Automatic Classification of PDC Cutter Damage Using a Single Deep Learning Neural Network Model
Day 2 Wed, March 08, 2023(2023)
摘要
AbstractThere is considerable value in automatically quantifying cutter damage from drill bit pictures. Current approaches do not classify cutter damage by type, i.e., broken, chipped, lost, etc. We, therefore, present a computer vision model using deep learning neural networks to automate multi-type damage detection in Polycrystalline Diamond Compact (PDC) drill bit cutters.The automated bit damage detection approach presented in this paper is based on training a computer vision model on different cutter damage types aimed at detecting and classifying damaged cutters directly. Prior approaches detected cutters first and then classified the damage type for the detected cutters. The You Only Look Once version 5 (YOLOv5) algorithm was selected based on the findings of an earlier published study. Different models of YOLOv5 were trained with different architecture sizes with various optimizers using two-dimensional (2D) drill bit images provided by the SPE Drilling Uncertainty Prediction technical section (DUPTS) and labeled by the authors with training from industry subject matter experts. To achieve the modeling goal, the images were first annotated and labeled to create training, validation, and testing sub-datasets. Then, by changing brightness and color, the images allocated for the training phase were augmented to generate more samples for the model development. The categories defined for labeling the DUPTS dataset were bond failure, broken cutter, chipped cutter, lost cutter, worn cutter, green cutter, green gauge, core out, junk damage, ring out, and top view. These categories can be updated once the IADC upgrade committee finishes upgrading IADC dull bit grading cones.Trained models were validated using the validation dataset of 2D images. It showed that the large YOLOv5 with stochastic gradient descent (SGD) optimizer achieved the highest metrics with a short training cycle compared to the Adam optimizer. In addition, the model was tested using an unseen data set collected from the local office of a drill bit supplier. Testing results illustrated a high level of performance. However, it was observed that inconsistency and quality of rig site drill bit photos reduce model accuracy. Therefore, it is suggested that companies produce large sets of quality images for developing better models. This study successfully demonstrates the integration of computer vision and machine learning for drill bit grading by categorizing/classifying damaged cutters by type directly in one stage rather than detecting the cutters first and then classifying them in a second stage. To guarantee the deployed model's robustness and consistency the model deployment has been tested in different environments that include cloud platform, container on a local machine, and cloud platform as a service (PaaS) with an online web app. In addition, the model can detect ring out and cored damages from the top view drill bit images, and to the best of the authors’ knowledge, this has not been addressed by any study before.The novelty of the developed deep learning computer vision algorithm is the ability to detect different cutter damage types in a fast and efficient process compared to the current lengthy manual damage evaluation practice. Furthermore, the trained model can detect damages that frequently take place in more than one blade of the bit such as ring outs and coring. In addition, a user-friendly interface was developed that generates results in pdf and CSV file formats for further data analysis, visualization, and documentation. Also, all the technologies used in the development of the model are open source and we made our web app implementation open access.
更多查看译文
AI 理解论文
溯源树
样例
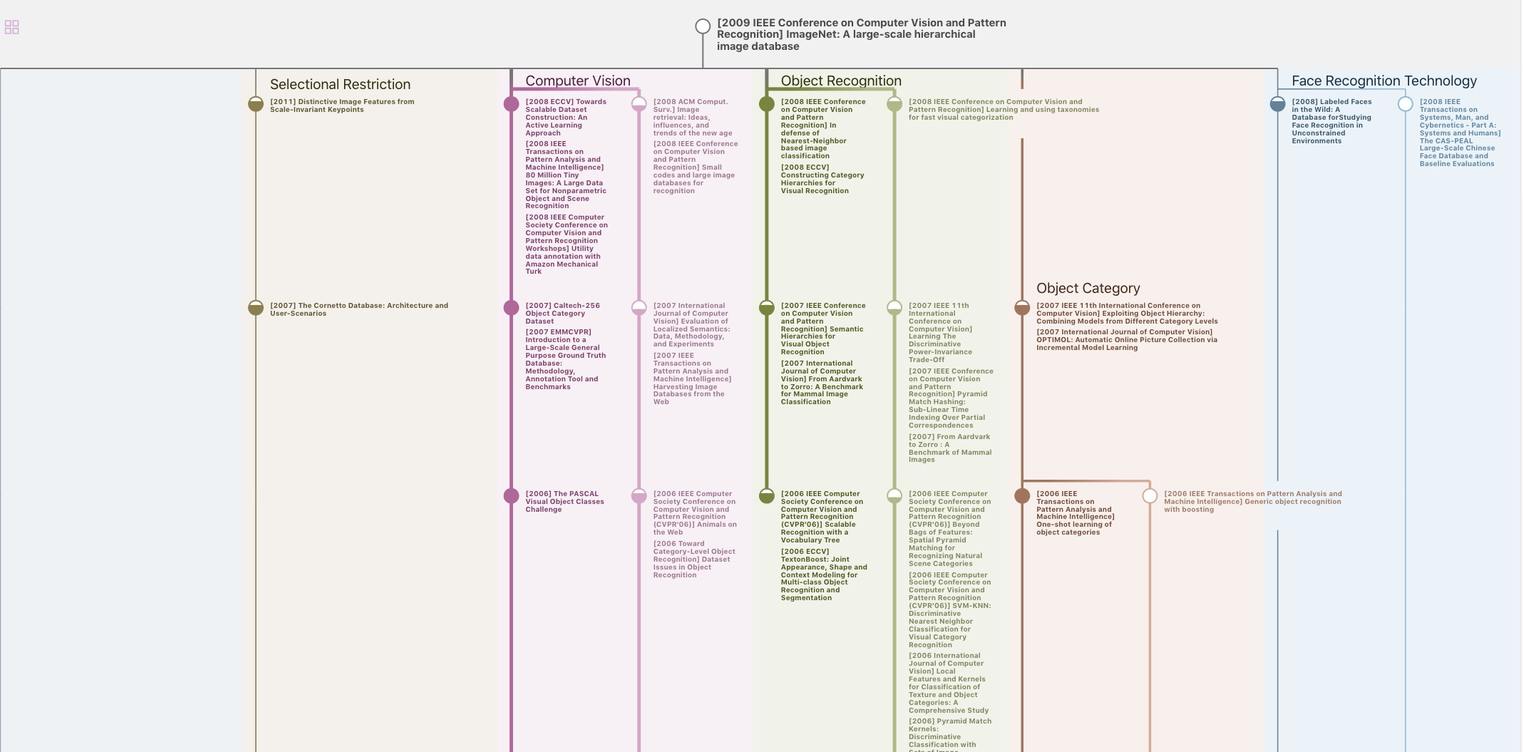
生成溯源树,研究论文发展脉络
Chat Paper
正在生成论文摘要