Enhanced flexibility and thermal conductivity of HfC decorated carbon nanofiber mats
CARBON(2023)
摘要
Future-generation spacecraft components allude discovery of novel materials that can withstand extreme envi-ronments (>2000 degrees C). The combined effect of ultra-high temperature ceramics (UHTCs) and carbon fibers (Cf) can satisfy the demanding requirements of aerospace applications. A novel, hybrid, and flexible hafnium carbide (HfC)-decorated carbon nanofiber (Cnf) mat was fabricated via electrospinning. Enhanced thermal stability of the flexible HfC decorated Cnf over Cnf can be elucidated from the 20-fold increment in thermal conductivity and the onset of degradation at higher temperatures (840 degrees C). Successful integration of multi-layered sandwich lattice using in-housed fabricated HfC decorated Cnf showed retention of the fibrous structure even after extreme spark plasma sintering (SPS) process at 1850 degrees C. Fabricating a similar multi-layered structure using procured Cf was unsuccessful due to bundled agglomeration and micron-sized fibers. High-load indentation suggests that HfC decorated Cnf interlayer is stronger (-2.3 times) than the parent UHTC with no cracking at the interface. Compared with the HfC matrix, the indentation-damaged area at the interface reduced up to-56% due to toughening mechanisms such as Cnf, fiber pull-out and bridging. The synthesized HfC decorated Cnf mat is proposed as an ultra-thin filler material for joining similar or dissimilar UHTCs while maintaining similar chemistry and better mechanical integrity at the interface. The findings insinuate a new paradigm in designing hybrid and flexible ceramic-containing materials for thermal protection systems (TPS) of future-generation spacecraft components that can mitigate failure in extreme environments (>2000 degrees C).
更多查看译文
关键词
Electrospinning,Hafnium carbide (HfC),Spark plasma sintering (SPS),Layered structure
AI 理解论文
溯源树
样例
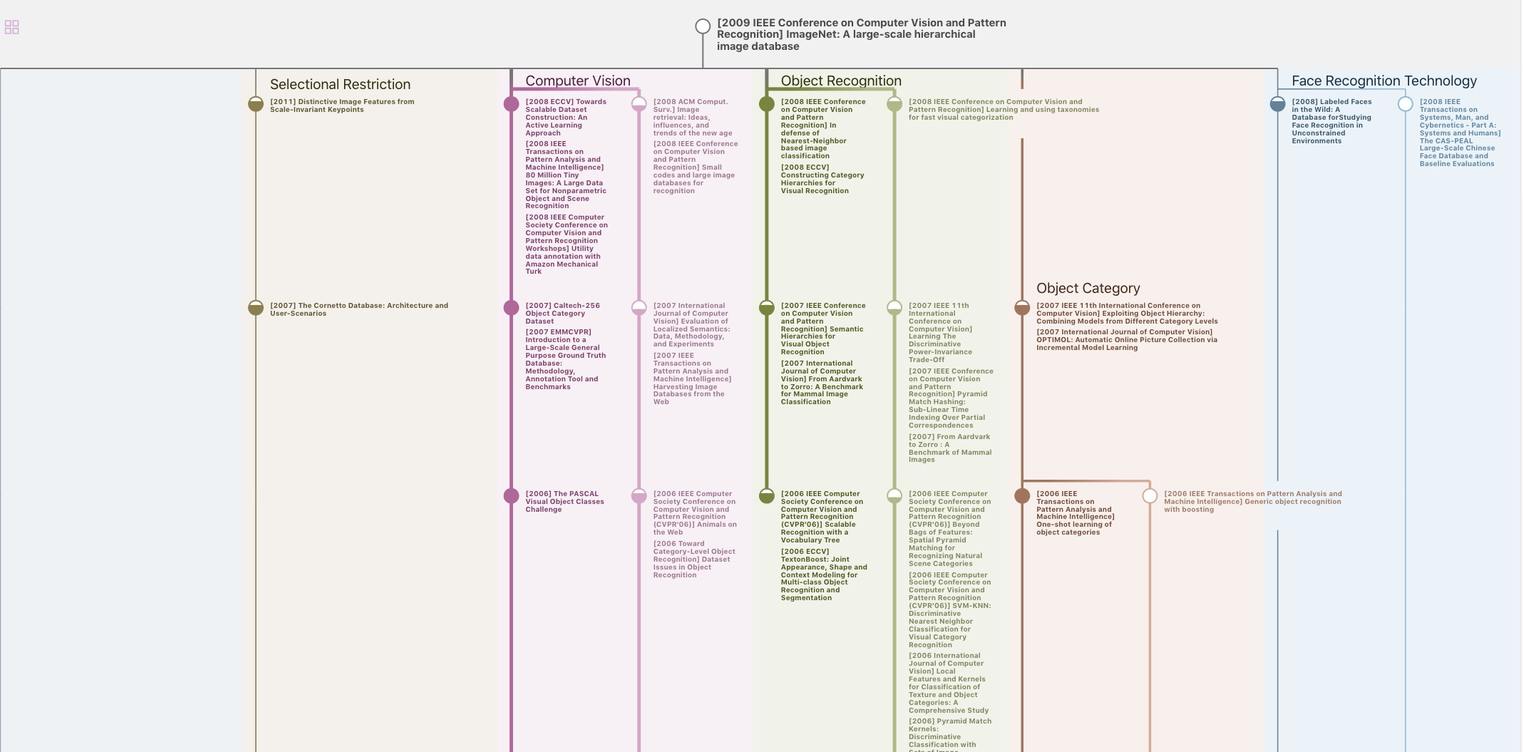
生成溯源树,研究论文发展脉络
Chat Paper
正在生成论文摘要