Ultra-precision time-controlled grinding for flat mechanical parts with weak stiffness
JOURNAL OF MANUFACTURING PROCESSES(2023)
摘要
High-precision flat mechanical parts are widely used, such as in aerostatic bearing, which requires a rather high machining precision. Due to large size, low stiffness and other machining problems, traditional ultra-precision grinding machine tool cannot directly achieve the final precision, so manual grinding is necessary to meet the manufacturing requirements, resulting in low efficiency. Based on the computer-controlled optical surfacing (CCOS) method and the flexible grinding process, the time-controlled grinding method (TCG) is proposed to achieve quantitative material removal at each position on the workpiece. Combined with the material removal mechanism, the removal function with good linearity and stability is extracted by controlling corresponding parameters. By applying a novel measuring and processing method of surface data with high precision and high efficiency, the flatness error and parallelism error are accurately obtained and used as grinding reference to carry out the time-controlled grinding experiment on one spacer ring with a diameter of 190 mm. The final flatness error converges from 1.5-2 mu m to 0.6-0.7 mu m and parallelism error converges from-2 mu m to-0.6 mu m, while the roughness converges from 273 nm Ra to 65 nm Ra, achieving the goal of ultra-precision digital machining of submicron level. The machining precision is better than traditional ultra-precision grinding machine tool, and the potential for time-controlled grinding method of ultra-precision machining in flat mechanical parts especially with low stiffness is verified.
更多查看译文
关键词
Time-controlled grinding,Abrasive belts,Flat mechanical parts,High precision measurement
AI 理解论文
溯源树
样例
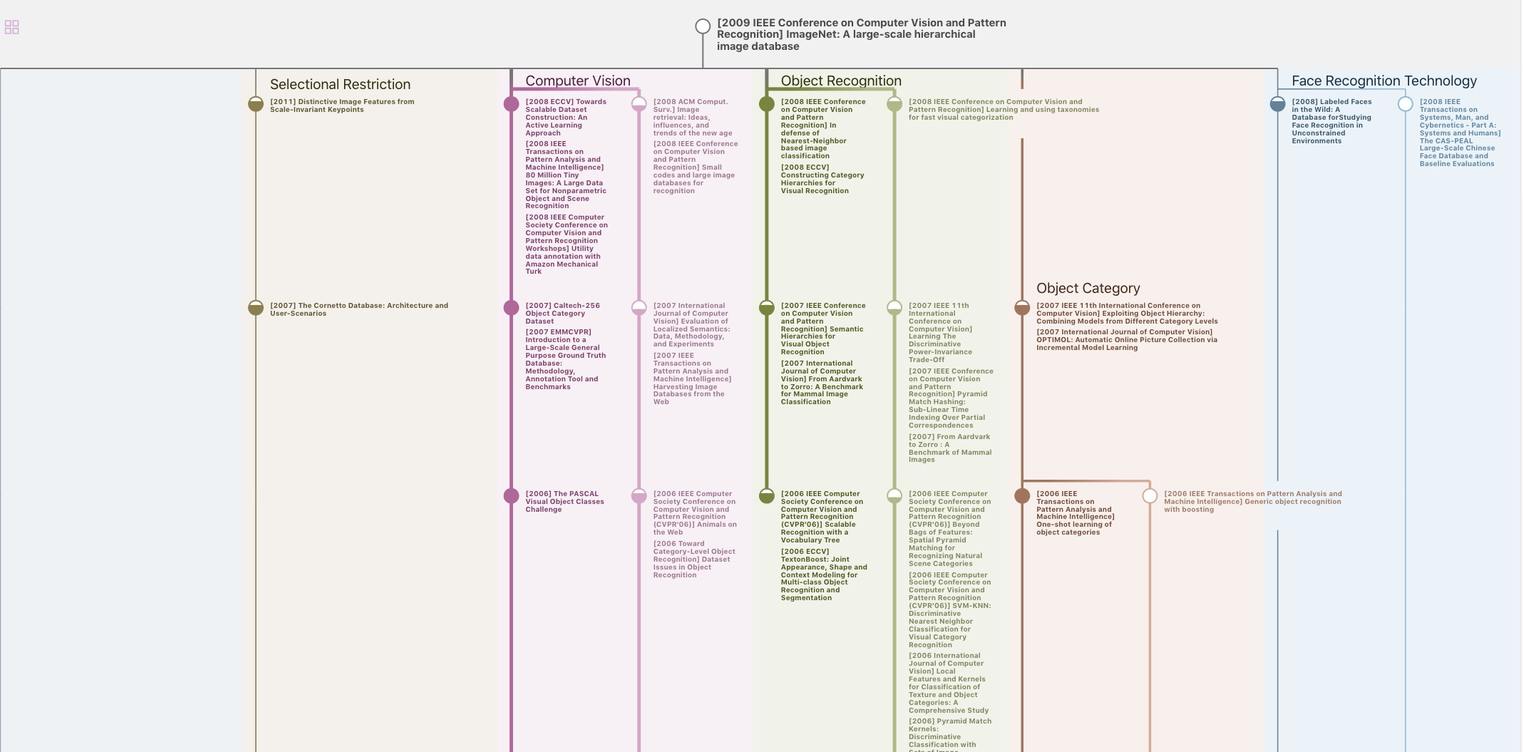
生成溯源树,研究论文发展脉络
Chat Paper
正在生成论文摘要