Iterative closest point-based data fusion of non-synchronized in-situ and ex-situ data in laser powder bed fusion
Journal of Manufacturing Systems(2023)
摘要
With the development of additive manufacturing (AM) processes, a variety of methods and technologies for process monitoring and post-process inspection have become available. These, together with modern computerized machines, generate large amounts of data about the process. Hence, efficient analysis methods for extracting useful information and knowledge from these datasets are needed. This paper presents a method for automated data fusion of machine input toolpath commands, on-axis intensity monitoring, and Computed Tomography (CT) scan measurement data in laser metal powder-bed fusion AM. The iterative closest point (ICP) point-clouds registration method is used for fine spatial alignments of (1) on-axis intensity measurements with machine input toolpath commands and (2) machine input toolpath and CT scan. The input-toolpath point cloud is selected as the reference point cloud. We further propose a post-processing method that can correct part of the wrong connections between measurements and toolpath points as results of ICP registration. The proposed method is suitable for merging data where there is no temporal synchronization between the machine commands and the monitoring system, and where the actual laser scan path may deviate from the machine input toolpath commands, e.g., due to dynamics constraints of scanning galvo mirror system. The method is designed to handle dynamic changes in input process parameters such as dynamic changes in laser power and scan speed, which lays a solid foundation for advanced AM process control, qualification and certification. A practical solution for organizing and storing the fused data, which allows for efficient analysis, is also presented. The results show that the method can spatially align all three different types of data and find the corresponding input toolpath command for each measurement point. The alignment of on-axis measurements and machine input toolpath commands has been improved by using a clustering algorithm. The main limitation is that, for estimating the improvement and error of spatial alignment, the average difference between the closest points of two point clouds is used, but this metric does not give an exact value of an actual registration error. The estimation of connectivity error is based on a visual comparison of registration results.
更多查看译文
关键词
Additive manufacturing,Data fusion,Data registration,Big data
AI 理解论文
溯源树
样例
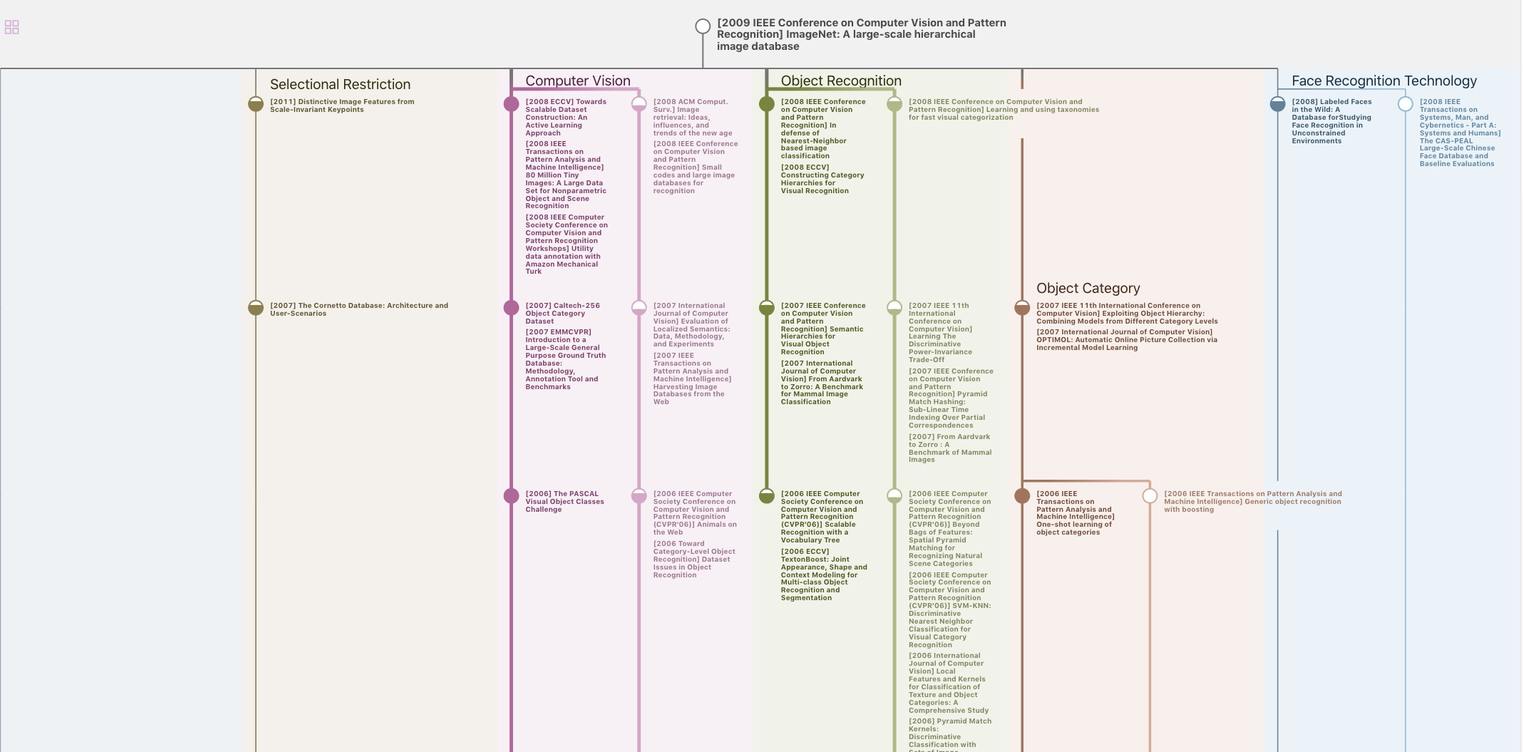
生成溯源树,研究论文发展脉络
Chat Paper
正在生成论文摘要