Features of wear of DLC-Si coating under microcontact conditions during the formation of secondary structures
COMPOSITE STRUCTURES(2023)
摘要
Diamond-Like Carbon (DLC) coatings have high wear resistance, hardness, biocompatibility and chemical inertness. Secondary structures, which formed at the track in dry friction conditions, provide friction reduction. Doping DLC with both metallic and non-metallic elements leads to a rearrangement of the structure of graphite clusters, a change in their properties, and facilitates the formation of secondary structures. In the present, the silicon atoms were used to create the compositional structure of DLC surface layers at the level of the crystal lattice. DLC-Si coatings with the thickness of 2 mu m were deposited on a (Cr, Al, Si)N layer with the thickness of 3 mu m formed on a steel substrate. DLC-Si layer was deposited by plasma-enhanced chemical vapor deposition using acetylene and tetramethylsilane. Nanoindentation in the wear mode was used to study the nanomechanical properties of the surface. Atomic force microscopy was used to visualize the surface morphology and wear traces. In this study, secondary structures were created in a microfriction process using a NanoScratch mode. The surface structures after microfriction was observed by atomic force microscopy, and the specific surface energy was measured. The specific volumetric wear rate of the coatings after microfriction was estimated. During microtribological testing with double squares the specific volumetric wear rate of DLC coatings was 5.39.10-14 m3/N.m for 0.8 % Si and 12.39.10-14 m3/N.m for 10 % Si. When tested in the form of scratches, the specific volumetric wear rate for the coating was for the DLC-0.8 % Si (1.22 - 10.71).10-14 m3/N.m and for the DLC-10 % (6.17 - 49.55) .10-14 m3/N.m.
更多查看译文
关键词
Si-doped DLC coatings,Microtribological testing,Microcontact,Secondary structures
AI 理解论文
溯源树
样例
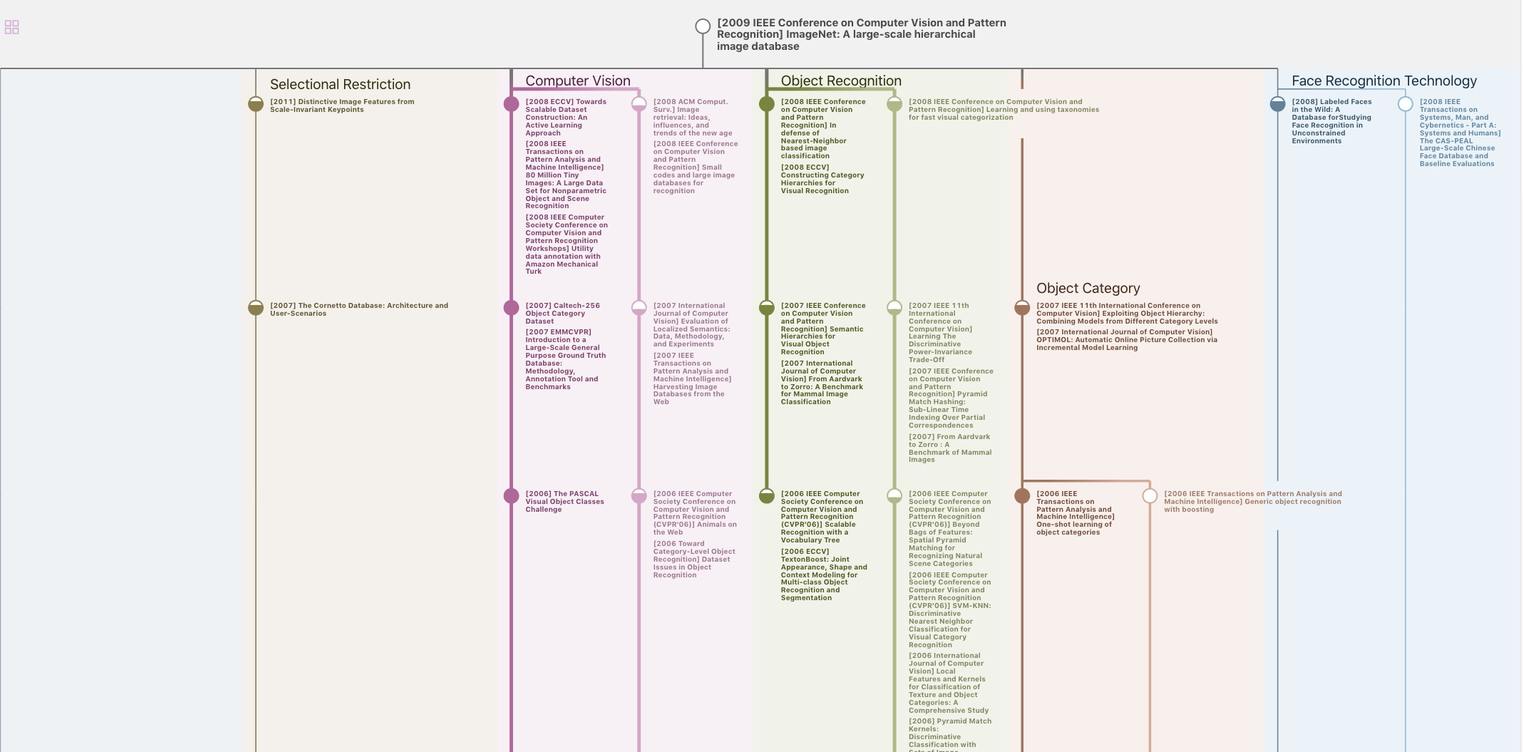
生成溯源树,研究论文发展脉络
Chat Paper
正在生成论文摘要