A two-module automated scanning inspection planning methodology for hole features on image measuring instrument
INTERNATIONAL JOURNAL OF ADVANCED MANUFACTURING TECHNOLOGY(2023)
摘要
Quality inspection of the holes is commonly indispensable, as the resulting geometrical errors severely affect the functionality and assembly of the parts. Until now, most machine vision systems have employed a single-camera to obtain the entire contour of an object, but it is of great challenge to ensure high accuracy. This paper proposes a new path-planning strategy in two steps: local path planning (LPP) and global path optimization (GPO). Instead of using a single-camera to acquire the complete contour of a single hole, the moving measurement captures multiple continuous and non-repetitive local contours, improving the resolution of the measured contours. To ensure that the imaging probe avoids interfering with the workpiece during the motion, a dynamic collision detection is used to generate a collision-free path. For multi-hole measurements, a shortest collision-free path algorithm (SCFPA) is proposed to transform the traversal problem of multiple features into a generalized traveling salesman problem (GTSP) and obtain the shortest collision-free path by substituting the collision-free distance into the improved simulated annealing algorithm (ISA). To conduct measurements more accurately and reduce the uncertainty caused by geometric errors, a geometric error model was established, and the nine-line method was utilized to identify error terms. The experimental results show that the proposed measurement method can not only reconstruct the whole 2D hole profile with high-precision but also effectively minimize the inspection path, ensuring the safety of the working process.
更多查看译文
关键词
2D hole contour reconstruction,21 geometric error,Image measuring instrument,GTSP,Simulated annealing
AI 理解论文
溯源树
样例
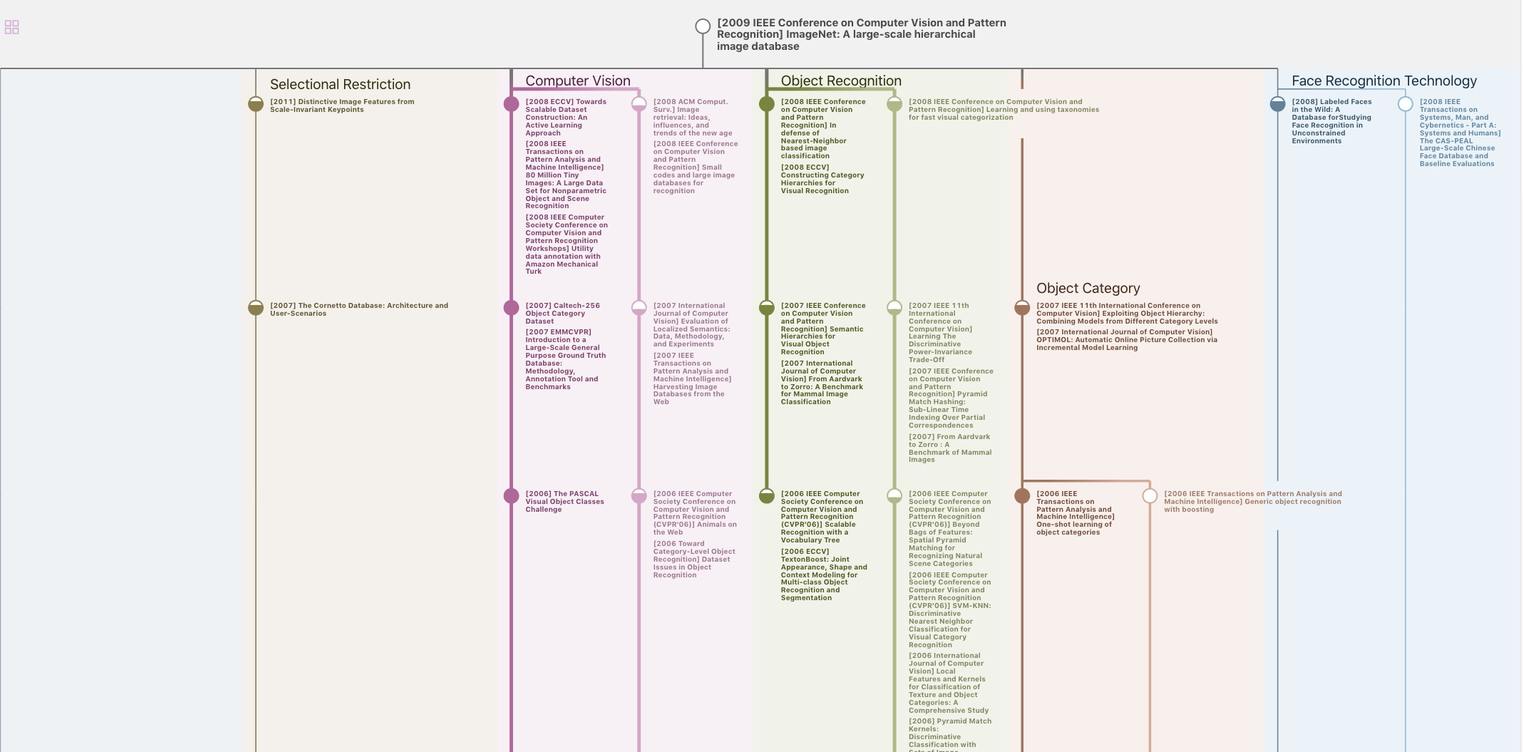
生成溯源树,研究论文发展脉络
Chat Paper
正在生成论文摘要