Influence of Grease Containing Mineral Particles on Friction and Wear Characteristics Between Spiral Wires Inside Wire Rope
Wear(2023)
摘要
The mine shaft environment is filled with mineral particles and these suspended particles exacerbate the wear behaviour between the wires in wire rope, seriously threatening the safety of mining. In this study, to investigate the influence of mixing mineral (ore, coal) particles of different concentrations and particle sizes in grease on the fretting behaviour between spiral-contacting wires, experiments were carried out on a selfmade test device. The results show that the addition of mineral particles increases the coefficient of friction (COF) and cumulative dissipation energy between steel wires. When the ore particles with a concentration of 15% and a size of 0.048-0.062 mm were added to the grease, the COF between the steel wires reached a maximum of about 0.234. In addition, with the increase of mineral particle concentration and the decrease of particle size, the wear depth, wear amount and specific wear rate of steel wire increase accordingly. Among them, the wear depth, wear amount and specific wear rate reach the maximum after adding ore particles with a concentration of 15% and a size of 0.048-0.062 mm, which are about 30.5 & mu;m, 6706 x 103 & mu;m3, and 2.31 x 10-6 mm3/Nm, respectively. Furthermore, many cutting furrows and crushing pits are added to the wear morphology of steel wire after adding ore particles. The main wear mechanism is severe abrasive wear and fatigue wear. After adding coal particles, the main wear morphology of steel wires is material transfer (attachment of coal particles) and exfoliation, and the main wear mechanism is adhesive wear, fatigue wear and slight abrasive wear.
更多查看译文
关键词
Mineral particles,Steel wire,Friction and wear,Wear mechanism
AI 理解论文
溯源树
样例
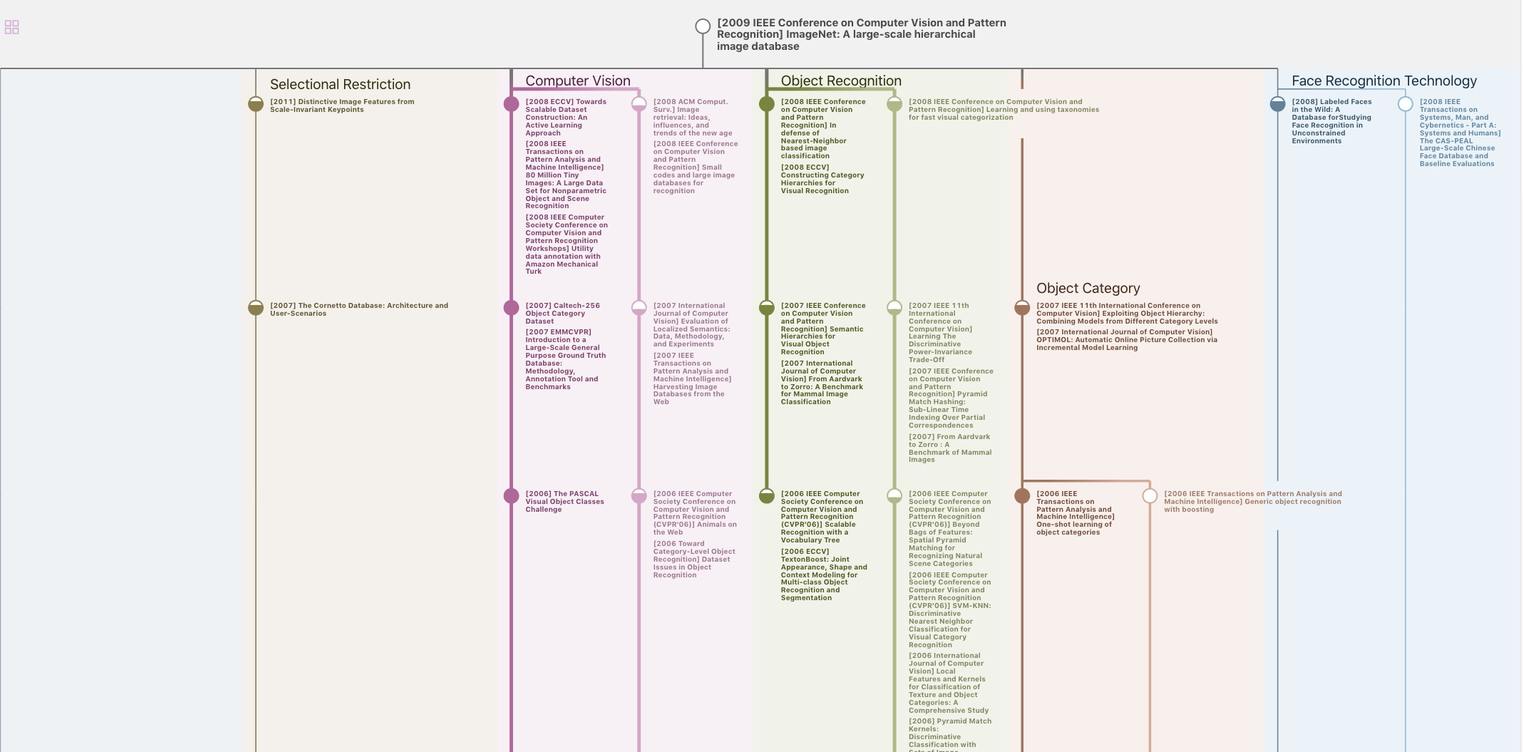
生成溯源树,研究论文发展脉络
Chat Paper
正在生成论文摘要