Study on milling tool wear morphology and mechanism during machining superalloy GH4169 with PVD-TiAlN coated carbide tool
Tribology International(2023)
摘要
Tool life, dimension accuracy and surface quality of workpiece, intelligent operation and maintenance of automated production are closely related to tool wear. However, for many years, relevant scholars have mainly focused on the research of the tool wear mechanism in the sharp wear stage, mainly involving various machining methods, various superalloy materials, various tool materials and geometric parameters, and different coolant methods et, al. The morphology and mechanism of tool wear need to be further studied in the initial and steady wear stage, which is helpful to ensure the dimensional accuracy and surface quality of workpiece, especially in the finishing stage. 45 groups of tool wear experiments are carried out under dry condition during milling of GH4169 with PVD-TiAlN coated carbide tools. The tool wear micro-topography, tool wear curve, tool cutting force, spindle motor current, tool wear mechanism, chip topography and machined surface topography were investigated during the milling tool wear. The tool wear mechanism in the sharp wear stage was further explored by SEM, EDS and XRD, which will help to deeply gain the milling characteristics of GH4169 and help to test the cutting performance of the tool. The results show that during the tool wear process of milling superalloy GH4169, severe abrasive wear and adhesive wear occur in large numbers, the rate of tool wear is fast, the cutting force increases, the current of the spindle motor increases, and the tool coating and substrate material were worn seriously, the main tool wear mechanisms are abrasive wear, adhesive wear, oxidative wear and breakage. Severe abrasive wear occurs between lots of hard abrasive carbides in the workpiece material and the rake and flank faces of the milling tool. Fe, Cr, Al, etc. were found on the rake and flank faces, and the adhesive wear was very serious. Many oxides (Al2O3, Fe2O3, etc.) appear on the rake and flank surfaces, which indicate that oxidative wear occurs. Due to the periodic intermittent cutting during the milling process, the breakage of milling tool edge is very serious. Chips or adherents with different microscopic topographies were adhered to the tool wear area due to extrusion and stretching in the sharp wear stage. The machined surface micro-topography of the workpiece, which affected by tool wear, was greatly of difference during the entire wear stage.
更多查看译文
关键词
Milling,Inconel 718,Tool wear morphology,Tool wear mechanism,Milling force,Spindle motor current
AI 理解论文
溯源树
样例
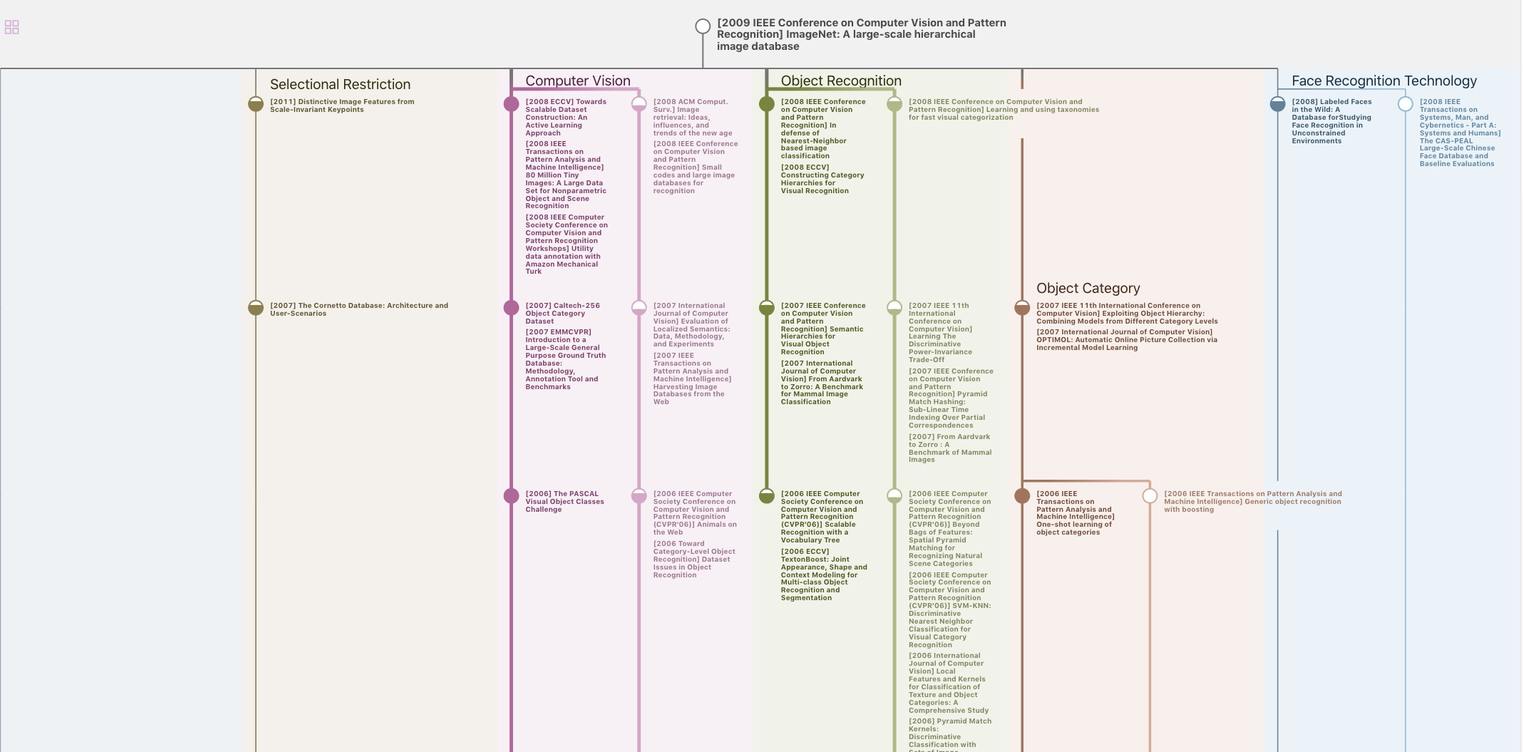
生成溯源树,研究论文发展脉络
Chat Paper
正在生成论文摘要