FPGA-Based Methodology for Detecting Positional Accuracy Degradation in Industrial Robots
Applied sciences(2023)
摘要
Industrial processes involving manipulator robots require accurate positioning and orienting for high-quality results. Any decrease in positional accuracy can result in resource wastage. Machine learning methodologies have been proposed to analyze failures and wear in electronic and mechanical components, affecting positional accuracy. These methods are typically implemented in software for offline analysis. In this regard, this work proposes a methodology for detecting a positional deviation in the robot's joints and its implementation in a digital system of proprietary design based on a field-programmable gate array (FPGA) equipped with several developed intellectual property cores (IPcores). The method implemented in FPGA consists of the analysis of current signals from a UR5 robot using discrete wavelet transform (DWT), statistical indicators, and a neural network classifier. IPcores are developed and tested with synthetic current signals, and their effectiveness is validated using a real robot dataset. The results show that the system can classify the synthetic robot signals for joints two and three with 97% accuracy and the real robot signals for joints five and six with 100% accuracy. This system aims to be a high-speed reconfigurable tool to help detect robot precision degradation and implement timely maintenance strategies.
更多查看译文
关键词
FPGA,positional accuracy,discrete wavelet transform,industrial robot,degradation,neural networks
AI 理解论文
溯源树
样例
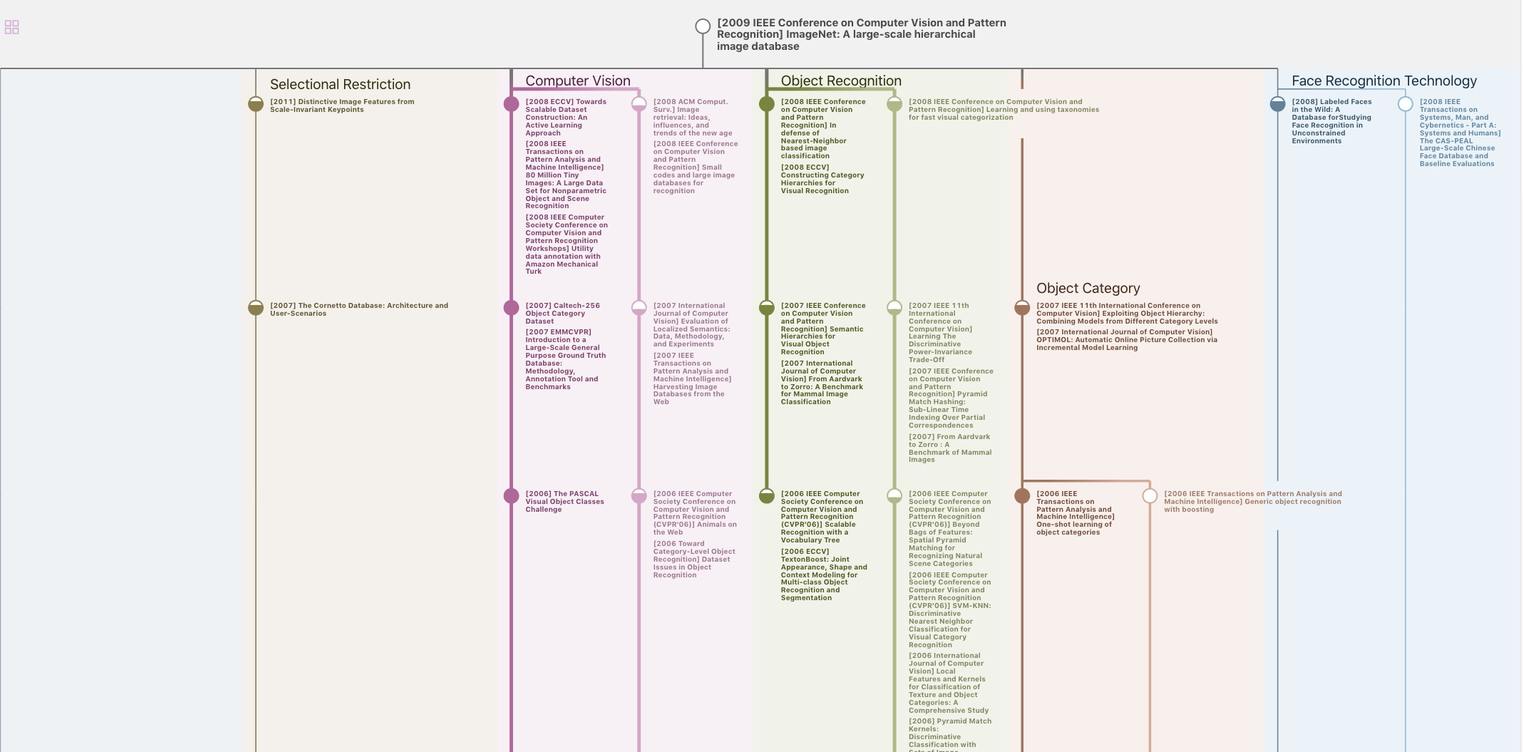
生成溯源树,研究论文发展脉络
Chat Paper
正在生成论文摘要