Fatigue Damage Analysis of Aluminum Alloy 6061 Based on CT Scanning
Journal of Materials Engineering and Performance(2022)
摘要
Dynamic spatial distribution and evolution of three-dimensional (3D) voids/cracks in engineering materials are crucial information to predict fatigue damage and residual life. A method of fatigue damage analysis was proposed and used to estimate low-cycle fatigue damage. First, multi-stage fatigue damage defects were measured based on x-ray computed tomography (XCT). 3D voids/cracks were reconstructed and analyzed by VG Studio and Diego algorithm. Then, 3D voids/cracks were transferred into finite element model along with material domain for numerical analysis. Thirdly, the damage transformation process was achieved by means of 3D finite element analysis. And the numerical and experimental results were compared. The estimated damage variables in terms of effective elastic modulus were in agreement with experimental results. It is indicated that the proposed numerical prediction method is valid for damage evolution in low-cycle fatigue.
更多查看译文
关键词
damage evolution, elastic modulus, finite element analysis, multi-stage fatigue
AI 理解论文
溯源树
样例
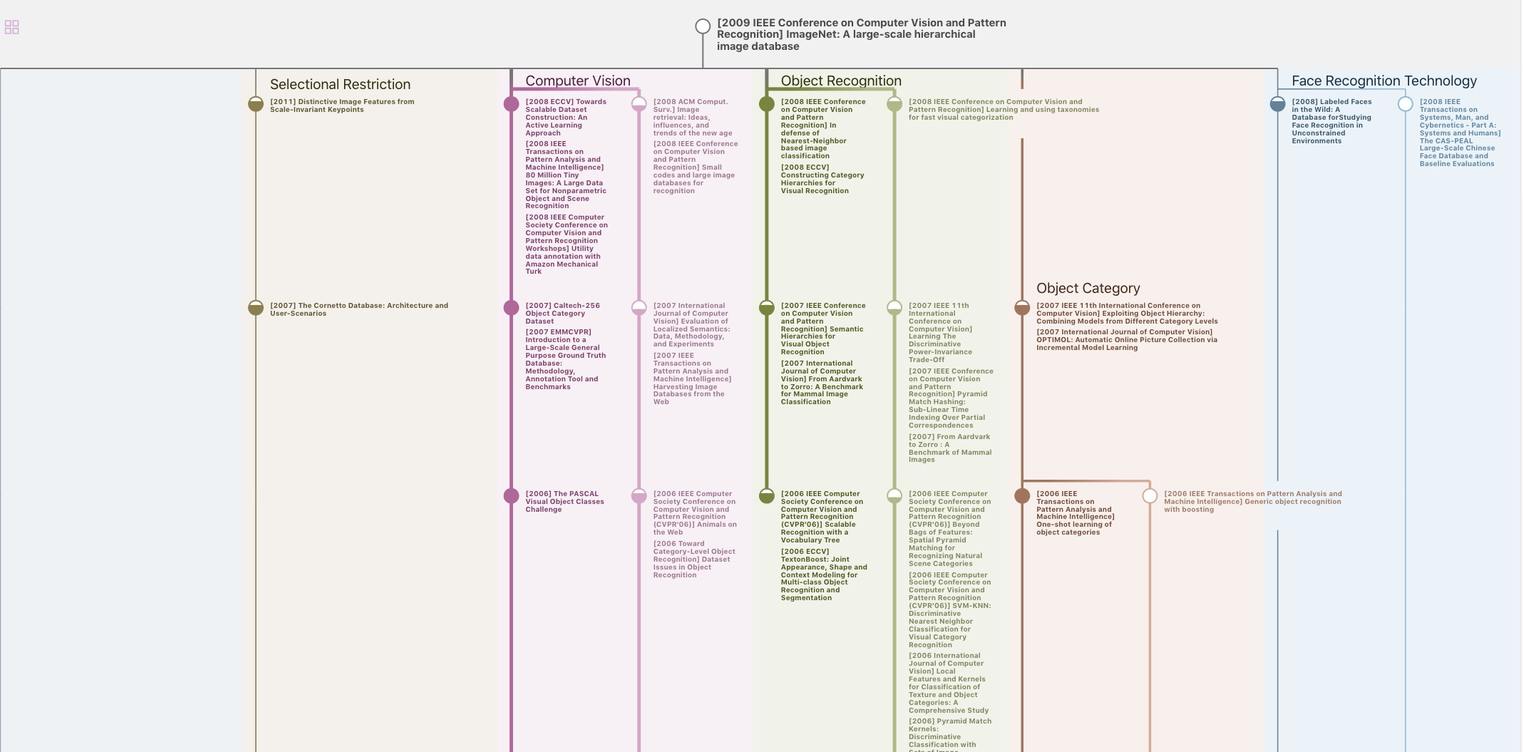
生成溯源树,研究论文发展脉络
Chat Paper
正在生成论文摘要