A Novel Biomedical Ti–35Nb–15Zr (At. Pct) Alloy In Situ Fabricated by Laser Powder Bed Fusion: Processing Window, Microstructure, and Mechanical Properties
METALLURGICAL AND MATERIALS TRANSACTIONS A-PHYSICAL METALLURGY AND MATERIALS SCIENCE(2023)
摘要
Commercial load-bearing implant applications have detrimental stress-shielding effects. In this study, the molybdenum equivalence (Mo eq ) and molecular orbital methods were used in the composition design of low modulus Ti–35Nb–15Zr (at. pct) alloys. Based on Taguchi’s experimental design, the relationship between the process parameters (laser power, scanning speed, hatch spacing) and the performance (surface quality, porosity, and mechanical properties) of the sample fabricated by LPBF with a small spot diameter (30 μ m) was studied. The use of EL is more effective in determining the process window. A surface roughness below 3 µ m, porosity of less than 1 pct, and hardness of up to 391 HV of the samples were obtained at a laser power of 250 to 300 W, scanning speed of 400 to 600 mm/s, and hatch spacing of 35 µ m. Ti–35Nb–15Zr (at. pct) alloys with Young’s modulus of 72.82 ± 0.77 GPa and yield strength of 1185.18 ± 41.79 MPa were obtained at a laser power of 250 W, and the values of both increased with the increasing laser power. The intensity of the β texture was also revealed to be related to the hatch spacing. As the hatch spacing increases, the intensity of β -texture decreases from 4.87 to 1.83 times from H35 to H60. Additionally, the correlations between process parameters and resultant properties were defined in study. The scan speed showed the highest correlation with surface roughness, porosity, and hardness, while the hatch spacing mainly affected surface roughness and hardness. Laser power had decreasing effects on porosity, surface roughness, and hardness in that order.
更多查看译文
关键词
laser powder bed fusion,alloy,pct
AI 理解论文
溯源树
样例
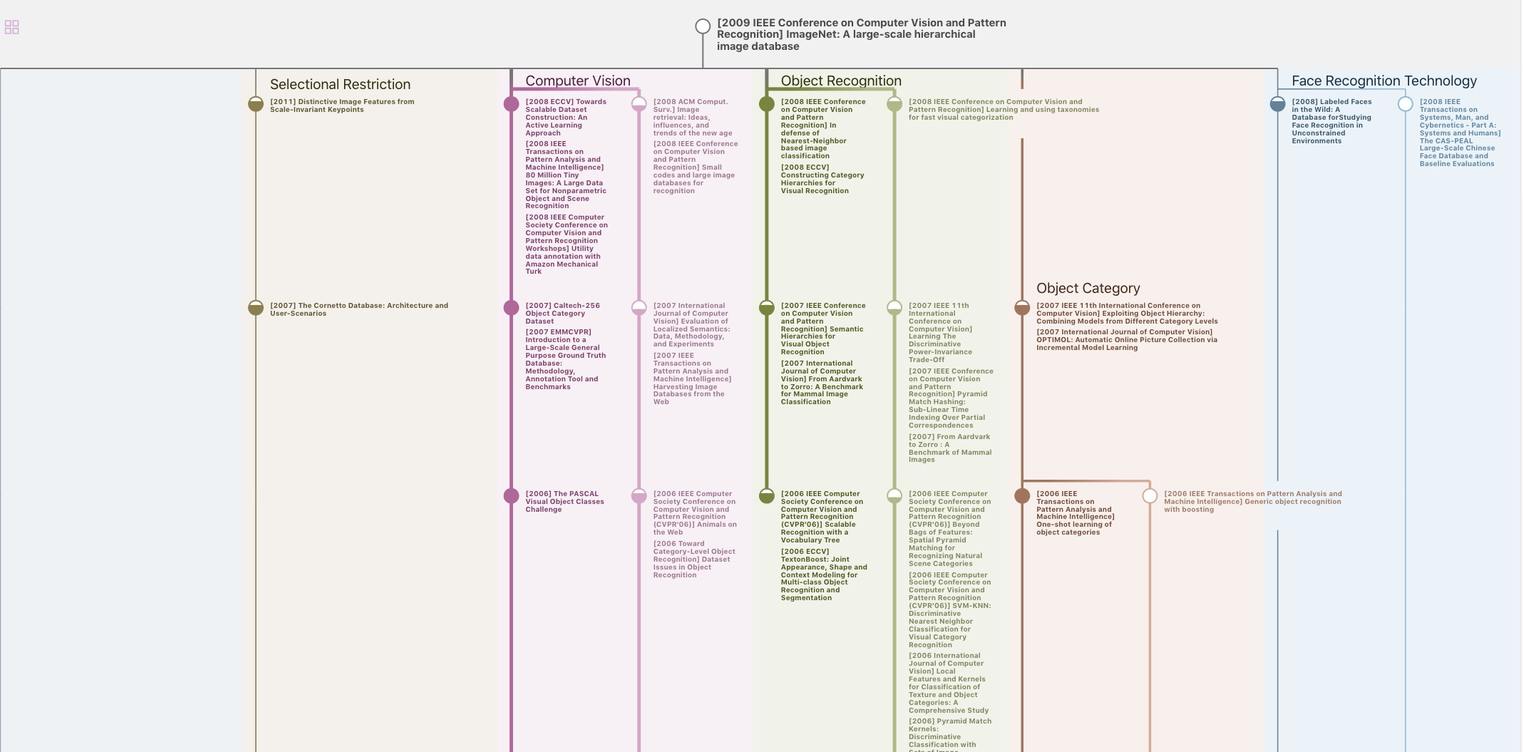
生成溯源树,研究论文发展脉络
Chat Paper
正在生成论文摘要