Digital-twin based real-time resource allocation for hull parts picking and processing
Journal of Intelligent Manufacturing(2024)
摘要
The development of Industrial Internet of Things, big data, and multi-domain modeling, led to the emergence of digital twin (DT), providing a new approach to the cyber-physical production systems. In the traditional shipbuilding industry, a large number of hull parts are often tracked and transferred. During the hull parts picking and processing, the uncertainty from parts transfer tasks and logistics information often leads to low resource utilization. Therefore, a real-time resource allocation method based on DT for hull part smart picking and processing system (SPPS) is proposed. Firstly, a multi-agent model of the multi-gantry crane system is established in virtual space to achieve real-time task allocation, hence minimizing the transport time. Next, a real-time picking and processing scheduling policy is proposed to reduce the idle time of all workstations by estimating the time of parts arriving at target station and processing completion time. Finally, the services available in the DT platform can be applied to optimize the system performance, taking the number of devices and the takt time optimization as examples. Several experiments in case study are carried out to verify the proposed method. The average utilization rate of all workstations is increased by 17.39%, and the standard deviation is reduced by 83.31%. The results have shown that the proposed method can effectively improve the workstation utilization rate and load balance. The maximum average number of parts in the station buffer, which is limited to 0.33, is kept at a low level.
更多查看译文
关键词
Resource allocation,Multi-gantry system,Digital twin,Real-time scheduling,Shipbuilding industry
AI 理解论文
溯源树
样例
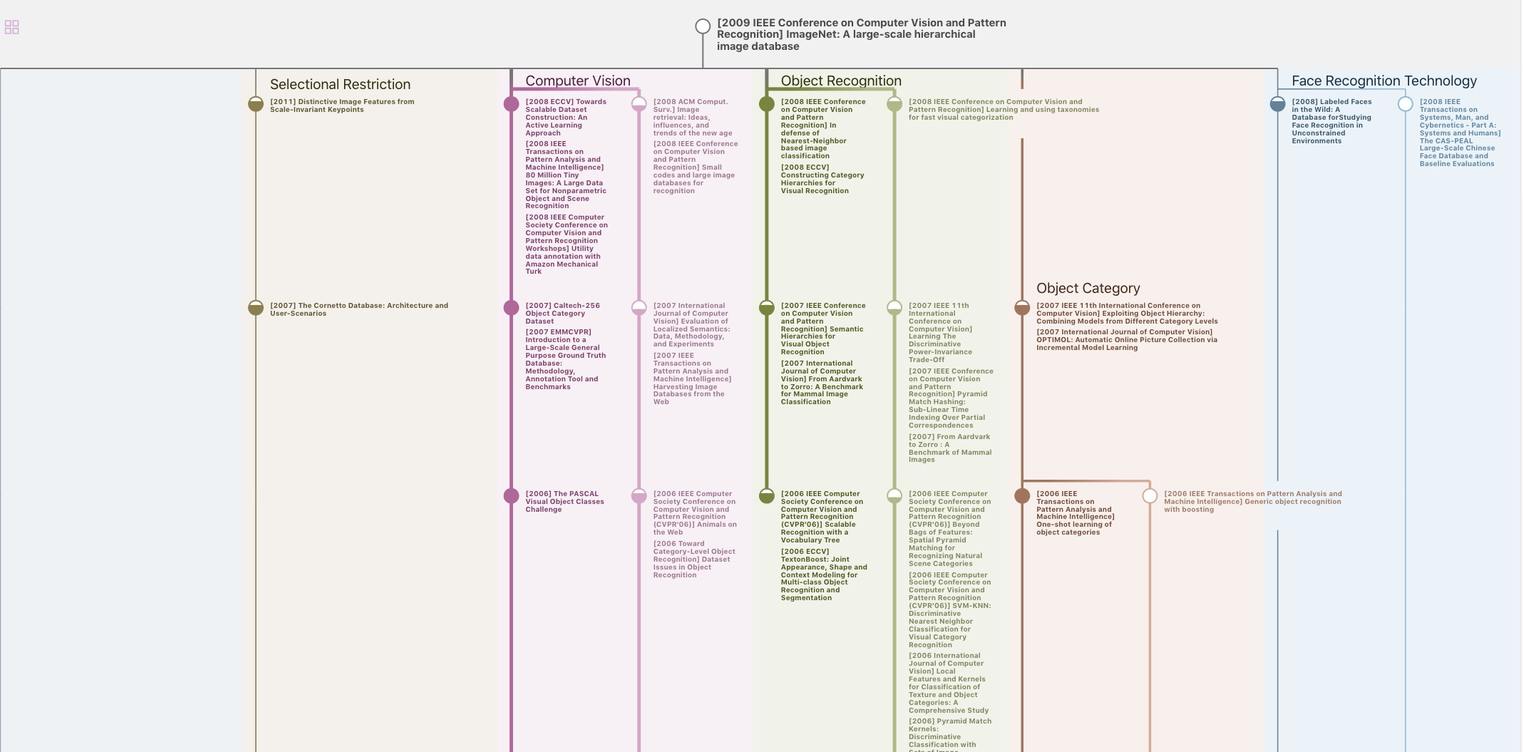
生成溯源树,研究论文发展脉络
Chat Paper
正在生成论文摘要