Optical Fiber Pressure Sensor Based on Sapphire Wafers Processed by Femtosecond Laser
ACTA OPTICA SINICA(2023)
摘要
Objective Pressure monitoring in high-temperature environments is necessary for aerospace, chemical smelting, and petroleum power. Optical fiber sensors can be applied in the measurement of various parameters under high-temperature and harsh environment due to their advantages of passivity, anti-electromagnetic interference, high-temperature resistance, and compactness. The optimal technical approach for pressure measurement is the optical fiber extrinsic FabryPerot interferometer (EFPI), which includes two typical structures of diaphragm- based type and diaphragm-free type. The principle of the diaphragm- free type is that as the refractive index of the gas in the open cavity changes linearly with the ambient pressure, diaphragm-free optical fiber pressure sensors can only measure the gas pressure, and its sensitivity is greatly affected by temperature. The diaphragm-type optical fiber EFPI pressure sensor based on different materials has been widely employed in pressure measurement. The working temperature of the sensor is mainly determined by the material of pressure sensing films. For example, the EFPI pressure sensor based on silicon dioxide is limited by the softening of the glass diaphragm at high temperature, and the working temperature for a long time is generally lower than 800 degrees C. With a melting point of 2045 degrees C and a wide transmission spectral range, sapphire is an ideal material for developing ultra- high temperature optical fiber sensors. To measure pressure in high- temperature and harsh environment, we propose and experimentally demonstrate a sapphire Fabry-Perot (F-P) interferometer with high temperature and large pressure range. The sensor is fabricated by direct bonding of three-layer sapphire wafers, including the sapphire substrate, the sapphire wafer with a through hole, and pressure-sensitive sapphire wafer. Methods Firstly, a femtosecond laser is adopted to slice the sapphire wafer. The sapphire wafer is fixed on the sixdimensional micro- motion platform, and the laser power is adjusted to 30 mW through the attenuator. The laser beam is vertically focused on the surface of the sapphire wafer through a plano-convex lens with a focal length of 100 mm. The laser is scanned on the sapphire wafer at 5 mm intervals by controlling the six-dimensional micro-motion platform. Secondly, a through hole is inscribed on a sapphire wafer with a thickness of 175 mu m. The laser power is adjusted to 5 mW, and the laser beam is focused by a 20x objective lens. The laser scans in the center of the sapphire wafer until the inner wafer falls off automatically. Thirdly, the outer surface of the sapphire diaphragm is roughened. The laser power is adjusted to 1 mW to roughen the diaphragm without changing the thickness of the diaphragm as much as possible. The laser scans the surface by line- by- line method with a spacing of 50 mu m. Finally, to improve the stability of the sensor at high temperature and high pressure, the direct bonding process of sapphire wafers is designed. After RCA cleaning, sapphire wafers are immersed in 85% ( mass fraction) H3PO4 solution to remove residual oxides on the surface. Then wafers are immersed in a H2SO4 diluted solution to deposit a hydrophilic layer. The wafer pair is successfully bonded after being kept at 1300 degrees C for 20 h and pressure test systems are set up to investigate the pressure response of the proposed sensor. Results and Discussions The EFPI interference signal collected by the white light interference demodulator with a center wavelength of 1550 nm is shown in Fig. 4(a), and its frequency spectrum is shown in Fig. 4(b). The reflection spectrum is formed by three- beam interference. The second peak is the F-P signal formed by two surfaces ( R1, R2) of the sapphire substrate, which is utilized to measure the temperature. The third peak is the F-P signal formed by the front surface of the sapphire substrate and the front surface of the pressure-sensing sapphire diaphragm (R1, R3), which is leveraged to measure the pressure. The main frequency signal is extracted by the Gaussian window function, and the interference signals of the two cavities are obtained by inverse Fourier transform. The optical cavity length can be calculated by demodulating the phase information of the interference signal. The ultra- high pressure test shows that the pressure sensitivity of the sensor is 0. 1253 mu m/MPa within the pressure range of 0- 30 MPa, and the sensor has no leakage at 45 MPa. As the temperature increases, the sensitivity of the sensor increases slightly, reaching 0. 1322 mu m/ MPa at 700 degrees C. Figure 9 shows that the measurement resolution of the optical cavity length is about 1. 5 nm. Combined with the pressure sensitivity of the sensor at room temperature, the pressure resolution of the ultra-high pressure measuring system is 12 kPa, and the relative resolution is 0. 04% FS ( full scale). Conclusions In this study, an optical fiber pressure sensor based on sapphire wafers processed by femtosecond laser is proposed. Sapphire wafers with through holes and rough sapphire pressure- sensitive wafers are fabricated by femtosecond laser micromachining. The experimental results show that the sensor can measure the pressure within the temperature range of 25- 700 degrees C and the wide pressure range of 0-30 MPa, and the sensor does not break and leak under the ultra-high pressure of 45 MPa. The sensor is resistant to ultra- high pressure, high temperature, and intrinsic safety, which can solve the technical problems of pressure in- situ testing in the harsh environment of high temperature and high pressure.
