Compensation method of wire electrode wear for reciprocating micro wire electrical discharge machining
Journal of Manufacturing Processes(2023)
摘要
Reciprocating micro wire electrical discharge machining (Micro-WEDM) has the advantage of high thickness cutting because it mainly relies on the high wire speed to remove discharge production. The wire electrode wear (WEW) not only affects the machining stability and quality, but also greatly increases the risk of wire breakage in long cycle machining. Aiming at the WEW of the micro wire electrode used in reciprocating, a method of introducing compensation voltage between pulse interval (Toff) is proposed in this paper. This method can enhance the existing electrochemical effect in WEDM and compensate the WEW by means of metal ion reduction deposition effect. The verification experiment of no-load pulse indirectly shows the feasibility of the compensation method. Too large compensation voltage will affect the Toff deionization and machining stability. Its value should be less than the maintenance voltage of normal discharge. The average thickness of recast layer decreases first and then increases with the increase of compensation voltage. The minimum thickness of recast layer is about 4.7 μm at 15 V, which is 62.4 % lower than that without compensation voltage. The high conductivity dielectric can reduce the WEW, while the compensation voltage can greatly enhance this effect. Compared with the initial cutting stage,the micro wire electrode has no wear basically until the cutting area exceeded 50,000 mm2, and the cutting speed maintains above 45 mm2/min. The distribution of elements on the surface of wire electrode indicates that the strength of electrolysis is improved by the method of WEW compensation.
更多查看译文
关键词
Micro-WEDM,WEW,Compensation voltage,Electrolysis,Recast layer
AI 理解论文
溯源树
样例
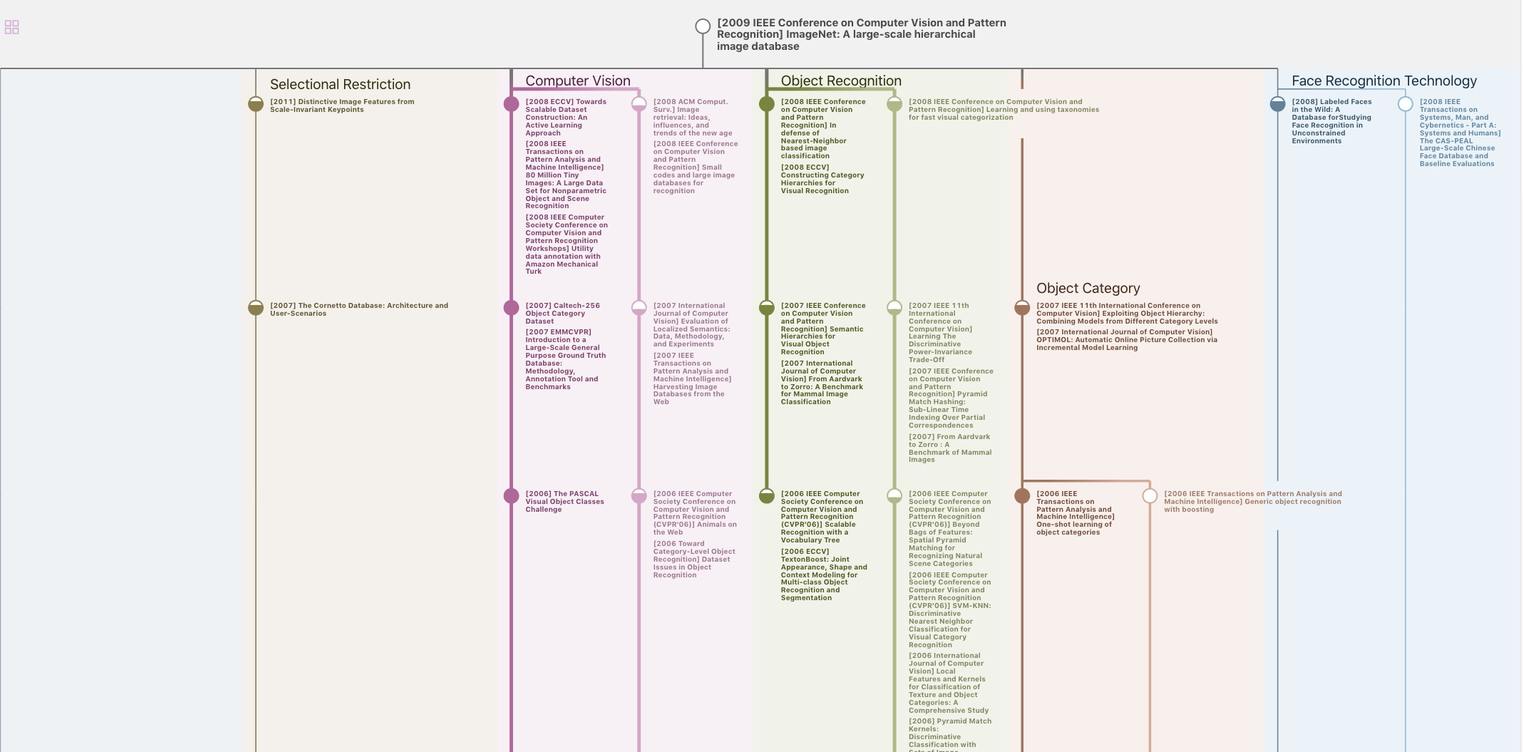
生成溯源树,研究论文发展脉络
Chat Paper
正在生成论文摘要