(Digital Presentation) Lithium Ion Battery Electrode Manufacturing Model Accounting for 3D Realistic Shapes of Active Material Particles: Exploring the Effect of Processing Parameters on Electrode Heterogeneity
ECS Meeting Abstracts(2022)
摘要
Nowadays, in face of the increasing need for lithium-ion batteries (LIBs), how to achieve higher energy densities while maintaining or reducing costs has been widely studied. In order to achieve optimization of the performance of batteries, it is essential to understand the influence of parameters at each stage of the LIBs manufacturing process on the architectures of the electrodes, which affects the energy, power, lifetime and safety of the LIB cells. The aim of our ARTISTIC project,1,2 funded by the ERC, is to develop a digital twin that enables predicting the electrode architectures and their electrochemical performances from parameters at each stage of the LIBs manufacturing process. Such digital twin is supported by a combination of multiscale modeling3-7 and machine learning (ML)8,9. In this work, we present our new work, which studies the manufacturing process of LiNi0.33Mn0.33Co0.33O2 (NMC111)-based cathodes (Figure 1). Our methodology encompasses coarse-grained molecular dynamics and discrete element method to simulate the different manufacturing stages, from the slurry, to the drying and the calendering of the resulting electrodes. In this new work, we account in our model for non-spherical NMC111 secondary particles with realistic 3D shapes obtained by X-ray micro-computational tomography (XCT), together with the spherical particles representing the carbon binder domain. The results are validated by comparing our predicted electrode architectures with the experimental ones. Our approach captures the changes in orientation of the secondary particles during the calendering process, as well as their possible deformation and cracking due to too high pressure. In addition, we discuss the changes in porosity, tortuosity factor, conductivity, different phases distribution and pore size distribution during the calendering process and compare them with the XCT results. The ARTISTIC Project website: www.erc-artistic.eu (accessed on April 2022). T. Lombardo, F. Caro, A. C. Ngandjong, J.-B. Hoock, M. Duquesnoy, J. C. Delepine, A. Ponchelet, S. Doison, and A. A. Franco, Batteries & Supercaps, 5, e202100324 (2022). T. Lombardo, J. Hoock, E. N. Primo, A. C. Ngandjong, M. Duquesnoy, and A. A. Franco, Batteries & Supercaps, 3, 721–730 (2020). T. Lombardo, A. C. Ngandjong, A. Belhcen, and A. A. Franco, Energy Storage Materials, 43, 337–347 (2021). A. C. Ngandjong, T. Lombardo, E. N. Primo, M. Chouchane, A. Shodiev, O. Arcelus, and A. A. Franco, Journal of Power Sources, 485, 229320 (2021). A. Shodiev, M. Chouchane, M. Gaberscek, O. Arcelus, J. Xu, H. Oularbi, J. Yu, J. Li, M. Morcrette, and A. A. Franco, Energy Storage Materials, 47, 462–471 (2022). M. Chouchane, A. Rucci, T. Lombardo, A. C. Ngandjong, and A. A. Franco, Journal of Power Sources, 444, 227285 (2019). M. Duquesnoy, T. Lombardo, M. Chouchane, E. N. Primo, and A. A. Franco, Journal of Power Sources, 480, 229103 (2020). R. P. Cunha, T. Lombardo, E. N. Primo, and A. A. Franco, Batteries & Supercaps, 3, 60–67 (2020). Figure 1
更多查看译文
AI 理解论文
溯源树
样例
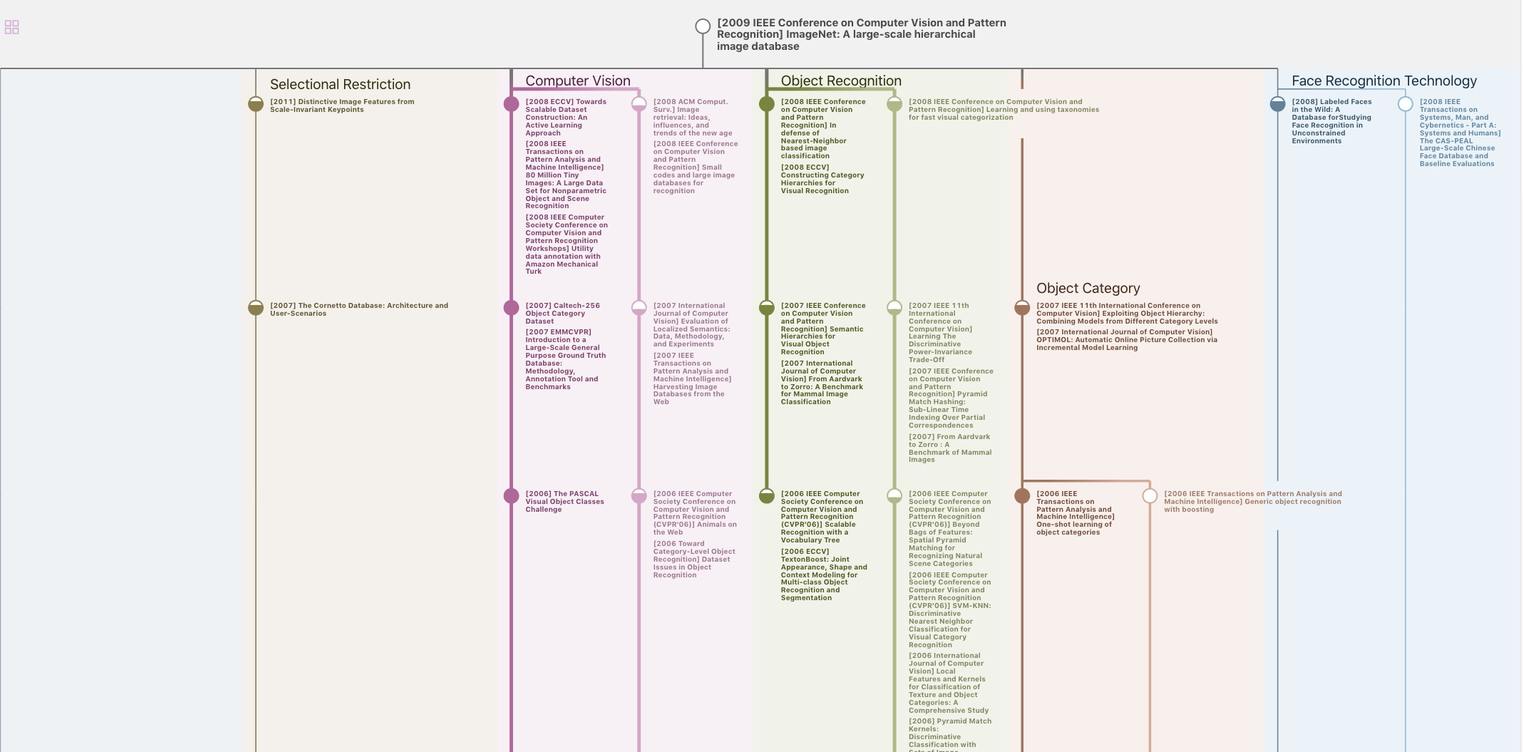
生成溯源树,研究论文发展脉络
Chat Paper
正在生成论文摘要