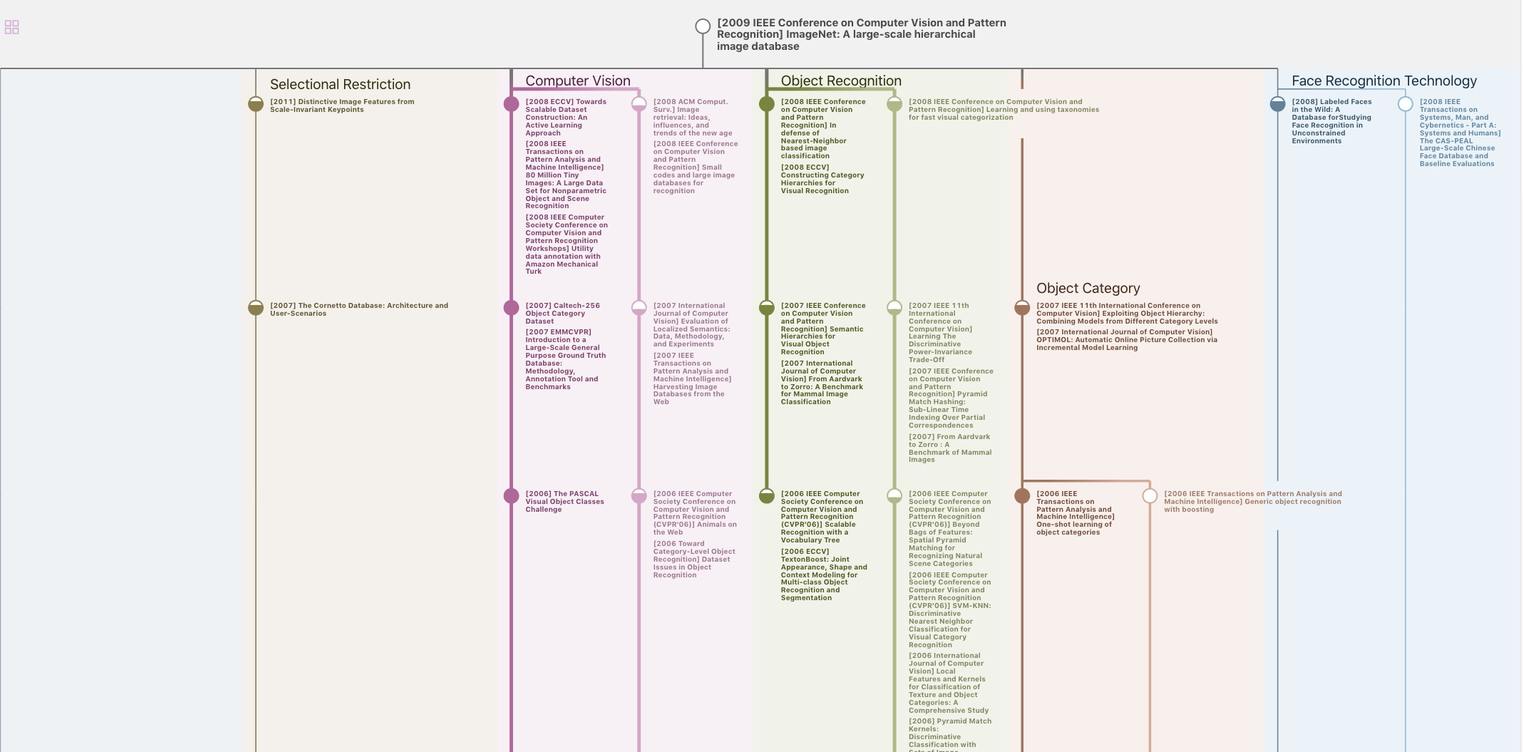
生成溯源树,研究论文发展脉络
Chat Paper
正在生成论文摘要