Modelling and Analysis of Dynamic Servo Error of Heavy Vertical Machining Centre Considering Nonlinear Factors
Processes(2023)
摘要
The dynamic servo error of heavy-duty vertical machining centres is one of the decisive factors affecting the machining accuracy of large and complex parts. Due to the characteristics of large mass, large load, and the large travel distance of the machine tool, non-linear factors such as friction, backlash, and lateral shift are more likely to cause unstable behaviours such as stick-slip and oscillation of the servo feed system of the machine tool, and reduce the performance and servo accuracy of the motion axis. In this paper, to consider the influence of non-linear factors such as friction, backlash, and lateral shift, an appropriately simplified representation of the mechanical transmission system of the ball screw has been used. According to the control structure of the Siemens 840D numerical control system, a theoretical model of the servo feed system for the heavy-duty vertical machining centre was established based on three-loop control. Then, the single-axis and double-axis closed-loop simulation models of the servo feed system were built in Simulink, and the influence pattern of control parameters and nonlinear factors on the dynamic servo error was obtained through simulation analysis. Finally, the validity of the theoretical model for the servo feed system was verified through a comprehensive comparison of simulation and experimental outcomes. This encompasses an analysis of the control system Bode plots, critical stick-slip velocity, and tracking errors in the X-axis with linear motion. The validation provides theoretical guidance for parameter design and mechanical adjustments of the servo feed system in heavy-duty vertical machining centres.
更多查看译文
关键词
dynamic servo error
AI 理解论文
溯源树
样例
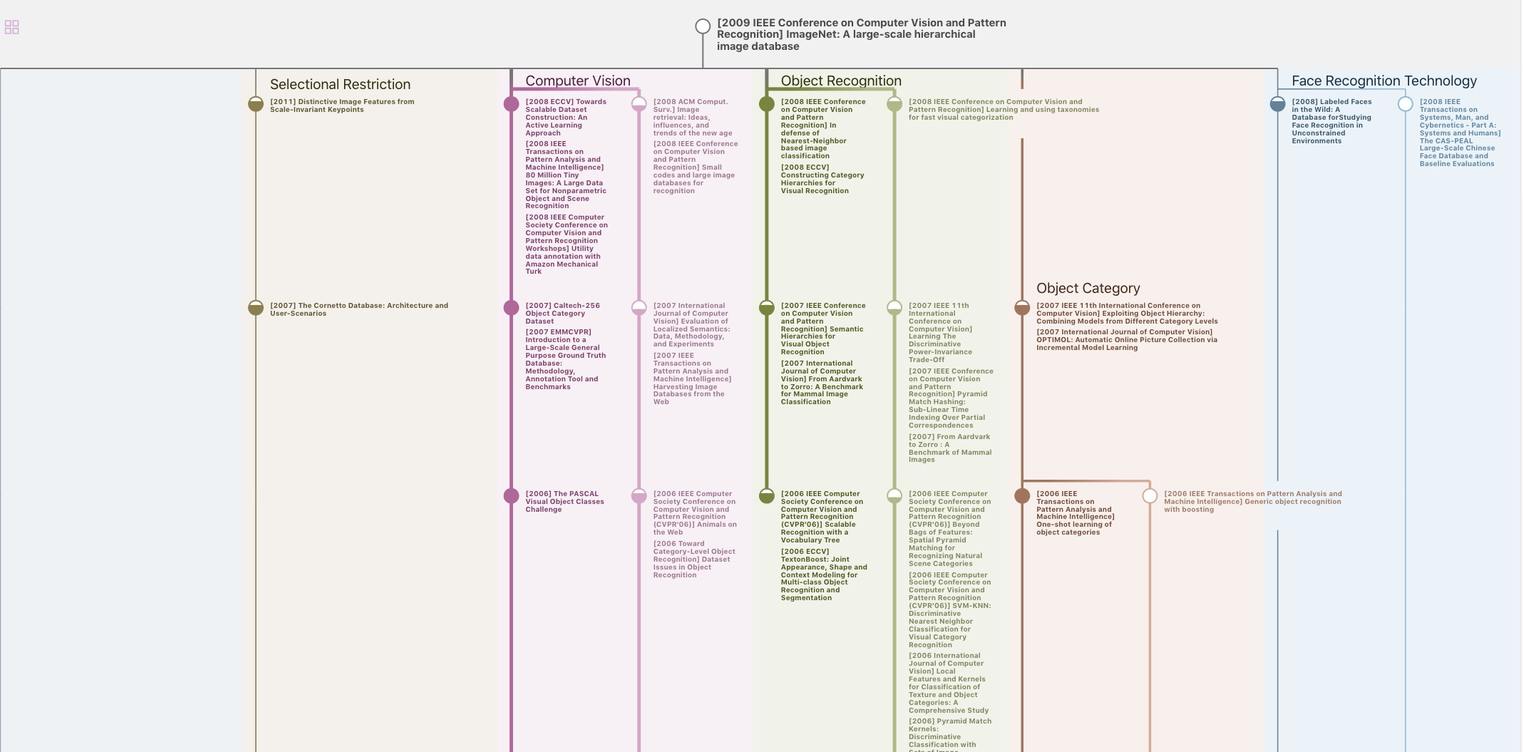
生成溯源树,研究论文发展脉络
Chat Paper
正在生成论文摘要