Multi-Fidelity Simulation for Secondary Air System Seal Design in Aero Engines
Volume 10C: Turbomachinery — Design Methods and CFD Modeling for Turbomachinery; Ducts, Noise, and Component Interactions(2022)
摘要
Abstract Secondary air system seals in aero engines sit at the intersection between all the major aspects of the physics of the system. Their behavior is affected by the air system, the thermal physics, the effect of flight loads and is highly dependent on the engine component movements, the operating conditions, and the supporting hardware. Due to the number of functional and physical interfaces in the engine, seal design is therefore a highly coupled multi-physics problem and requires multiple iterations during the design process to converge to a solution that meets system requirements and optimizes engine specific fuel consumption. At different stages of the design process, simulation models with different levels of fidelity can be built. Due to the long runtimes of high-fidelity coupled multi-disciplinary models and to the iterative nature of the process, seal design in industry presents significant computational cost challenges, in particular in the phases of the design that require multiple simulation runs. Multi-fidelity computational techniques for surrogate modelling and optimization such as Kriging and co-Kriging have been demonstrated on a number of industrial applications and have the potential to significantly reduce the number of function evaluations for computationally expensive optimization problems, improve the accuracy of the predictions of surrogate models and allow the development of improved simulation strategies for a specific product design. This paper demonstrates the use of multi-fidelity simulation techniques on aero engine secondary air system seal design and shows how these techniques can be used in the context of system, sub-system and component design. This is achieved by combining results from a simple two-dimensional Finite Element Analysis with those from a coupled secondary air system-thermomechanical model. Depending on the stage of the design process and on the specific design decisions being made, the use of computational power in simulation often comes down to a trade-off between reduced overall computational time and improved result accuracy. Multi-fidelity simulation frameworks provide the environment to drive holistic choices on the simulation strategy, reducing the cost of the design and offering agility in the industrial response to market changes or new technologies. Moreover, this methodology establishes an infrastructure for updating the virtual product at each step of the product lifecycle, allowing experimental or service data to feed the system-level simulation models to produce a digital twin.
更多查看译文
AI 理解论文
溯源树
样例
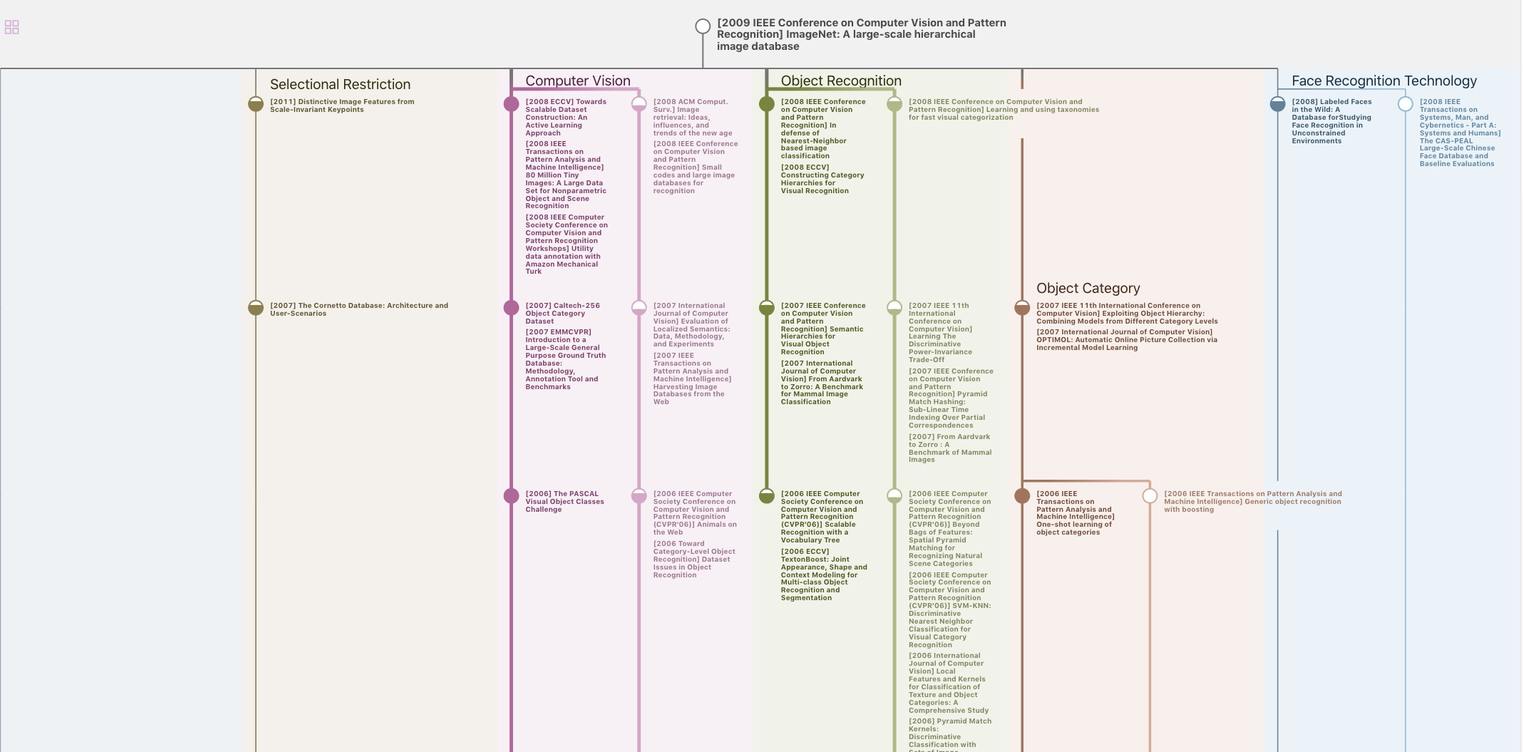
生成溯源树,研究论文发展脉络
Chat Paper
正在生成论文摘要