Energy balance model to predict the critical edge radius for adhesion formation with tool wear during micro-milling
Journal of Manufacturing Processes(2023)
摘要
Cutting edge of the micro-milling tool rapidly loses its sharpness and experiences early adhesion that degrade the machinability and surface quality. Although rapid edge-rounding and early adhesion were reported in the literature, the condition that promotes the adhesion development was not established. For dry machining of Ti-6Al-4V with TiAlN-coated WC-6Co micro-mills, an energy balance model is proposed in this article that guides the condition for the onset of adhesion with progressive tool wear. Initially, tool wear progression through successive stages of rapid abrasion, steady abrasion, adhesion, and edge-chipping is experimentally characterised. Adhesion at the tool-tip is found to develop when the abrasively worn-out edge radius reaches a critical value. Thereafter, a model is presented considering the dynamic growth of the dead metal zone (DMZ) with tool wear to capture the changes in the tribological contact and stress distribution at the interfaces. The chip-DMZ contact is the crucial factor in governing the critical edge radius for adhesion initiation, while the chip-tool contact has no direct role. Adhesion occurs when worn-out edge radius reaches 3.98–4.26 μm during micro-milling at a low feed of 1.0 μm/flute, whereas 4.0 μm/flute feed permits adhesion-free cutting up to 5.02–5.32 μm edge radius. Higher speed can favourably retard adhesion development. The inherently occurring phenomena like chip accumulation and non-cutting passes in low-feed micro-milling can favourably extend adhesion-free machining. However, coating delamination promotes adherence at an early stage in high-feed machining.
更多查看译文
关键词
Micro-milling,Edge radius,Tool wear,Dead metal zone,Adhesion,Tool life
AI 理解论文
溯源树
样例
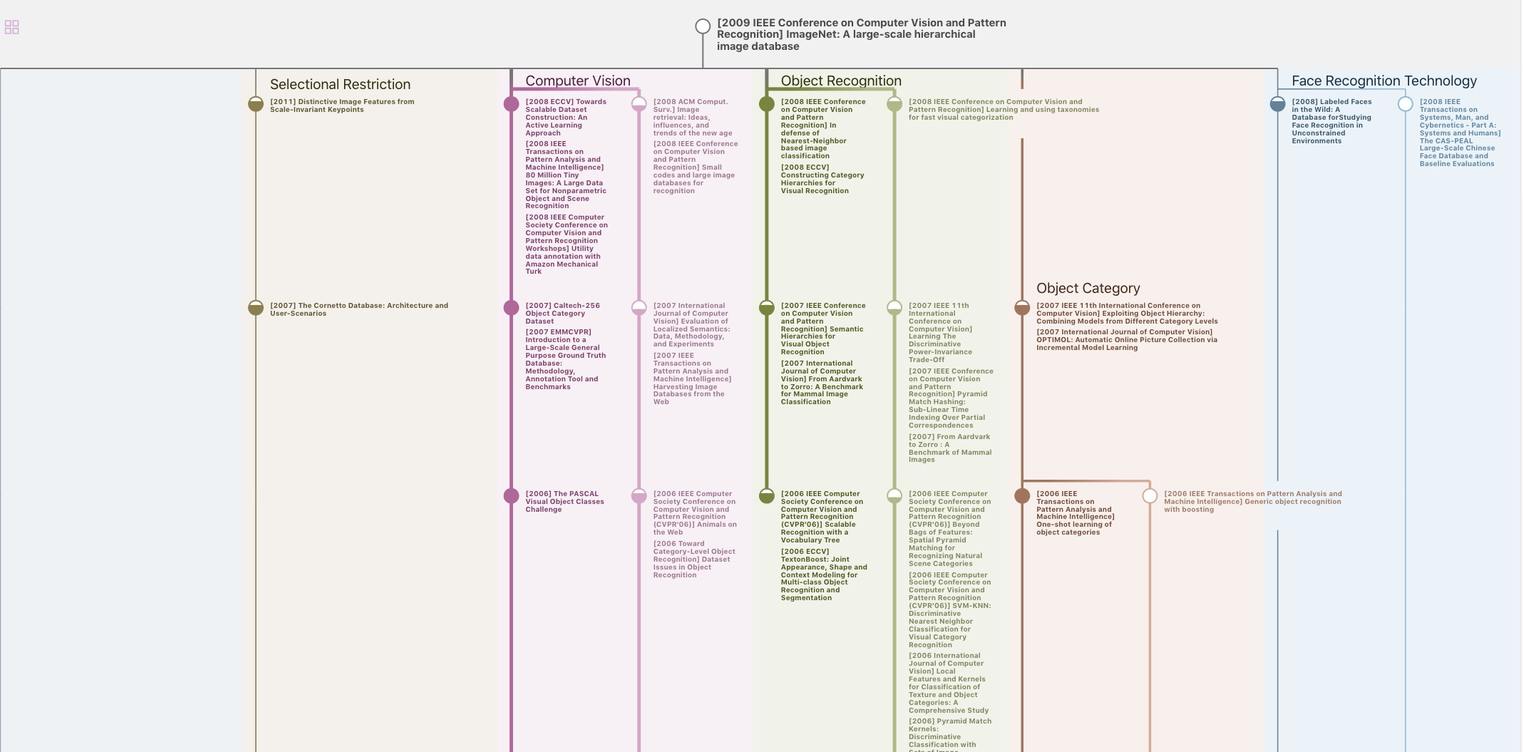
生成溯源树,研究论文发展脉络
Chat Paper
正在生成论文摘要