Influence of Divisional Size on Structural Quality of 316L Parts Printed by Selective Laser Melting
China Surface Engineering(2023)
摘要
Recently, laser additive manufacturing technology has become a research hotspot in engineering, manufacturing, materials, optics, and other disciplines. Namely, it provides a new technical approach for lightweight and structural integration design and manufacturing of complex structural metal components. Selective laser melting (SLM) uses a high-energy laser beam with a diameter of 20-100 & mu;m as the heat source to melt the metal powder and matrix surface below the powder by high-speed scanning and realizes layer-by-layer formation after cooling and solidification. Compared to other additive manufacturing technologies, SLM exhibits better forming accuracy, free forming, and a wide range of material selections. However, it is difficult to carry out the subsequent surface processing of complex structure precision metal parts manufactured by additive manufacturing, which puts higher requirements on the surface quality of SLM parts. The divisional scanning strategy can substantially enhance the surface quality of parts printed with SLM. This is because there is a large temperature gradient in the parts during the SLM forming process, which causes the expansion and contraction trends of each area in the parts to be inconsistent. This means the parts will produce large thermal stress in the forming process and exhibit a warping deformation trend. The influence of the scanning strategy on shape error and surface roughness is obtained by comparing the divisional scanning strategy with the conventional "S"-shaped scanning strategy. However, the effect of the divisional scanning size on the surface quality of printed parts is still unclear, and the undulation morphology between the divisions under the divisional scanning strategy has not been analyzed. To improve the surface quality and dimensional accuracy of cantilever structures by SLM, taking a square overhanging structure with support as the research object, a set of samples with the same specifications was designed, and the size of the samples was 25 mm x 25 mm. All the samples were added to the same support structure. The "S" shape laser scanning strategy with a reentrant width of 5 mm and the partitioned laser scanning strategy with different partition sizes (1.2, 3.6, 9.6, and 13.2 mm) were used for the samples. Using ABAQUS finite element software as the analysis tool, a numerical simulation of the SLM forming process was carried out using the thermal-mechanical coupling analysis method. The surface structure with three different wave distances, namely shape error, waviness, and surface roughness, were studied by combining numerical simulations and experiments. The profile data of the entire upper surface of the sample were obtained using confocal microscopy. The structural quality of square overhanging parts with supports was evaluated based on geometry errors, waviness, and surface roughness. The results showed that the variation trends of the geometry error, waviness, and surface roughness concerning the divisional size were different. The warpage height of the surface edge of the parts gradually decreased as the divisional size decreased. The width of the single-channel molten pool in the division gradually increased and the convexity gradually decreased. The contour fluctuation between the adjacent divisional zones gradually increased. The cross-sectional geometry error and surface roughness of the printed parts were reduced, but the waviness increased with decreasing divisional size. The surface quality of the printed parts first improved and then decreased. The increase in waviness with decreasing divisional size could be attributed to heat accumulation if the divisional size is too small. Improving the surface quality by decreasing the laser energy input by tuning the divisional size would provide a theoretical foundation for optimizing the surface quality and dimensional accuracy of cantilever structures using SLM.
更多查看译文
关键词
selective laser melting,divisional size,geometry error,waviness,roughness
AI 理解论文
溯源树
样例
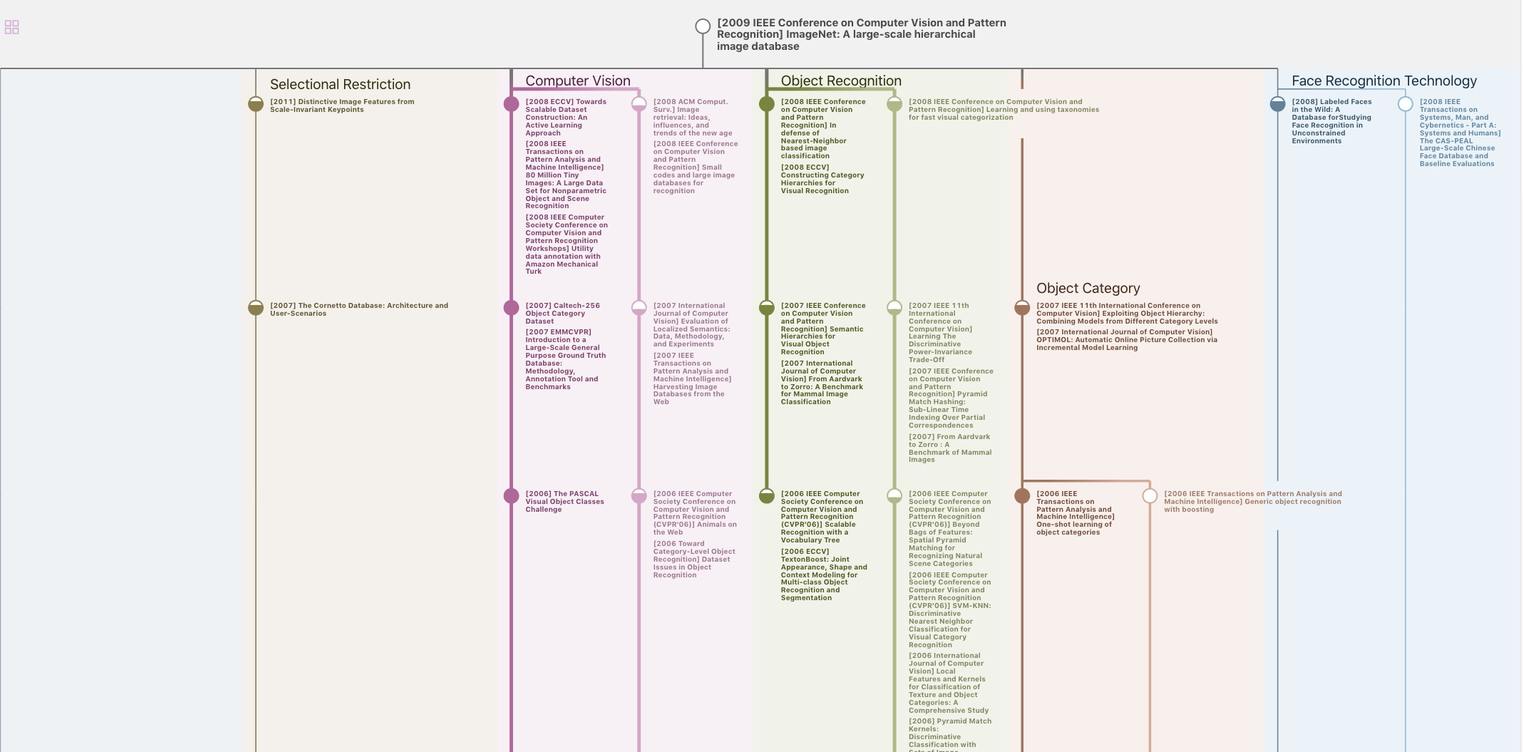
生成溯源树,研究论文发展脉络
Chat Paper
正在生成论文摘要