Computer-controlled finishing via dynamically constraint position-velocity-time scheduler
Journal of Manufacturing Processes(2023)
摘要
In a Computer Numerical Controlled (CNC) finishing process, the target material removal from an optical surface is guided by the convolution between the influence function of a machine tool and its dwell time at certain points over the surface. To reduce dynamics stressing and increase machining efficiency, the dwell time must be converted to varying velocities, which are the actual inputs to the machine tool controller. Conventionally, the conversion assumed constant acceleration and relied on linear motion interpolation, which caused discontinuities in velocities. This unsmooth motion affects the material removal distribution, and, thus, the accuracy of the finished surface shape. Many modern CNC machines support the smoother, cubic-polynomial interpolated Position-Velocity-Time (PVT) motion mode; however, the conventional scheduler may fail to provide suitable velocities for the PVT. This study answers this challenge by proposing a novel PVT-based velocity scheduler that achieves smooth motion while considering CNC dynamic limits. Firstly, the principle of the PVT is explained, and the PVT-based velocity scheduler is formulated. Secondly, a quadratic programming is used to optimize the velocities by imposing the CNC dynamic constraints and the C1 continuities (zeroth and first derivatives are continuous) simultaneously. Thirdly, the smoothness and accuracy of the scheduled velocities are studied on different kinds of tool paths via simulation. Finally, a sub-0.3 nm level surface finishing experiment using ion beam figuring is demonstrated to verify the feasibility of the proposed method. The PVT-based scheduler and simulator code is open-sourced.
更多查看译文
关键词
Correction polishing,Position -velocity -time,Feed drive control,Ion beam figuring,Sub-nanometer finishing,Computer -controlled optical surfacing
AI 理解论文
溯源树
样例
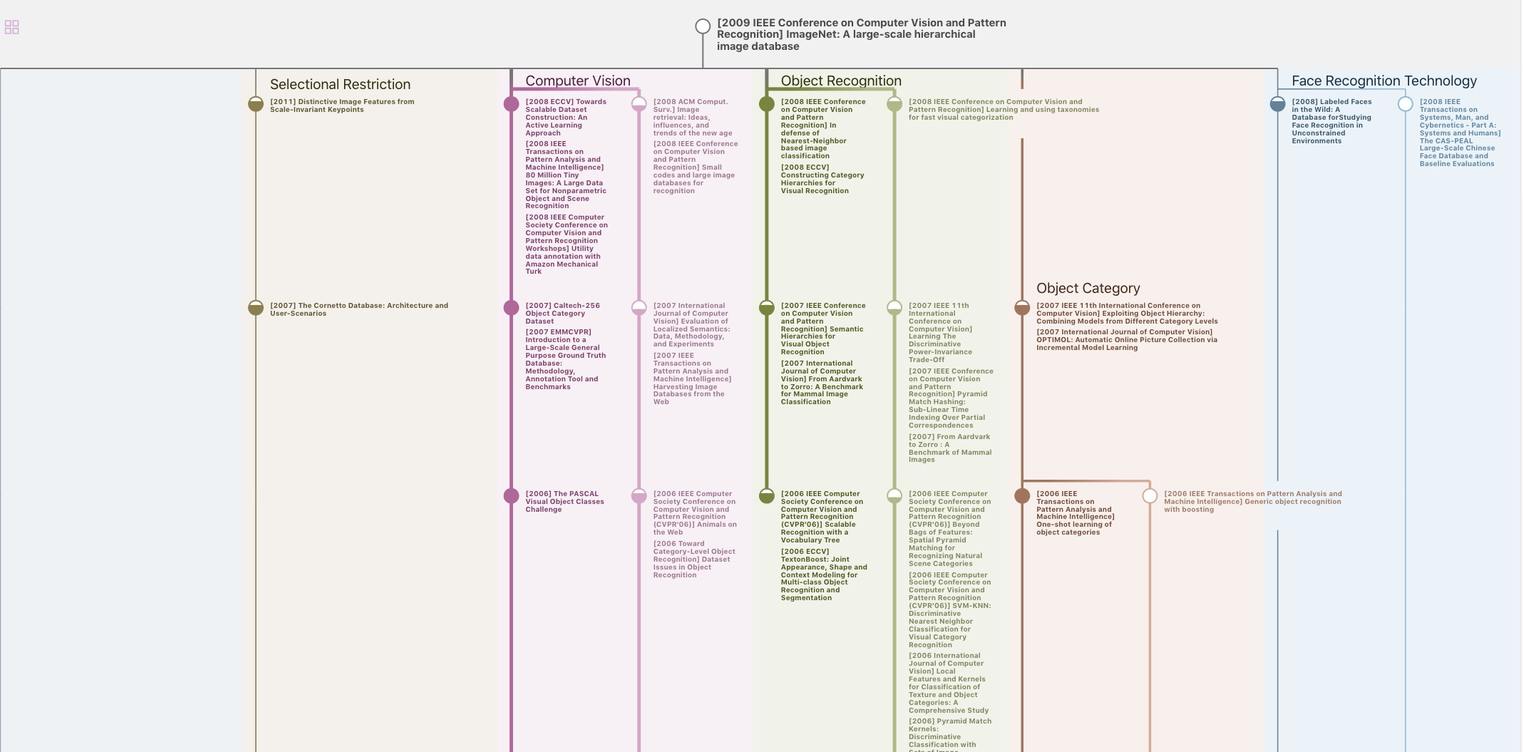
生成溯源树,研究论文发展脉络
Chat Paper
正在生成论文摘要