Microspine Design for Additive Manufacturing
2022 IEEE/RSJ International Conference on Intelligent Robots and Systems (IROS)(2022)
摘要
Microspine grippers allow robots to ascend steep rocky slopes and cliff faces, enabling scientific exploration of exposed strata on Earth and other solar system bodies. Historically, the Shape Deposition Manufacturing (SDM) process has been used to fabricate multi-material suspensions for load-sharing among multiple microspines. We instead apply the Hybrid Deposition Manufacturing (HDM) process to microspine fabrication, and we further propose a novel 3D-printed microspine suspension design that can be manufactured via Fused Deposition Manufacturing (FDM) alone, using a single flexible material with an embedded fishhook. We use a model of microspine stiffness that allows designers to compensate for order-of-magnitude changes in material tensile modulus by adjusting geometric parameters of the design. The stiffness model and the FDM microspine design are validated through tensile testing, and mechanical properties of the HDM and FDM designs are compared against a standard SDM microspine design. We demonstrate that the FDM process can produce microspines with equivalent normal and axial stiffness and superior maximum load and fatigue response to SDM microspines, and discuss additional advantages of the FDM process for rapid prototyping and broader accessibility.
更多查看译文
关键词
3D-printed microspine suspension design,additive Manufacturing,axial stiffness,cliff faces,embedded fishhook,fatigue response,FDM process,fused deposition manufacturing,HDM,hybrid deposition manufacturing process,load-sharing,material tensile modulus,mechanical properties,microspine grippers,multimaterial suspensions,rapid prototyping,robots,SDM,shape deposition manufacturing process,single flexible material,solar system bodies,steep rocky slopes,tensile testing
AI 理解论文
溯源树
样例
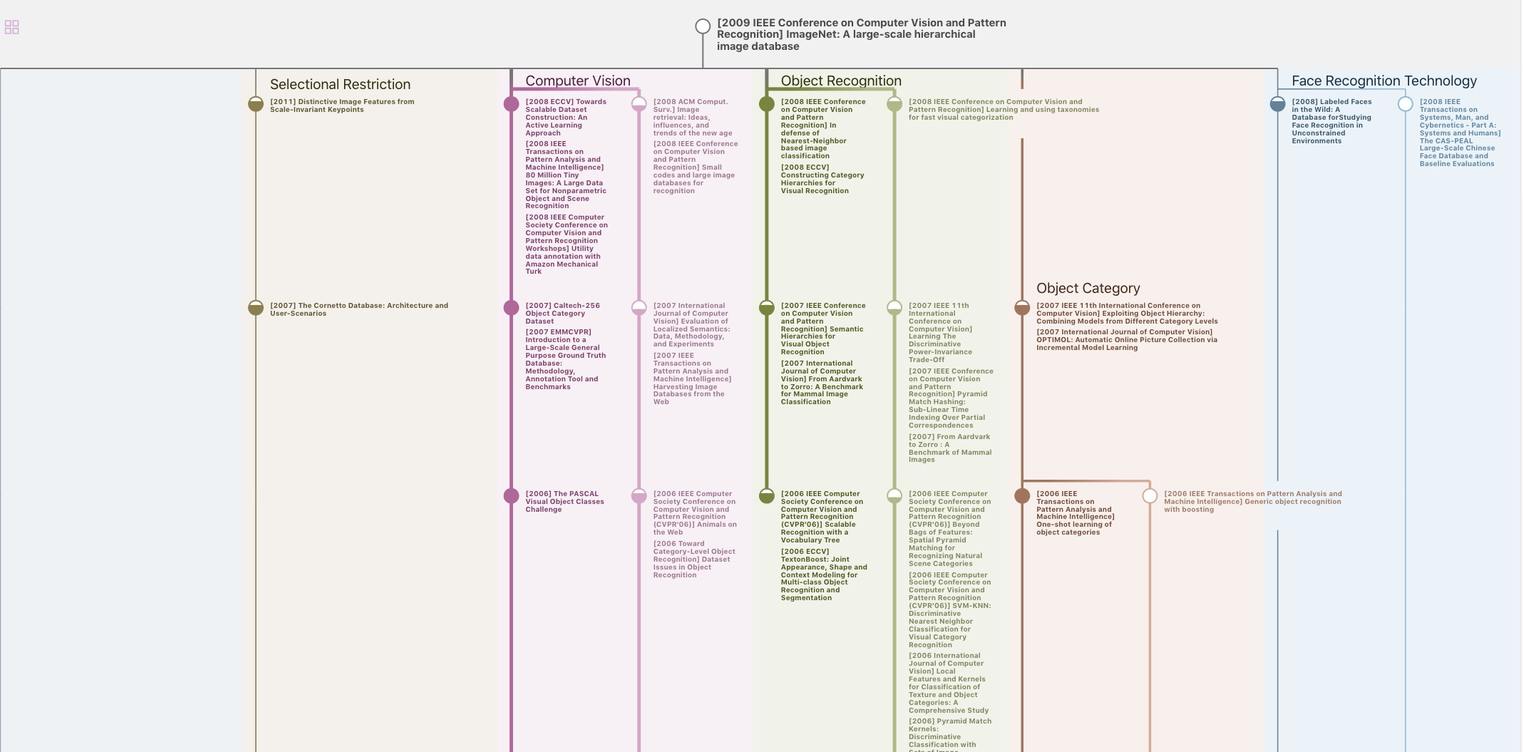
生成溯源树,研究论文发展脉络
Chat Paper
正在生成论文摘要