A Method to Identify Different Comb Gaps for MEMS Gyroscope at the Wafer Level Based on Negative Electrostatic Stiffness
IEEE Sensors Journal(2023)
摘要
For highly accurate micro-electromechanical systems (MEMS) gyroscopes, comb gap errors influence mechanical coupling errors and limit performance. In this study, an in situ method was proposed to identify the gaps of drive combs, drive-sense combs, and sense combs in MEMS gyroscopes that can be applied at the wafer level. Negative electrostatic stiffness of combs was considered in the model construction of the sense mode and the
${Y}$
-axis in-phase mode, and the frequency change caused by this was applied to characterize the comb gaps. Eight chips in different positions of a wafer were selected for verification of this method. The results shows that errors of drive comb gaps, drive-sense comb gaps, and sense comb gaps in the chip near the wafer center were 0.67, 0.60, and
$0.53 \mu \text{m}$
, respectively, and those in the chip at the wafer edge were 0.96, 0.95, and
$0.71 \mu \text{m}$
, respectively. The variation of comb gaps was
$0.08 \mu \text{m}$
in a single chip near the wafer center and
$0.03 \mu \text{m}$
in a single chip at the wafer edge. This work provides a method for fabless designers to explore the effect of the wafer process on the structures and reduce it through careful design.
更多查看译文
关键词
Comb gap, micro-electromechanical systems (MEMS) gyroscope, morphological identification, quadrature error, wafer level
AI 理解论文
溯源树
样例
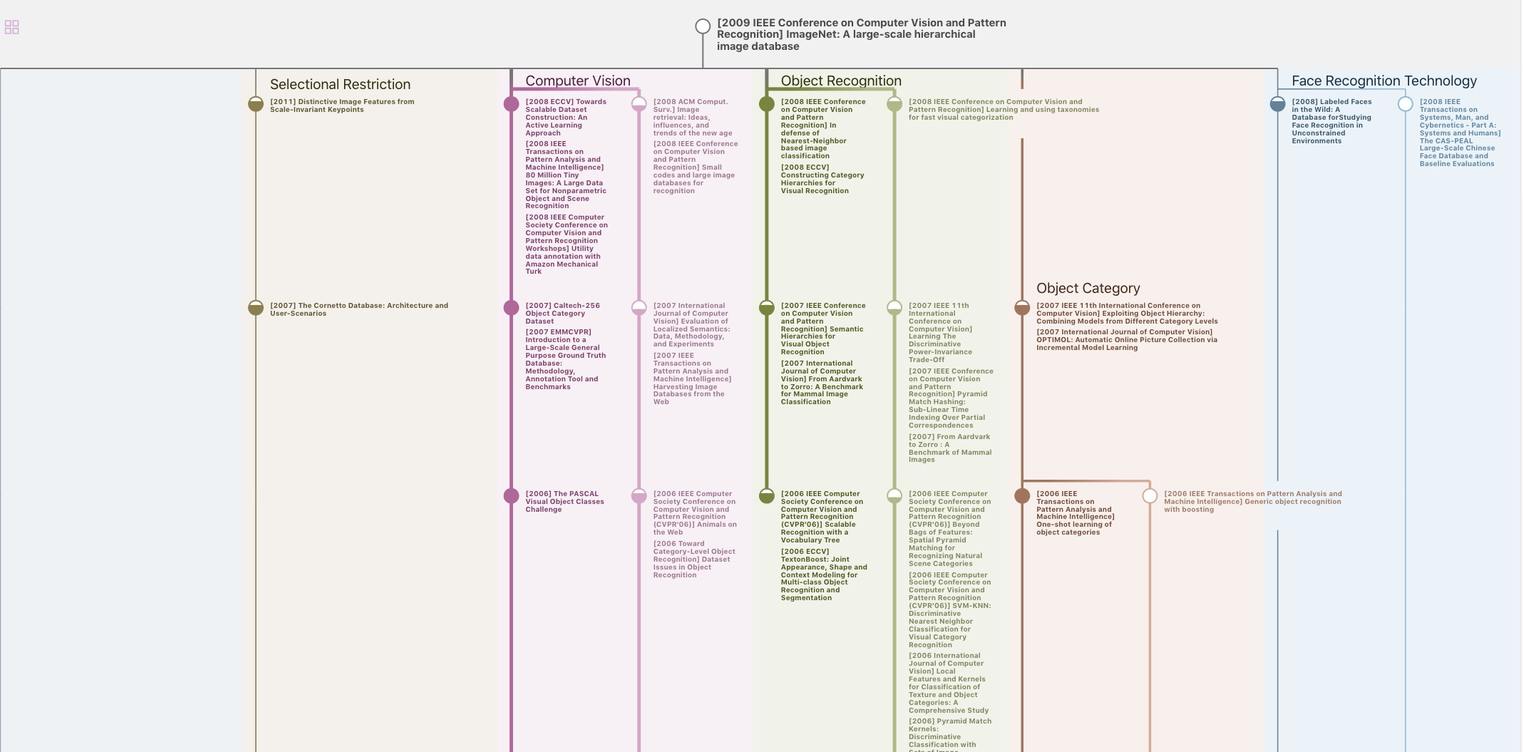
生成溯源树,研究论文发展脉络
Chat Paper
正在生成论文摘要