Enhancement of cooling performance in MEMS by modifying 3D packaging structure: A design, integration, analysis and test study
APPLIED THERMAL ENGINEERING(2024)
摘要
The heat dissipation of three-dimensional (3D) integrated Micro-Electro-Mechanical Systems (MEMS) has garnered considerable attention in scientific research and electronic applications in recent years. As power demands increase, device sizes decrease, and energy consumption is limited, the use of liquid and forced air cooling techniques is diminishing. In light of the growing emphasis on achieving carbon neutrality, there is renewed interest in passive cooling methods, which present a new imperative for environmentally-friendly thermal management of chips in the field of green energy. While the concept of designing thermal paths to mitigate heat in chips is not novel, it has become increasingly important due to the rapid accumulation of heat, reduction in chip volume, and the need to minimize energy consumption and carbon emissions. Consequently, the implementation of appropriate cooling structures within the available space of the chips has emerged as an appealing approach to enhance passive cooling. In order to tackle this challenge, four cooling structures, namely embedding network structure, overlaying extension platform, overlaying micro-pillar array, and overlaying surface microstructures, have been employed in the packaging process to augment the passive cooling capabilities of the chips. In this study, a 3D packaging model is developed to analyze the thermal characteristics of MEMS under the influence of power, TSV voltage, and heat source area using the finite element method. Additionally, the cooling structures are optimized based on the cooling performance analysis, taking into account the self-remaining space within the system and the heat source area factor. The application of four different cooling structures in 3D MEMS leads to enhanced cooling performance. In the event that liquid cooling and forced air cooling are not utilized, the system experiences a decrease in maximum temperature by 3.66 K, resulting in a corresponding decrease in temperature difference by 43.79 %. These reductions significantly contribute to the mitigation of thermal deformation and stress in MEMS, thereby enhancing the thermal reliability of the system. To verify the accuracy of the thermal simulation, a thermal test is conducted on the embedded network structure under simulated conditions. The thermal simulation, which has been validated through thermal testing, indicates that the implementation of four cooling structures within the self-contained area of MEMS has a notable effect on reducing temperature. This finding holds promise for its potential application in 3D MEMS.
更多查看译文
关键词
MEMS,3D integration,Packaging,Cooling structure,Cooling performance
AI 理解论文
溯源树
样例
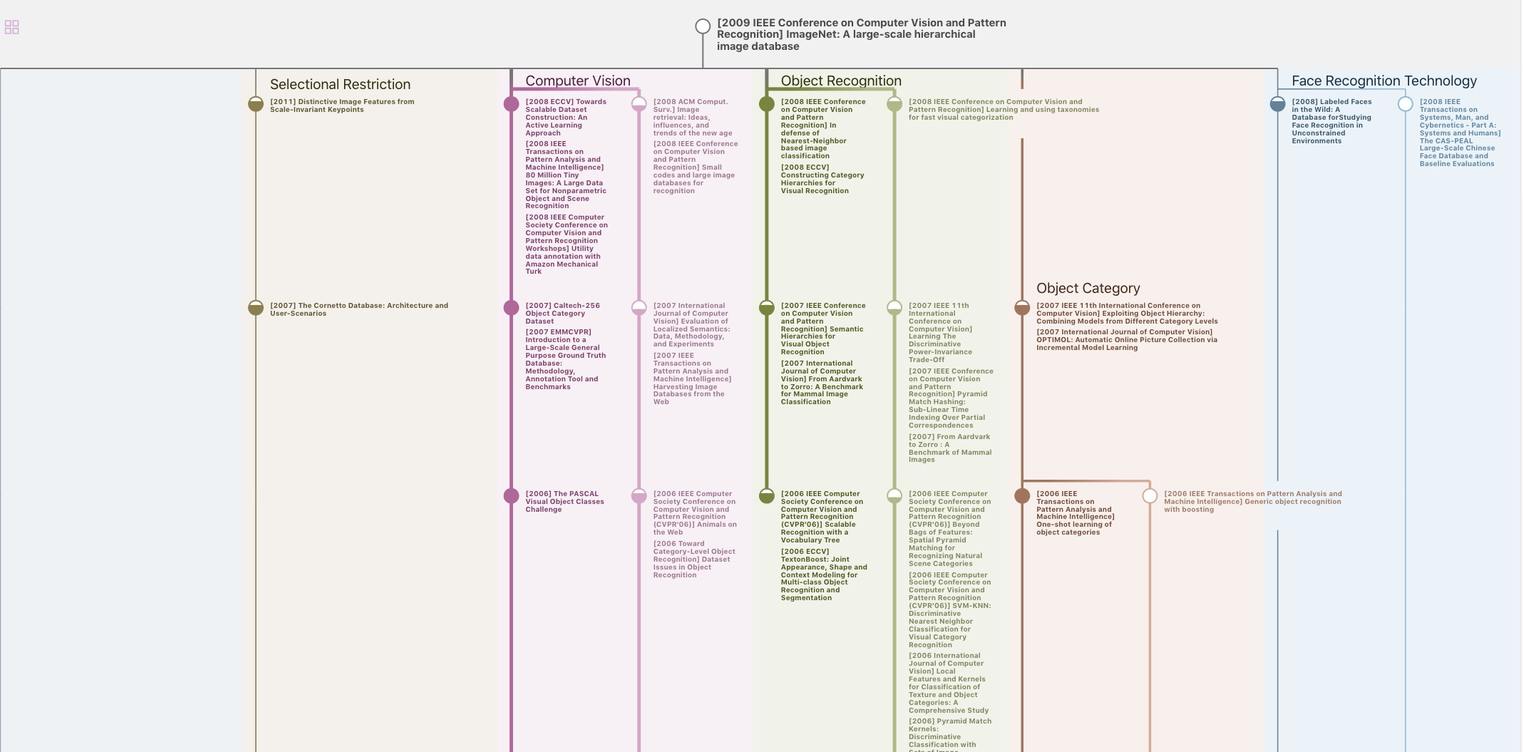
生成溯源树,研究论文发展脉络
Chat Paper
正在生成论文摘要