Influence of Support Material on the Structural Evolution of Copper during Electrochemical CO2 Reduction
Meeting abstracts(2023)
摘要
The electrochemical CO 2 reduction reaction (CO 2 RR) provides the combined benefit of reducing anthropogenic CO 2 emissions while supplying a wide variety of valuable chemical feedstock chemicals. [1] While many transition metals are CO 2 RR active catalysts, only copper can form products requiring more than two electrons in the electrochemical conversion of CO 2 . This includes a multitude of high-value-added products such as ethylene, ethanol, or propanol. [1-3] The selectivity of the CO 2 RR is strongly influenced by the structure and morphology of the copper catalysts. Consequently, structural properties such as copper nanoparticle size, display an influence on CO 2 RR product selectivity. [4] This creates a substantial problem as copper is highly susceptible to reorganization during the electrochemical CO 2 RR, which inhibits the retention of apparently favorable surface structures during the CO 2 RR. [5] As a consequence, structure-selectivity relations can neither be reliably described nor completely understood. This problem is exacerbated by a lack of understanding of the underlying reasons that drive reorganization and therefore degradation of the catalyst. At reductive potentials, as used in the electrochemical CO 2 RR, coalescence and subsequent agglomeration are assumed to be the dominant degradation mechanism, while oxidative potentials generally trigger support corrosion and dissolution. Strategies for stabilization to retain activity and selectivity are therefore essential. Nevertheless their importance in the electrochemical CO 2 RR, stabilization methods are largely missing. For other reactions, such as the oxygen reduction reaction, various studies showed an increase in overall stability by containing the catalysts in a confined space. [6-8] This work presents the stabilizing effect of three different carbon support materials with unique morphologies on copper nanoparticles (CuNPs). Through the use of a non-porous Vulcan, a Ketjenblack with a diverse pore size distribution and highly defined mesoporous graphitic spheres (MGS) with a unimodal pore size distribution, the influence on structural characteristics of the carbon material on the stabilization of the CuNPs can be presented. The representative copper catalysts were prepared