Case Study 2. Raw Material Receipt Process Optimization
Synthesis lectures on engineering, science, and technology(2023)
摘要
Currently, manufacturing companies face problems that prevent them from achieving their goals of delivering products on time to satisfy their customers. This chapter reports a case study of a manufacturing company that presents a problem in the Warehouse area, specifically in receiving raw materials. It has been observed that the time it takes to receive materials can last up to 45 days, and the lack of storage space in the Receiving sub-area and operational stoppages have caused an excess of material inventory in this sub-area, forcing the company to work overtime. This translates into costs of more than 50,000 dollars. The general objective of this study is to reduce the material receiving process time, while the specific objectives are to increase by 50% the capacity of the labeling operation, reduce by 20% the activities of the raw material receiving process, and eliminate the extra time for raw material receiving. The Plan-Do-Check-Act (PDCA) cycle is applied together with the flow process chart, Ishikawa diagram and the 5’s are used to achieve this objective. At the end of the project, the results indicate that the process of receiving materials takes a maximum of 7 days, while the capacity of the labeling operation increases from 580 to 1,470 units (253.4% increase), and process activities are reduced from 37 to 20 (45.9% reduction), and overtime is eliminated in its entirety. In conclusion, the PDCA cycle, supported by tools such as the flow chart, the cause-effect diagram, and the 5’s, helps to reduce process times, increase process capacity, eliminate unnecessary operations, and eliminate extra work time.
更多查看译文
关键词
optimization,process,material
AI 理解论文
溯源树
样例
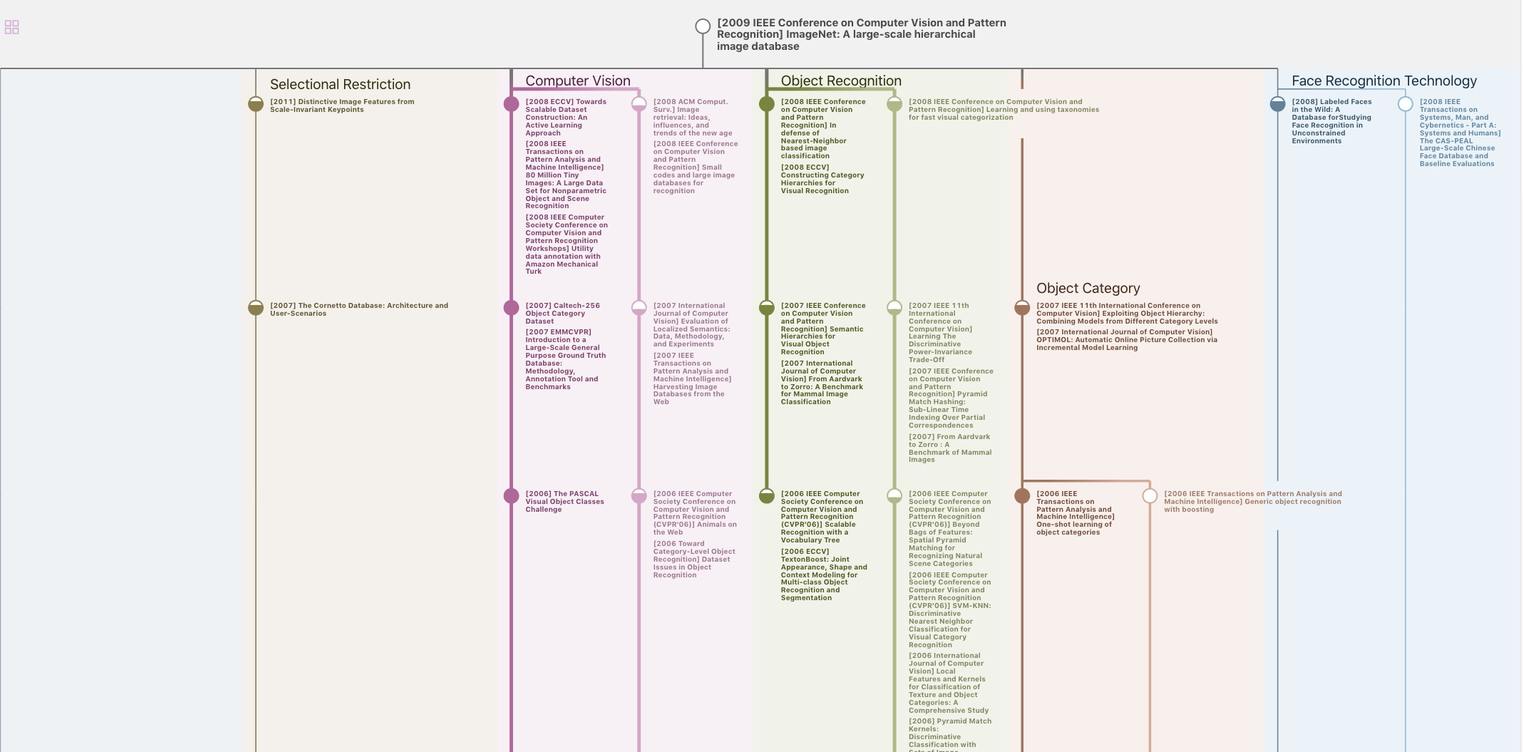
生成溯源树,研究论文发展脉络
Chat Paper
正在生成论文摘要