Numerical Investigation of Oil-Air Flow Inside Tapered Roller Bearings with Oil Bath Lubrication
JOURNAL OF APPLIED FLUID MECHANICS(2024)
摘要
Oil-air flow within an oil bath lubrication tapered roller bearing is essential for the lubrication and cooling of the bearing. In this paper, we develop a simulation model to investigate the flow field of tapered roller bearings with oil bath lubrication. The multiple reference frame (MRF) approach is used to describe the physical motion of the bearing, and the volume of fluid (VOF) two-phase flow model is used to track the oil-air interface in the flow field. The effects of mesh scale, geometric gap, and oil reservoir size on calculation time and convergence accuracy are examined in detail, and the effects of inner ring rotational speed and lubricant viscosity on frictional torque are systematically studied. The results of the numerical simulation indicate that as the gap distance between the raceway and the rolling elements decreases, the frictional torque is mainly generated by churning losses at the inner raceway and the rolling elements. The frictional torque increases with increasing inner ring speed and lubricating oil viscosity, with the rolling element contributing the largest portion at approximately 50% of the total. We demonstrate the effectiveness of a method to reduce frictional torque by optimizing the internal structure of the bearing to control oil flow. By optimizing the cage structure and reducing the roller halfcone angle, frictional torque can be reduced by 29.1% and 26.2%, respectively.
更多查看译文
关键词
Tapered roller bearings,Oil bath lubrication,Two-phase flow,Frictional torque,CFD simulation
AI 理解论文
溯源树
样例
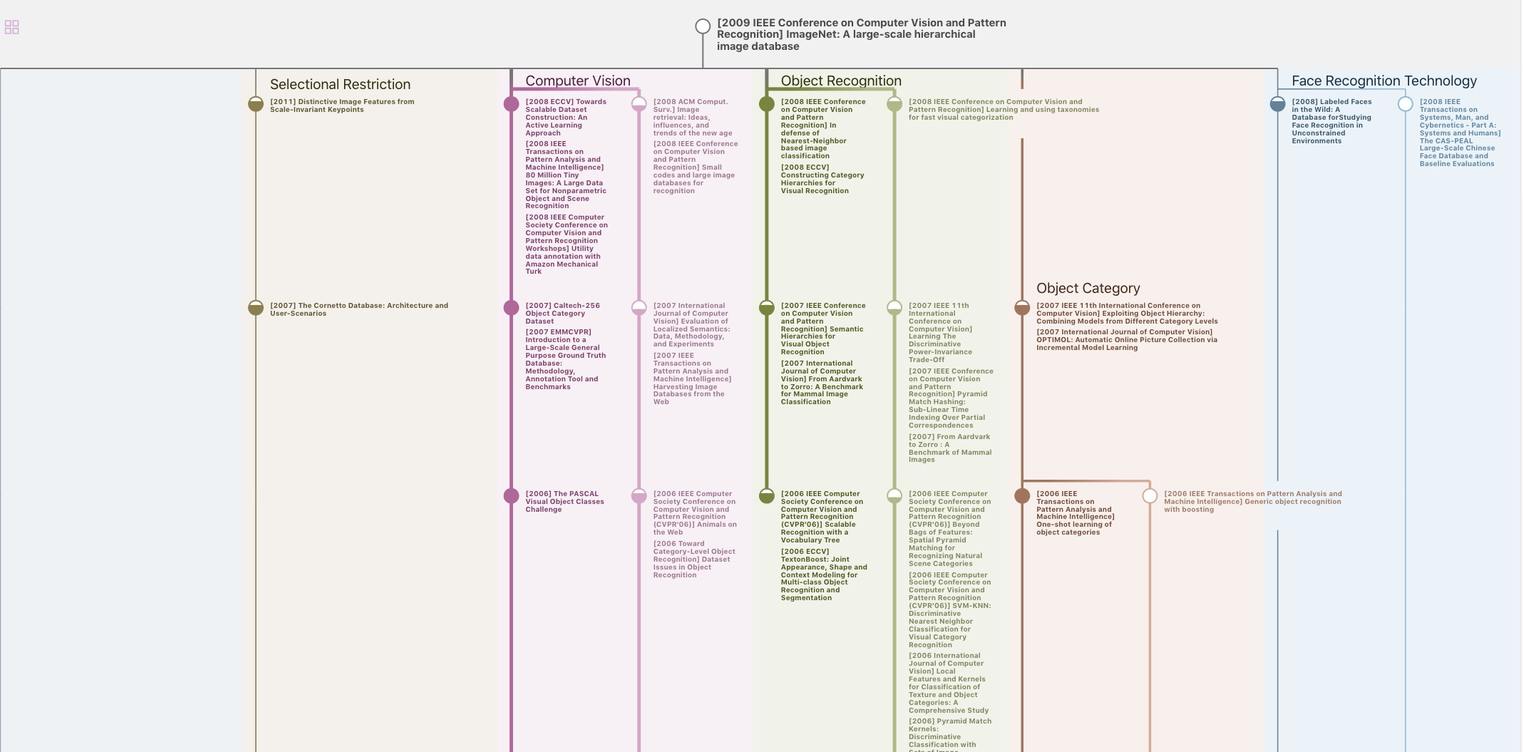
生成溯源树,研究论文发展脉络
Chat Paper
正在生成论文摘要