Facile and flexible fabrication of structured array surfaces on binderless tungsten carbide by using electrical discharge machining with a novel self-assembly ball electrode
JOURNAL OF THE AMERICAN CERAMIC SOCIETY(2023)
摘要
Electrical discharge machining (EDM) method is an innovative method for the fabrication of structured array surfaces on binderless tungsten carbide (WC) which is a typical embossing mold material, compared to traditional machining methods. To improve the convenience of electrode replacement and the fabrication efficiency of the structured array, a novel self-assembly ball electrode is innovatively developed. The feasibility of machining binderless WC with a self-assembly ball electrode was studied and its effect on profile deviation analyzed. Furthermore, the discharge condition's effect on surface roughness, material removal rate (MRR), and tool wear ratio (TWR) was investigated. The microstructure, phase structure, and element distribution of binderless WC caused by EDM were characterized by Raman spectroscopy, scanning electron microscopy, and energy dispersive x-ray spectroscopy. The results indicated that the maximum profile deviation of the different random structured arrays was about 3.7 & mu;m. The surface roughness of all structured arrays was below 1 & mu;m. The maximum TWR was about 0.008 mm(3)/min. Besides, the binderless WC surface after EDM presented strong D and G carbon peaks, which means the precipitation and transformation of the WC phase during the discharge process. Finally, different kinds of self-assembly ball electrodes are developed and used to fabricate the lens array structures on binderless WC. The fast fabrication of the micro-lens array surfaces in different arrangements sheds some light on the design and manufacturing of other functional structured surfaces.
更多查看译文
关键词
flexible fabrication,tungsten,structured array surfaces,machining,carbide
AI 理解论文
溯源树
样例
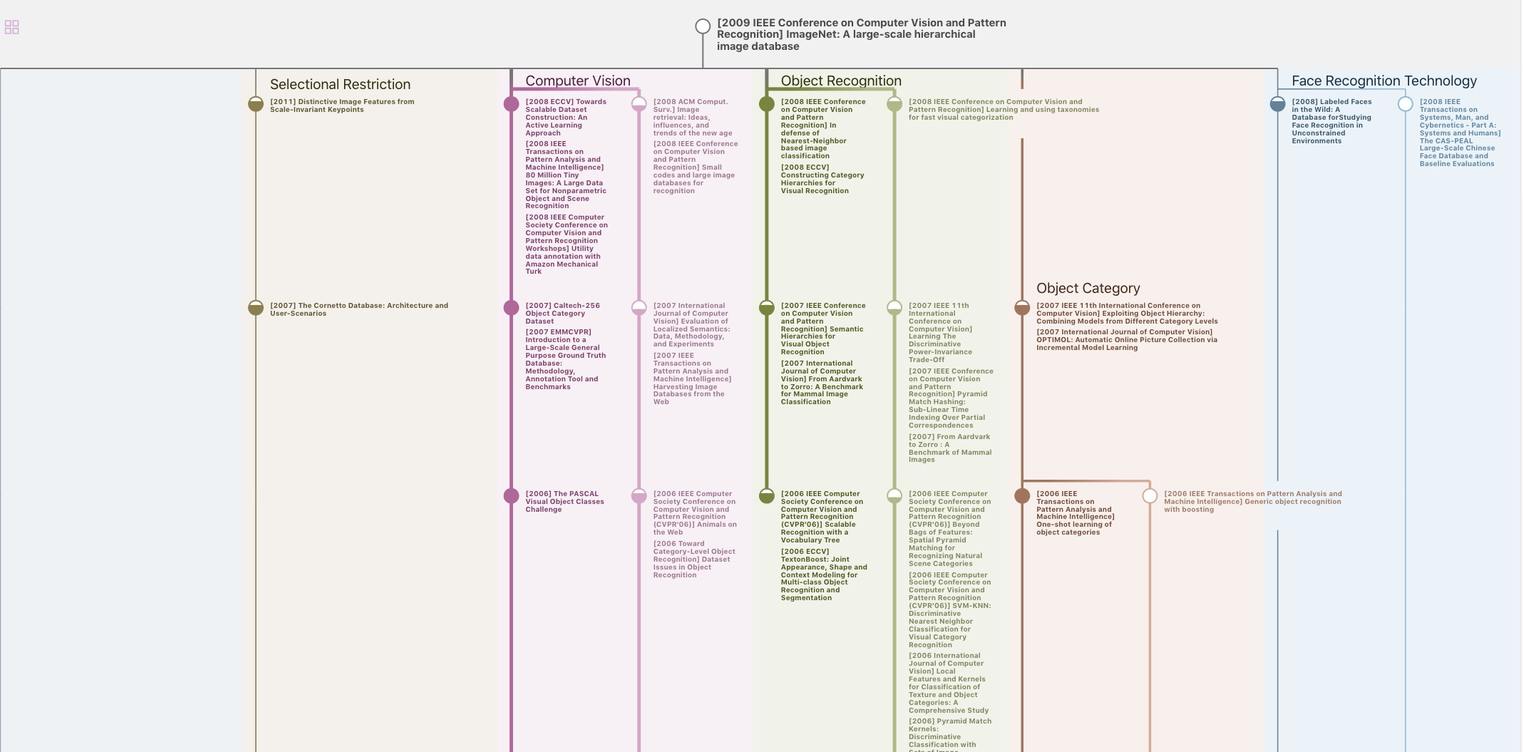
生成溯源树,研究论文发展脉络
Chat Paper
正在生成论文摘要