by colloidal synthesis or incipient wetness impregnation and evaluated through micro-flow cell measurements with online gas chromatography (GC) analytics and pre-/post catalytic high angle annular dark field scanning transmission electron microscopy (HAADF-STEM), visualizing changes in the catalyst structure and morphology after the reaction. We demonstrate the successful stabilization of CuNPs by pore confinement against particle coalescence and subsequent agglomeration for up to 20 h of electrochemical CO 2 RR conditions, with GC analysis providing great insight into the influence of particle size, morphology, and location of the CuNPs on CO 2 RR product selectivity. Intriguingly, a high share of CO 2 RR products was observed for stabilized < 4 nm CuNPs putting the established particle size effect for the CO 2 RR, where the hydrogen evolution reaction was predominantly observed on nanoparticles below 15 nm, into question. [4] These results present new ways of stabilizing CuNPs and highlight the need for post-catalytic evaluation of the catalysts' morphological state to precisely derive performance-structure indicators. Work accepted and soon to be published in ChemElectroChem doi.org/10.1002/celc.202200924 Literature: [1] S. Nitopi, E. Bertheussen, S. B. Scott, X. Liu, A. K. Engstfeld, S. Horch, B. Seger, I. E. L. Stephens, K. Chan, C. Hahn, J. K. Nørskov, T. F. Jaramollo, I. Chorkendorff, Chem Rev. 2019 , 119, 7610–7672. [2] Y. Hori, Modern Aspects of Electrochemistry No. 42, Springer, 2008 . [3] K. P. Kuhl, E. R. Cave, D. N. Abram, T. F. Jaramillo, Energy Environ. Sci . 2012 , 5, 7050–7059. [4] R. Reske, H. Mistry, F. Behafarid, B. Roldan Cuenya, P. Strasser, J. Am. Chem. Soc. 2014 , 136, 6978–6986. [5] W. T. Osowiecki, J. J. Nussbaum, G. A. Kamat, G. Katsoukis, M. Ledendecker, H. Frei, A. T. Bell, A. P. Alivisatos, ACS Appl. Energy Mater. 2019 , 2, 7744–7749. [6] Y. Li, F. Cui, M. B. Ross, D. Kim, Y. Sun, P. Yang, Nano Lett. 2017 , 1312–1317. [7] Y. T. Guntern, J. R. Pankhurst, J. Vavra, M. Mensi, V. Mantella, P. Schouwink, R. Buonsanti, Angew. Chem. 2019 , 131, 12762–12769. [8] C. Galeano, J. C. Meier, V. Peinecke, H. Bongard, I. Katsounaros, A. A. Topalov, A. Lu, K. J. J. Mayrhofer, F. Schüth, J. Am. Chem. Soc. 2012 , 134, 20457 – 20465. Figure 1
更多查看译文
关键词
electrochemical copper
AI 理解论文
溯源树
样例
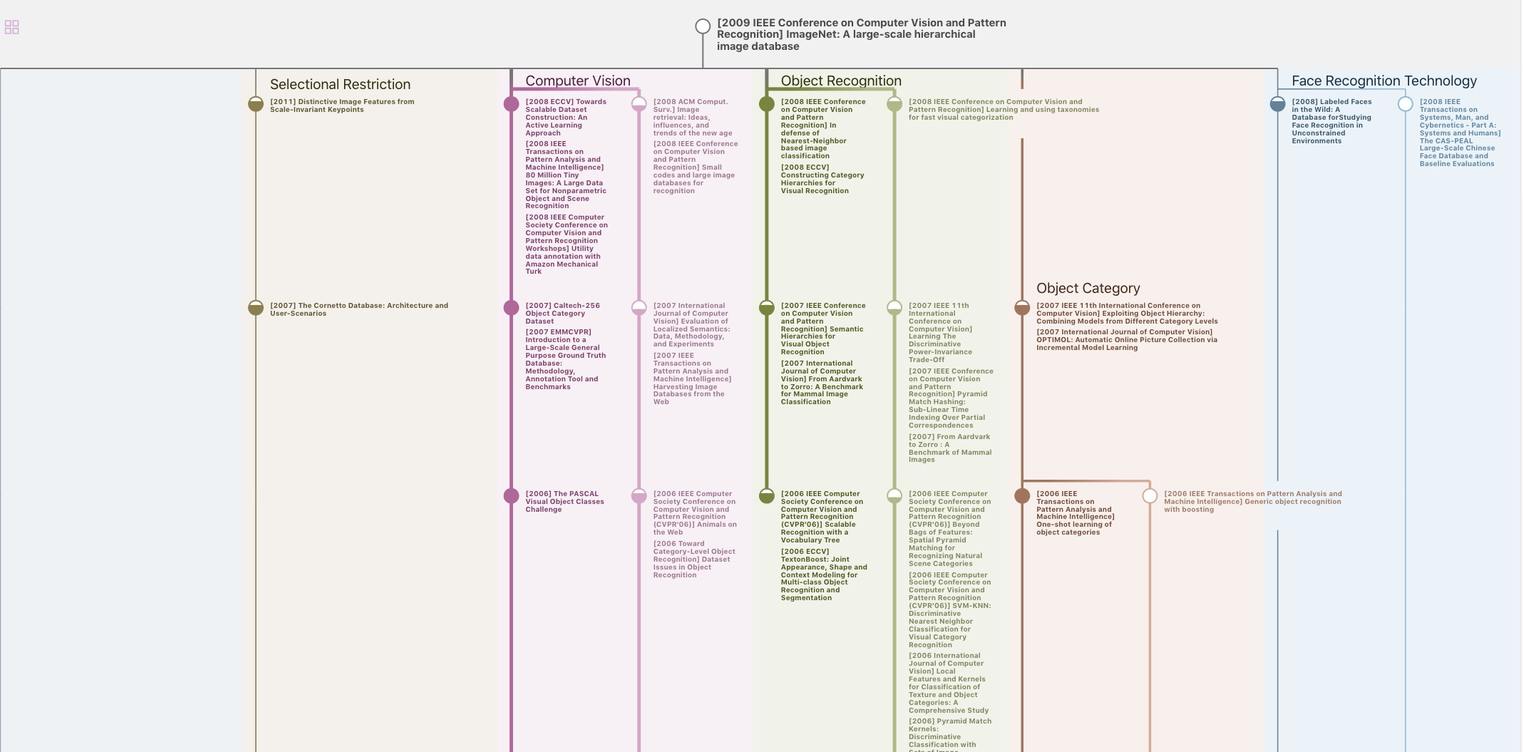
生成溯源树,研究论文发展脉络
Chat Paper
正在生成论文摘要