Tailoring microstructure with special bimodal structure to improve the ductility and fatigue life of laser powder bed fused Ti6Al4V alloy
Materials Science and Engineering: A(2023)
摘要
Achieving the high strength and ductility, as well as the excellent fatigue life, was the primary consideration for aerospace application of the additively manufactured (AM) titanium alloys, but it was limited to the high residual stress, huge columnar β grains arising from the severe directional heat flow and temperature gradient. To address these challenges and then improve the comprehensive mechanical properties, this work newly designed heat treatment schedules to tailor the microstructure to improve tensile/fatigue properties in the laser-powder bed fusion (L-PBF) of Ti6Al4V. The optimized schedule (920 °C/1 h/water cooling + 800 °C/2 h/furnace cooling) obtained the special bimodal structure, including the thin lamellar α+β phases (thickness of 1.8 μm) and the discontinuous equiaxed grain boundary α phases (GB-α) (diameter in ∼6 μm), achieving the good combination of tensile strength (1025 MPa) and ductility (17.2%). The heated-treated Ti6Al4V parts with thickness of 2∼10 mm exhibited the good stability of strength and eliminated the strength anisotropy. The dimensional effect of specimen resulted in the significant discrepancy in ductility. The tailored Ti6Al4V exhibited the superior low-cycle fatigue life equivalent to the wrought counterpart due to the refined α phases, whereas presenting the relatively low stability in the high cycle fatigue life. The fracture morphology showed the crack initiation and propagation resulting from the aligned pores and uncontrollable defects.
更多查看译文
关键词
laser powder bed,microstructure
AI 理解论文
溯源树
样例
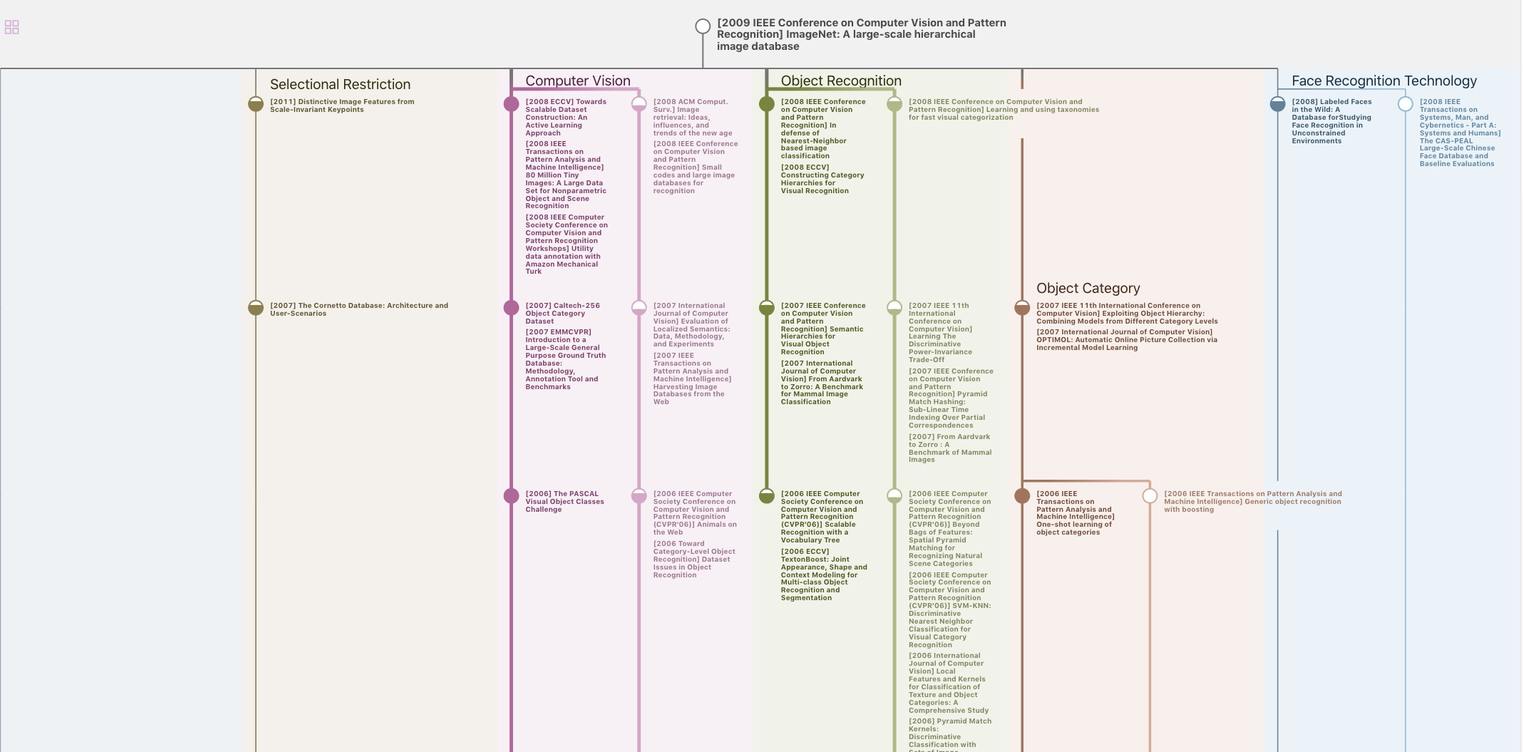
生成溯源树,研究论文发展脉络
Chat Paper
正在生成论文摘要