更多查看译文
关键词
fiber optics,optical fiber pressure sensors,extrinsic Fabry,Perot interferometer,sapphire wafer,femtosecond laser micromachining,large pressure range
AI 理解论文
溯源树
样例
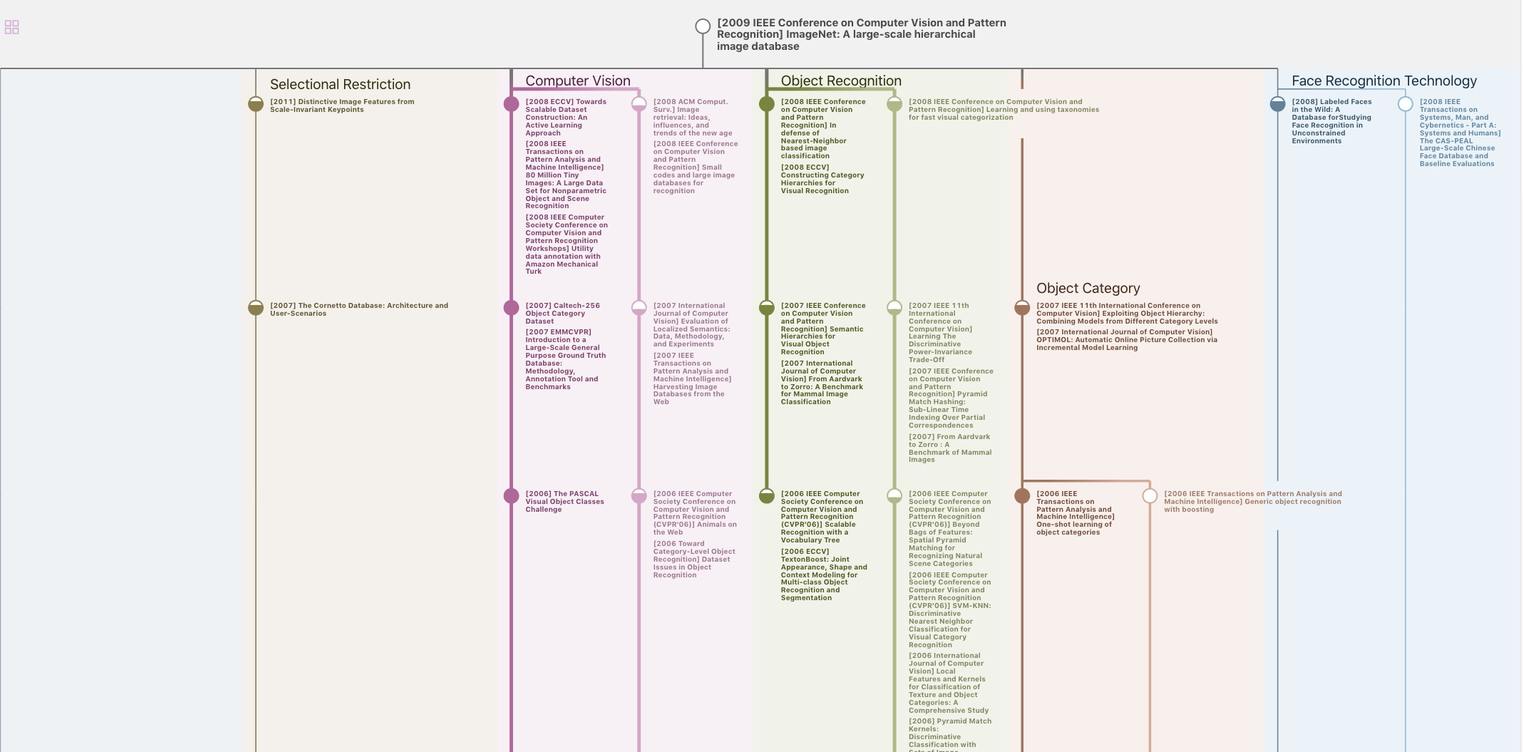
生成溯源树,研究论文发展脉络
Chat Paper
正在生成论文摘要