A coupled ray-tracing based CFD and cellular automaton model for predicting molten pool formation and microstructure evolution in narrow gap laser welding
INTERNATIONAL JOURNAL OF HEAT AND MASS TRANSFER(2023)
摘要
Laser beam reflection plays a significant role in the temperature development history during various laser material processes. Different from other processes where laser beam reflection main happens inside the keyhole, in narrow gap laser welding (NGLW), the laser beam would interact with the sidewalls multiple times before existing the narrow groove, which would have a great impact on the defect formation as well as the grain structure development. However, the underlying mechanism of this process remains unknown in multi-pass NGLW. In this study, an integrated ray-tracing based CFD and cellular automaton (CA) modelling framework is established to investigate the impact of laser beam reflection on molten pool formation and microstructure evolution in multi-pass NGLW. From the CFD simulation, it is found that the overall laser beam absorption of NGLW is greater than laser metal deposition (LMD) while smaller than laser powder bed fusion (LPBF) process. Besides, the overall absorptivity in NGLW is increased 28% when considering the ray reflection during the first welding pass. The absorptivity would increase and then stabilise through the multi-pass welding process, which is attributed to the change in incident angle and number of reflections. Additionally, it is found that the undercut defect is more likely to occur with ray reflection due to the excessive temperature rise on the sidewalls, while lack of fusion is observed in the case without ray reflection. By incorporating the thermal history of each welding pass with CA, the impact of laser beam reflection on grain structure development is evaluated. Columnar grains would govern the microstructure evolution in the case with ray reflection, which grow epitaxially from the fusion line to the molten pool centre. Grain coarsening would occur around the lack of fusion region in the case without ray reflection. Moreover, the analysis on grain size distribution is conducted and a greater maximum grain size is obtained in the case without ray reflection as a result of lower cooling rate caused by lack of fusion. However, a higher grain size increase is obtained in the case with ray reflection during multiple welding passes, and larger grains are expected to form if more welding passes are to be conducted. The simulated molten pool morphology and grain structure are compared with the experimental observation, and a good agreement is achieved.
更多查看译文
关键词
molten pool formation,cellular automaton model,microstructure evolution,ray-tracing
AI 理解论文
溯源树
样例
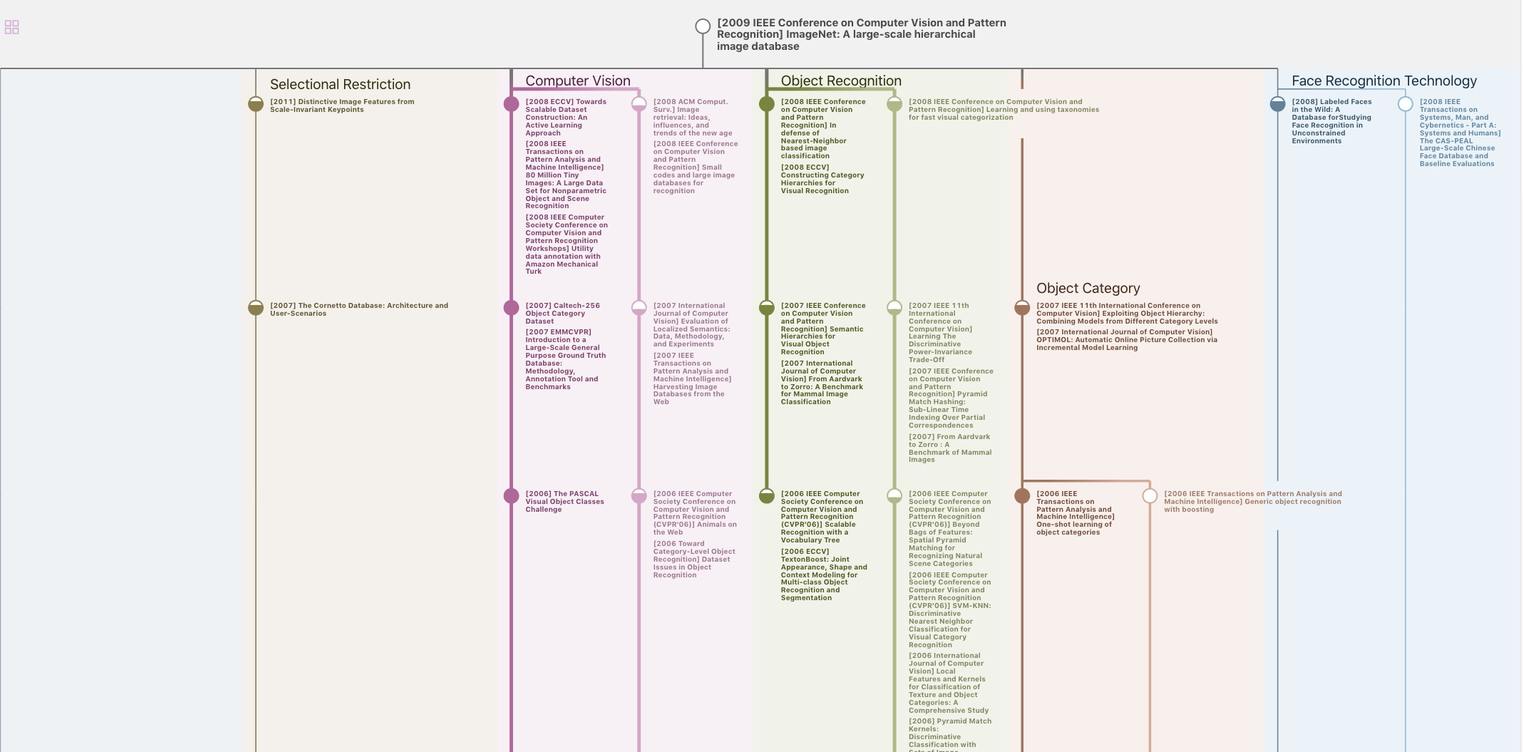
生成溯源树,研究论文发展脉络
Chat Paper
正在生成论文摘要