Optimizing rotary friction welding parameters to attain maximum strength in duplex stainless steel tube joints
MULTISCALE AND MULTIDISCIPLINARY MODELING EXPERIMENTS AND DESIGN(2023)
摘要
Duplex stainless steels (DSS) have excellent strength to resist stress corrosion cracking and also good strength to withstand corrosion. In conventional fusion welding method, unbalanced ferrite–austenite ratios, formation of intermetallic compounds, heat affected zone (HAZ), and weld center having coarse grain structure result in decreasing the impact strength and corrosion resistance of welded joints. Due to all the abovementioned problems, solid-state welding methods have been employed to join the DSS materials. Rotary friction welding (RFW) is a solid-state joining process in which the rubbing action between the surfaces produces heat causing the material to soften, followed by applying a higher lateral force to plastically diffuse and join the materials. The present work investigates the rotary friction welding of DSS 2205 tubes which have 25.4 mm outer diameter, 3 mm thickness, and 60 mm length. The input attributes viz. rotational speed ( N ), friction pressure/time ( F ), and forging pressure/time ( P ) were optimized using Response surface methodology (RSM). The results, when analyzed, indicated that friction pressure and rotational speed are the most significant attributes on the tensile strength of the weld joint quality. At optimized conditions, tensile strength (TS), notch tensile strength (NTS), and impact toughness obtained are 894.796 MPa, 1120 MPa, and 45.733 MPa, respectively.
更多查看译文
关键词
rotary friction,welding,joints,duplex
AI 理解论文
溯源树
样例
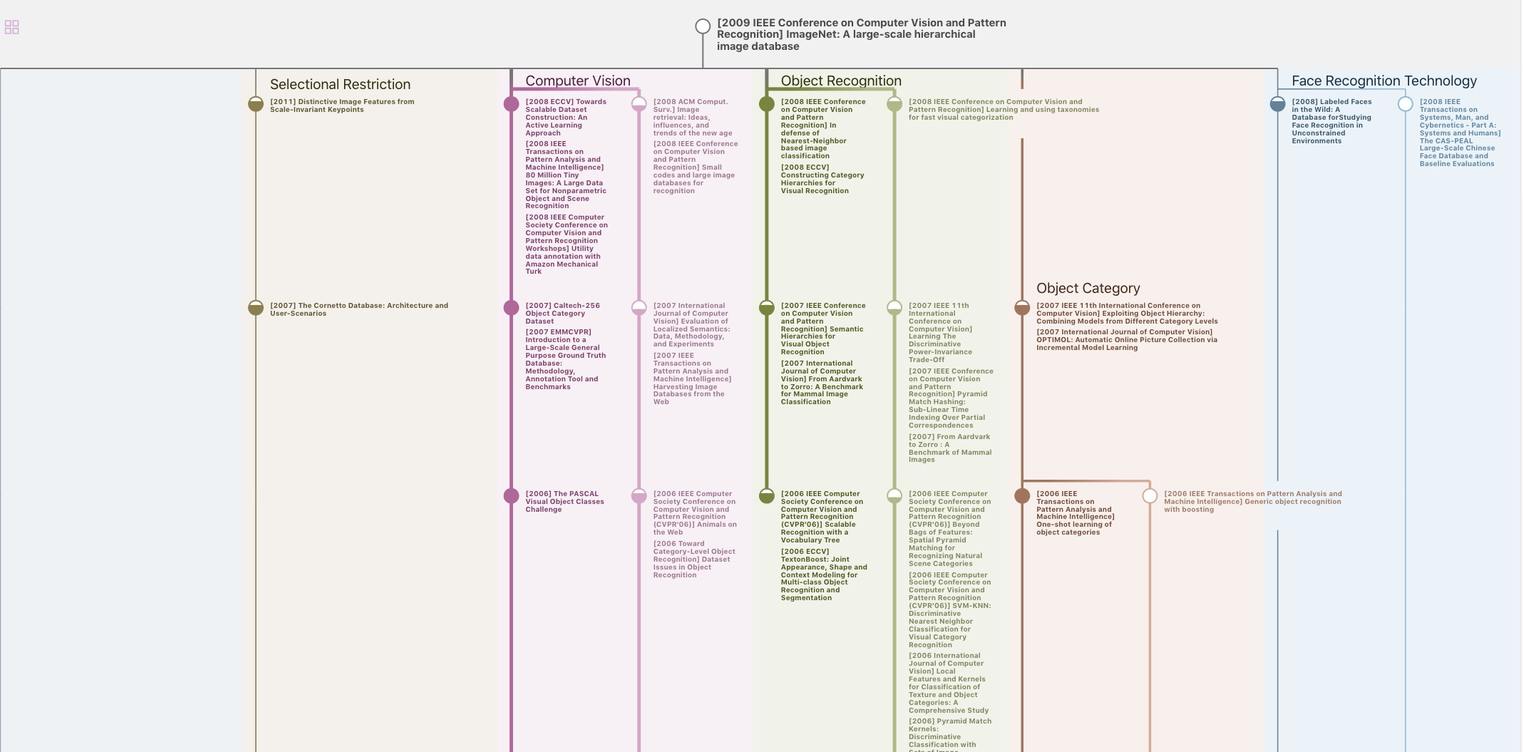
生成溯源树,研究论文发展脉络
Chat Paper
正在生成论文摘要