Correlation between filament deposition path, microstructural and mechanical properties of dense alumina parts printed by robocasting
JOURNAL OF THE EUROPEAN CERAMIC SOCIETY(2024)
摘要
Robocasting is an extrusion-based additive manufacturing (AM) process widely used to produce porous structures. It enables to build three-dimensional (3D) ceramic parts, thanks to computer numerical control of the filament deposition path onto a fabrication substrate. Despite its high potential, robocasting is much less explored than other AM techniques for producing dense parts. This work focused on the robocasting of dense alumina parts by varying the filament deposition path of an environmentally friendly paste. Taguchi method was used to establish a correlation between the printing parameters and the microstructural and mechanical properties of the sintered parts. Closed pores located between adjacent filaments were found to dictate crack propagation mechanisms, depending on the infill pattern. The optimal printing strategy led to 93% dense alumina samples having a flexural strength of 140 MPa, a Young's modulus of 355 GPa and a Poisson's ratio of 0.23.
更多查看译文
关键词
Printing parameters,Additive manufacturing,Porosity,Young 's modulus,Flexural strength
AI 理解论文
溯源树
样例
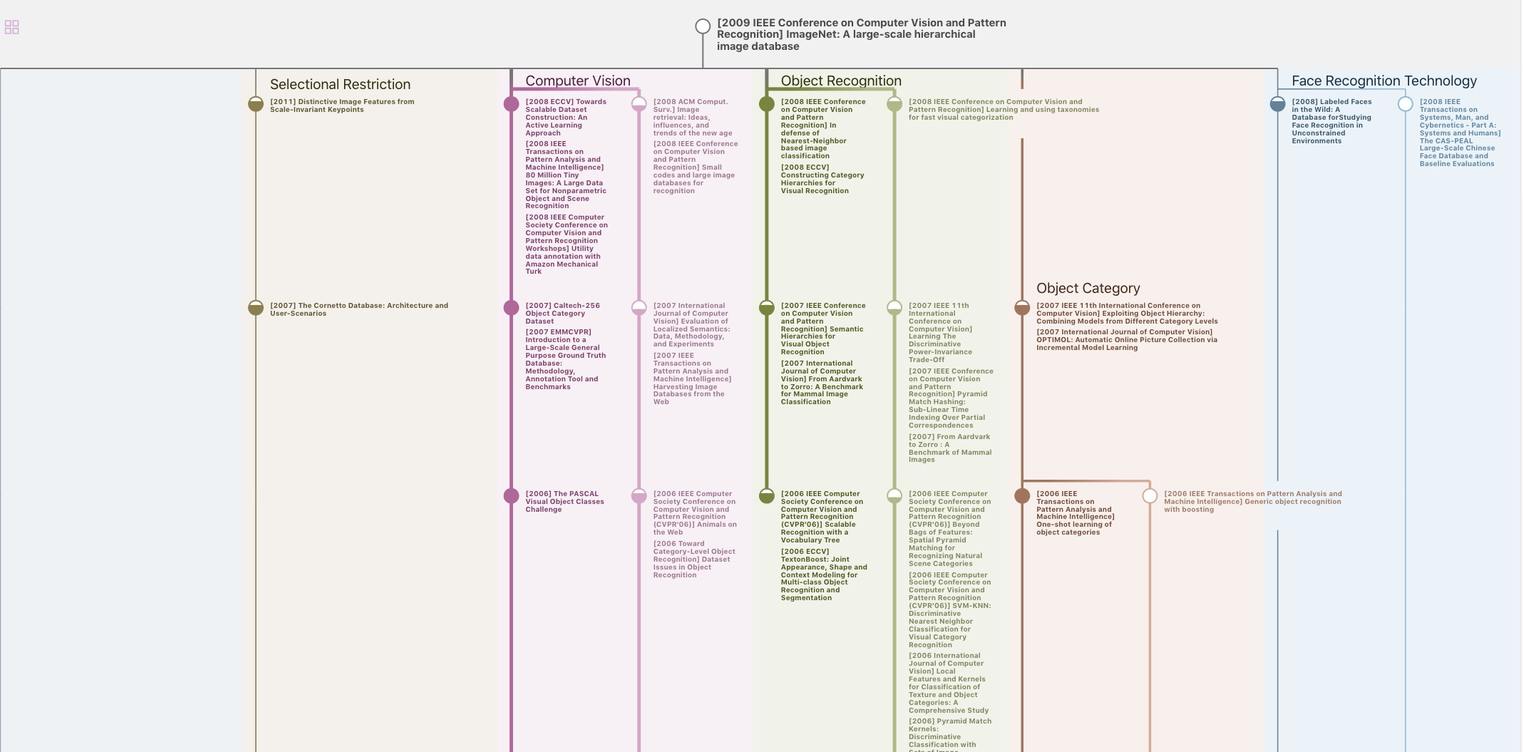
生成溯源树,研究论文发展脉络
Chat Paper
正在生成论文摘要