Investigation on microstructure evolution of hybrid manufactured TC17 titanium alloy during cyclic deformation
MATERIALS SCIENCE AND ENGINEERING A-STRUCTURAL MATERIALS PROPERTIES MICROSTRUCTURE AND PROCESSING(2023)
摘要
In this work, laser direct energy deposition technology was used to produce hybrid manufactured TC17 titanium alloy with wrought substrate. The cyclic deformation behavior in the total strain range of 1.5%, 2.0%, 2.5%, and 3.0% at ambient temperature and dislocation morphology was investigated. The experimental results show that the three specimens represent cyclic softening when the total strain range is large than 1.5%. All the hybrid manufactured specimens are fractured in the deposition zone and the size of the deformated alpha phase decreases with increased strain. Slip transfer between alpha phase and beta matrix and a small amount of dislocation tanglement in beta matrix was observed in the specimen with strain of 1.5% and cyclic hardening. The dislocation density in beta phase increased abruptly when the strain range is 2.5%, which promotes cyclic softening. The heterogeneous deformation between the high and low density dislocation zones formed in the alpha phase of the cyclic softening samples is the cause of the deformation and fracture of the alpha phase. The tension-compression asymmetry under forward and reverse loading revealed the Bauschinger effect in specimens with total strain exceeding 1.5%. Dislocation tanglement promoted cyclic softening by increasing the local back stress, at the same time, the back stress helped easier dislocation movement during reverse loading. Meanwhile, dislocation rearrangement and annihilation reduced the friction stress and further accelerate cyclic softening.
更多查看译文
关键词
Titanium alloy,Laser directly energy deposition,Hybrid manufacturing,Low cycle fatigue,Dislocation movement
AI 理解论文
溯源树
样例
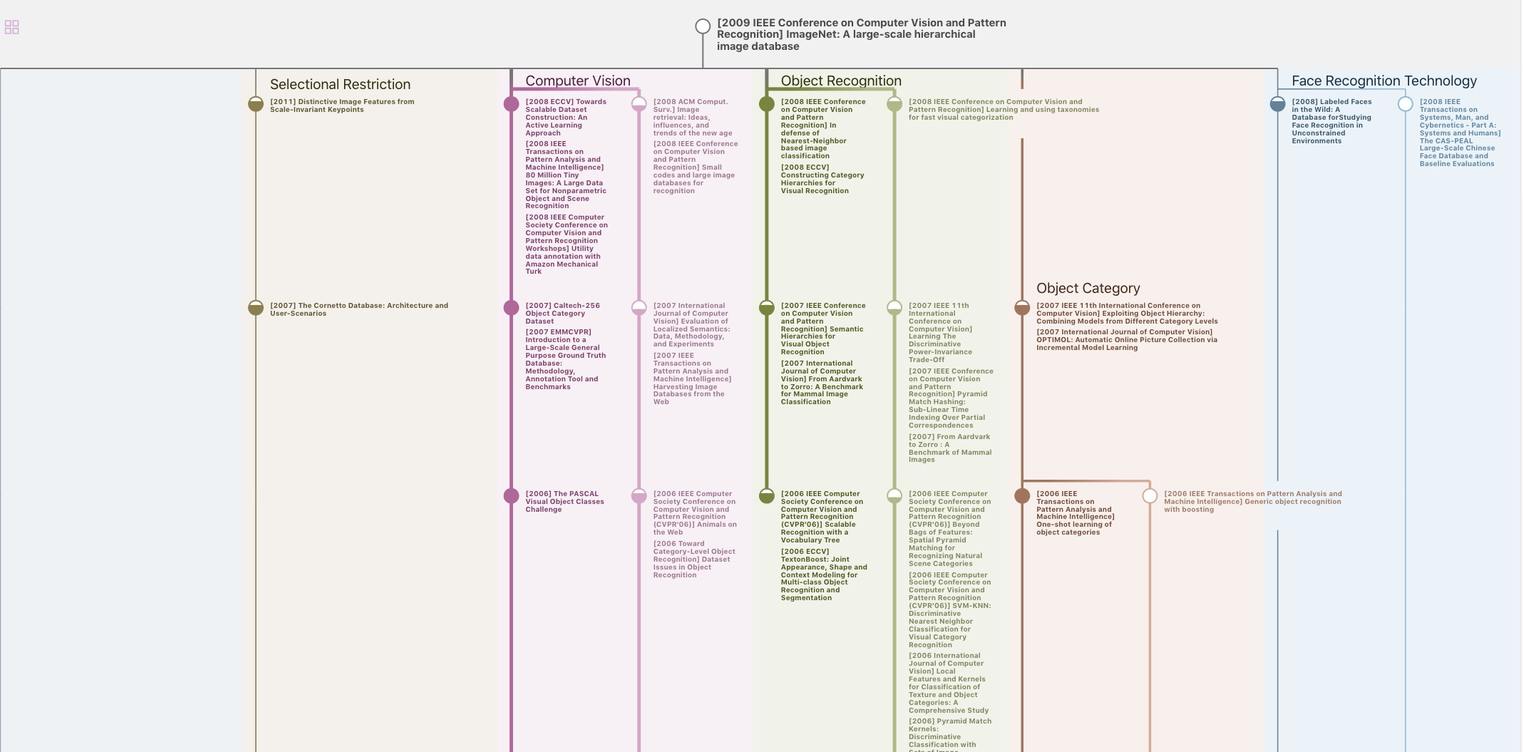
生成溯源树,研究论文发展脉络
Chat Paper
正在生成论文摘要