Design and manufacture of a shape-adaptive full-scale composite hydrofoil using automated fibre placement
INTERNATIONAL JOURNAL OF ADVANCED MANUFACTURING TECHNOLOGY(2022)
摘要
Robotic manufacturing using automated fibre placement (AFP) provides the foundation for efficient, low labour intensive, high accuracy and repeatable composite manufacturing. This paper presents a novel manufacturing process used to build a full-scale shape-adaptive composite hydrofoil using AFP. The outer layers of the hydrofoil were made up of carbon-fibre/epoxy plies laid up by AFP. The inner core of the hydrofoil was made from an E-glass/epoxy laminate, which was used as a rotatable “core-wrap” mandrel to place the carbon plies on. This type of core-wrapping manufacturing process allowed the consolidation of continuous carbon fibres around the leading and trailing edges and minimised the risk of premature delamination failure. Fibre orientations of the AFP-laid carbon plies were optimised using a genetic algorithm for a shape-adaptive response, and the manufacturing process from the layup to the curing is presented. The manufacturing downtime, dimensional variation and AFP-inherent imperfections and underlying reasons for their occurrence were discussed for future improvement. It was found that the manufactured hydrofoil has a lower laminate thickness than the expected profile due to not using female moulds during the cure process. About half of the AFP operation time was spent on several downtimes such as ply inspection and layup rework. Intrinsic tow defects such as tow upfolding and wrinkling mostly occurred around the narrow-curvature trailing edge and contributed largely to layup rework time.
更多查看译文
关键词
Automated fibre placement,Manufacturing,Composite hydrofoil,Optimisation
AI 理解论文
溯源树
样例
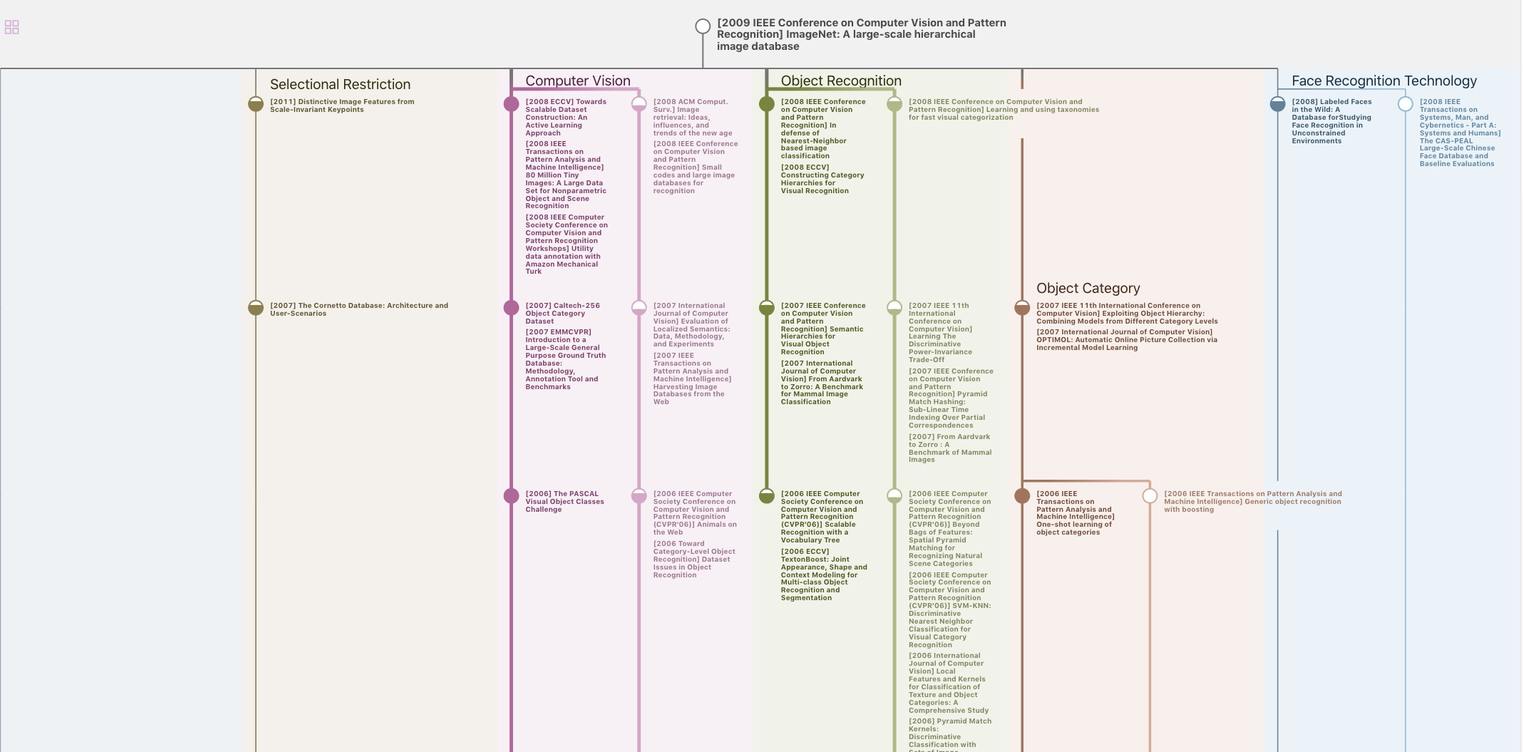
生成溯源树,研究论文发展脉络
Chat Paper
正在生成论文摘要